Photonicare Adopts Medical Device QMS Software to Accelerate Time to Market
Customer Company Size
SME
Region
- America
Country
- United States
Product
- Greenlight Guru
- TomiScope
Tech Stack
- Cloud-based Quality Management System
Implementation Scale
- Enterprise-wide Deployment
Impact Metrics
- Productivity Improvements
- Customer Satisfaction
- Digital Expertise
Technology Category
- Functional Applications - Computerized Maintenance Management Systems (CMMS)
- Functional Applications - Enterprise Resource Planning Systems (ERP)
- Functional Applications - Product Lifecycle Management Systems (PLM)
Applicable Industries
- Healthcare & Hospitals
- Life Sciences
Applicable Functions
- Quality Assurance
- Product Research & Development
Use Cases
- Regulatory Compliance Monitoring
- Remote Collaboration
Services
- System Integration
- Training
About The Customer
Photonicare is an early-stage medical device company based in Champaign, IL, focused on providing physicians with better tools to make better treatment decisions and provide better care for children who suffer from ear infections. The company is led by Ryan Shelton, Ph.D., Co-Founder & CEO, Ryan Nolan, Co-Founder/ VP of Clinical Operations, and Heather Howard, Biomedical Engineer II. Their primary device, the TomiScope, uses ultrasound-related technology to visualize the middle ear for physicians to confidently diagnose middle ear infections. The company initially targeted the USA market and started from scratch with their quality management system. The team at Photonicare is known for wearing multiple hats throughout the production of their device, which requires documenting product development and quality activities. They sought a cloud-based, purpose-built solution to improve internal team efficiencies and maintain their agility.
The Challenge
At Photonicare, the team was always wearing different hats to maintain their agility, and implementing a paper-based quality system seemed like a retroactive solution. They believed such a solution would ultimately lead to more inefficiencies and time spent on manually documenting product and quality activities where quality could slip through the cracks. In order to avoid this, they began searching for a cloud-based, purpose-built solution that would contribute to improving their internal team efficiencies and maintaining their agility. As an early-stage company, the team at Photonicare is always looking for ways to improve their efficiencies while maintaining their agility. Ryan Nolan, Co-founder and VP of Clinical Operations, recalls their antiquated way of doing things in the beginning when it came to documenting things on paper. As a result of having to wear multiple hats and juggle competing priorities at a startup, they reached a point where their documents weren't as organized as they wanted them to be. Knowing this antiquated way was a time-consuming solution for managing documentation and quality processes, Ryan and the team at Photonicare began searching for a purpose-built solution that was as agile as their team.
The Solution
The team at Photonicare was looking for a medical device quality management system (MDQMS) that would be intuitive and nimble. During their search, Photonicare discovered the value of in-app controls and guidance from medical device industry experts that assured they would produce a high-quality FDA submission. After deciding to adopt Greenlight Guru, their team is now able to see all of their design controls in one place and can identify existing holes that need to be filled. Since they have been generating numerous documents and preparing their FDA submission, Heather finds value in being able to route documents electronically for necessary signatures so that she can focus on higher-value day-to-day activities. Ryan highlighted that having industry experts from the Greenlight Guru Customer Success team at their disposal helped them easily implement an MDQMS and jump-start their documentation efforts. Heather finds having a pre-existing Design History File (DHF) in Greenlight Guru is a “huge relief” that has eliminated the countless hours of manually preparing a DHF for their FDA submission. Their team believes that partnering with Greenlight Guru has been a competitive advantage for Photonicare – allowing them to get through different stages of development at a much faster pace than a paper-based system would have.
Operational Impact
Quantitative Benefit
Case Study missing?
Start adding your own!
Register with your work email and create a new case study profile for your business.
Related Case Studies.
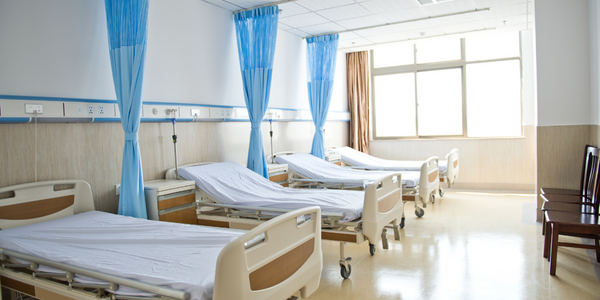
Case Study
Hospital Inventory Management
The hospital supply chain team is responsible for ensuring that the right medical supplies are readily available to clinicians when and where needed, and to do so in the most efficient manner possible. However, many of the systems and processes in use at the cancer center for supply chain management were not best suited to support these goals. Barcoding technology, a commonly used method for inventory management of medical supplies, is labor intensive, time consuming, does not provide real-time visibility into inventory levels and can be prone to error. Consequently, the lack of accurate and real-time visibility into inventory levels across multiple supply rooms in multiple hospital facilities creates additional inefficiency in the system causing over-ordering, hoarding, and wasted supplies. Other sources of waste and cost were also identified as candidates for improvement. Existing systems and processes did not provide adequate security for high-cost inventory within the hospital, which was another driver of cost. A lack of visibility into expiration dates for supplies resulted in supplies being wasted due to past expiry dates. Storage of supplies was also a key consideration given the location of the cancer center’s facilities in a dense urban setting, where space is always at a premium. In order to address the challenges outlined above, the hospital sought a solution that would provide real-time inventory information with high levels of accuracy, reduce the level of manual effort required and enable data driven decision making to ensure that the right supplies were readily available to clinicians in the right location at the right time.
