Petrochemical Plant Troubleshoots with Aspen Plus and Saves $2.4M USD per Year
Customer Company Size
Large Corporate
Region
- Asia
Country
- India
Product
- Aspen Plus
- Aspen HYSYS
- Aspen Capital Cost Estimator (ACCE)
Tech Stack
- AspenTech Software
Implementation Scale
- Enterprise-wide Deployment
Impact Metrics
- Cost Savings
- Productivity Improvements
Technology Category
- Analytics & Modeling - Process Analytics
- Application Infrastructure & Middleware - Data Exchange & Integration
Applicable Industries
- Oil & Gas
- Chemicals
Applicable Functions
- Process Manufacturing
Use Cases
- Process Control & Optimization
- Predictive Maintenance
Services
- Software Design & Engineering Services
About The Customer
Reliance Industries Limited is an Indian conglomerate holding company. The company's businesses span across various sectors including hydrocarbon exploration and production, petroleum refining and marketing, petrochemicals, retail, and telecommunications. They strive to maintain innovation-led growth in each of these areas and aim to achieve global leadership by maintaining their position as the largest polyester yarn and fiber producer in the world and a leading producer of ultra-clean fuels. Reliance Industries uses the aspenONE Engineering suite of products in many of their businesses when designing new plants, revamping existing plants, and troubleshooting underperforming units.
The Challenge
Reliance Industries Limited, an Indian conglomerate holding company, faced a challenge with their toluene separation process. The existing benzene separation column was underperforming, with the benzene content in the bottoms being higher than the required 200 ppm. This resulted in an unsuccessful planned revamp for benzene-toluene separation. The vendor was unable to offer a viable solution to the underperforming column, stating the column was too tightly designed resulting in offsite processing of the benzene column bottoms containing toluene and heavies. Following the shutdown of the offsite processing facility, the revamp for benzene-toluene became essential. Because of heavy losses due to the lack of a local toluene separation facility, an urgent revamp became critical.
The Solution
Reliance turned to Aspen Plus and the hydraulic modeling capabilities to troubleshoot the underperforming column and find a viable alternative. This was completed in-house, avoiding the costs and delay associated with getting help from an outside simulation expert. Using Aspen Plus and plant data, Reliance built a model rigorous enough to correctly explain what was occurring in the underperforming unit. They determined that poor benzene-toluene separation tower efficiency was the reason and found the benzene column to be hydraulically limited. Since the separation column required more trays to reach the required performance, a redundant column was identified as a potential alternative to avoid column replacement or re-traying, which would result in further losses in production. By confirming that the redundant column could be used as a stripper and reconfiguring the two columns, Reliance could effectively reach the required separation and locally separate the toluene.
Operational Impact
Quantitative Benefit
Case Study missing?
Start adding your own!
Register with your work email and create a new case study profile for your business.
Related Case Studies.

Case Study
Taking Oil and Gas Exploration to the Next Level
DownUnder GeoSolutions (DUG) wanted to increase computing performance by 5 to 10 times to improve seismic processing. The solution must build on current architecture software investments without sacrificing existing software and scale computing without scaling IT infrastructure costs.

Case Study
Remote Wellhead Monitoring
Each wellhead was equipped with various sensors and meters that needed to be monitored and controlled from a central HMI, often miles away from the assets in the field. Redundant solar and wind generators were installed at each wellhead to support the electrical needs of the pumpstations, temperature meters, cameras, and cellular modules. In addition to asset management and remote control capabilities, data logging for remote surveillance and alarm notifications was a key demand from the customer. Terra Ferma’s solution needed to be power efficient, reliable, and capable of supporting high-bandwidth data-feeds. They needed a multi-link cellular connection to a central server that sustained reliable and redundant monitoring and control of flow meters, temperature sensors, power supply, and event-logging; including video and image files. This open-standard network needed to interface with the existing SCADA and proprietary network management software.

Case Study
Refinery Saves Over $700,000 with Smart Wireless
One of the largest petroleum refineries in the world is equipped to refine various types of crude oil and manufacture various grades of fuel from motor gasoline to Aviation Turbine Fuel. Due to wear and tear, eight hydrogen valves in each refinery were leaking, and each cost $1800 per ton of hydrogen vented. The plant also had leakage on nearly 30 flare control hydrocarbon valves. The refinery wanted a continuous, online monitoring system that could catch leaks early, minimize hydrogen and hydrocarbon production losses, and improve safety for maintenance.
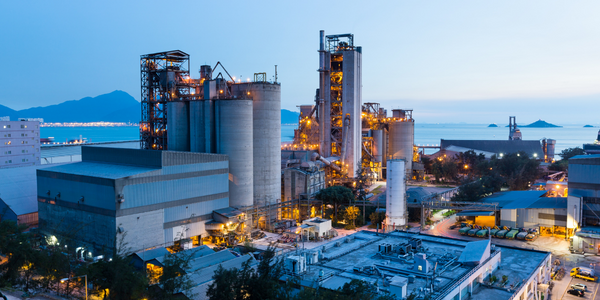
Case Study
Honeywell - Tata Chemicals Improves Data Accessibility with OneWireless
Tata was facing data accessibility challenges in the cement plant control room tapping signals from remote process control areas and other distant locations, including the gas scrubber. Tata needed a wireless solution to extend its control network securely to remote locations that would also provide seamless communication with existing control applications.