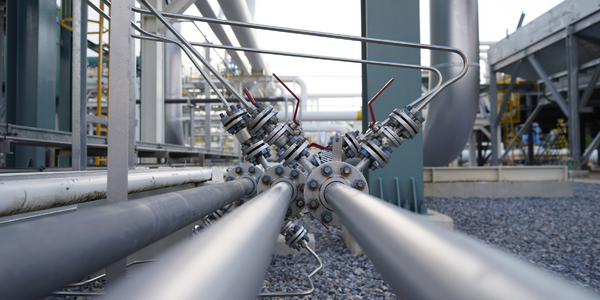
Case Study
Gas Pipeline Monitoring System for Hospitals
This system integrator focuses on providing centralized gas pipeline monitoring systems for hospitals. The service they provide makes it possible for hospitals to reduce both maintenance and labor costs. Since hospitals may not have an existing network suitable for this type of system, GPRS communication provides an easy and ready-to-use solution for remote, distributed monitoring systems System Requirements - GPRS communication - Seamless connection with SCADA software - Simple, front-end control capability - Expandable I/O channels - Combine AI, DI, and DO channels
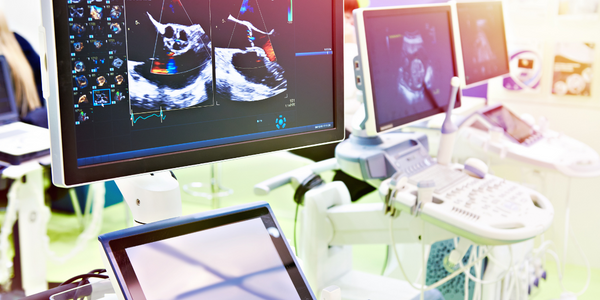
Case Study
Driving Digital Transformations for Vitro Diagnostic Medical Devices
Diagnostic devices play a vital role in helping to improve healthcare delivery. In fact, an estimated 60 percent of the world’s medical decisions are made with support from in vitrodiagnostics (IVD) solutions, such as those provided by Roche Diagnostics, an industry leader. As the demand for medical diagnostic services grows rapidly in hospitals and clinics across China, so does the market for IVD solutions. In addition, the typically high cost of these diagnostic devices means that comprehensive post-sales services are needed. Wanteed to improve three portions of thr IVD:1. Remotely monitor and manage IVD devices as fixed assets.2. Optimizing device availability with predictive maintenance.3. Recommending the best IVD solution for a customer’s needs.
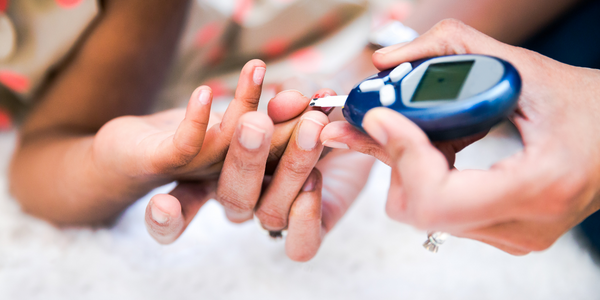
Case Study
HaemoCloud Global Blood Management System
1) Deliver a connected digital product system to protect and increase the differentiated value of Haemonetics blood and plasma solutions. 2) Improve patient outcomes by increasing the efficiency of blood supply flows. 3) Navigate and satisfy a complex web of global regulatory compliance requirements. 4) Reduce costly and labor-intensive maintenance procedures.
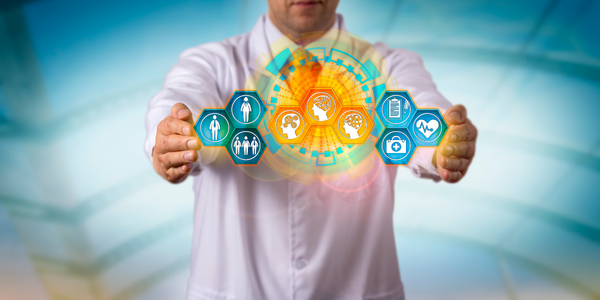
Case Study
Harnessing real-time data to give a holistic picture of patient health
Every day, vast quantities of data are collected about patients as they pass through health service organizations—from operational data such as treatment history and medications to physiological data captured by medical devices. The insights hidden within this treasure trove of data can be used to support more personalized treatments, more accurate diagnosis and more advanced preparative care. But since the information is generated faster than most organizations can consume it, unlocking the power of this big data can be a struggle. This type of predictive approach not only improves patient care—it also helps to reduce costs, because in the healthcare industry, prevention is almost always more cost-effective than treatment. However, collecting, analyzing and presenting these data-streams in a way that clinicians can easily understand can pose a significant technical challenge.