Company Size
1,000+
Region
- America
Country
- Other
Product
- Blue Yonder's demand planning capabilities
- Blue Yonder's fulfillment capabilities
Tech Stack
- Supply Chain Management Software
- Inventory Optimization Software
Implementation Scale
- Enterprise-wide Deployment
Impact Metrics
- Cost Savings
- Productivity Improvements
Technology Category
- Functional Applications - Enterprise Resource Planning Systems (ERP)
- Functional Applications - Inventory Management Systems
Applicable Industries
- Food & Beverage
Applicable Functions
- Logistics & Transportation
- Warehouse & Inventory Management
Use Cases
- Inventory Management
- Supply Chain Visibility
Services
- Software Design & Engineering Services
- System Integration
About The Customer
With $7.2 billion in annual sales, PepsiCo Latin America employs more than 70,000 people in 34 countries. Its beverage, food and snack products include major global brands such as Pepsi, Quaker, Lays and Gatorade as well as brands tailored to regional and local markets. The company was looking for a solution that could help it manage its supply chain more efficiently, reduce costs, and improve forecast accuracy.
The Challenge
PepsiCo Latin America, a long-time Blue Yonder customer, was seeking a customer-focused and perfectly synchronized value chain, supported by standardized usage of its supply planning and execution solutions across 16 countries. As demand variability, materials costs and transportation expenses increased, this value chain would enable greater speed, accuracy and responsiveness. The company was looking for a solution that could integrate and roll out its solutions in demand planning, supply planning, inventory optimization, shipment scheduling and promotions across 34 countries.
The Solution
PepsiCo Latin America partnered with Blue Yonder to integrate and roll out its solutions in demand planning, supply planning, inventory optimization, shipment scheduling and promotions across 34 countries. Horizon, the largest supply chain transformation effort in the company’s history, seeks to transform supply chain planning, as well as automate and integrate all the processes that comprise it. Blue Yonder’s demand planning capabilities consolidate and synchronize demand signals, as well as external variables, across PepsiCo Latin America’s diverse markets. The company can make more accurate, profitable decisions, from inventory staging to maximizing usage of manufacturing resources. Fulfillment capabilities from Blue Yonder help PepsiCo Latin America balance all the factors that determine inventory placement, including demand signals, customer service targets, safety-stock policies and shelf-life constraints — all while keeping inventory costs low.
Operational Impact
Quantitative Benefit
Case Study missing?
Start adding your own!
Register with your work email and create a new case study profile for your business.
Related Case Studies.

Case Study
The Kellogg Company
Kellogg keeps a close eye on its trade spend, analyzing large volumes of data and running complex simulations to predict which promotional activities will be the most effective. Kellogg needed to decrease the trade spend but its traditional relational database on premises could not keep up with the pace of demand.

Case Study
HEINEKEN Uses the Cloud to Reach 10.5 Million Consumers
For 2012 campaign, the Bond promotion, it planned to launch the campaign at the same time everywhere on the planet. That created unprecedented challenges for HEINEKEN—nowhere more so than in its technology operation. The primary digital content for the campaign was a 100-megabyte movie that had to play flawlessly for millions of viewers worldwide. After all, Bond never fails. No one was going to tolerate a technology failure that might bruise his brand.Previously, HEINEKEN had supported digital media at its outsourced datacenter. But that datacenter lacked the computing resources HEINEKEN needed, and building them—especially to support peak traffic that would total millions of simultaneous hits—would have been both time-consuming and expensive. Nor would it have provided the geographic reach that HEINEKEN needed to minimize latency worldwide.

Case Study
Energy Management System at Sugar Industry
The company wanted to use the information from the system to claim under the renewable energy certificate scheme. The benefit to the company under the renewable energy certificates is Rs 75 million a year. To enable the above, an end-to-end solution for load monitoring, consumption monitoring, online data monitoring, automatic meter data acquisition which can be exported to SAP and other applications is required.

Case Study
Coca Cola Swaziland Conco Case Study
Coco Cola Swaziland, South Africa would like to find a solution that would enable the following results: - Reduce energy consumption by 20% in one year. - Formulate a series of strategic initiatives that would enlist the commitment of corporate management and create employee awareness while helping meet departmental targets and investing in tools that assist with energy management. - Formulate a series of tactical initiatives that would optimize energy usage on the shop floor. These would include charging forklifts and running cold rooms only during off-peak periods, running the dust extractors only during working hours and basing lights and air-conditioning on someone’s presence. - Increase visibility into the factory and other processes. - Enable limited, non-intrusive control functions for certain processes.

Case Study
Temperature Monitoring for Restaurant Food Storage
When it came to implementing a solution, Mr. Nesbitt had an idea of what functionality that he wanted. Although not mandated by Health Canada, Mr. Nesbitt wanted to ensure quality control issues met the highest possible standards as part of his commitment to top-of-class food services. This wish list included an easy-to use temperature-monitoring system that could provide a visible display of the temperatures of all of his refrigerators and freezers, including historical information so that he could review the performance of his equipment. It also had to provide alert notification (but email alerts and SMS text message alerts) to alert key staff in the event that a cooling system was exceeding pre-set warning limits.
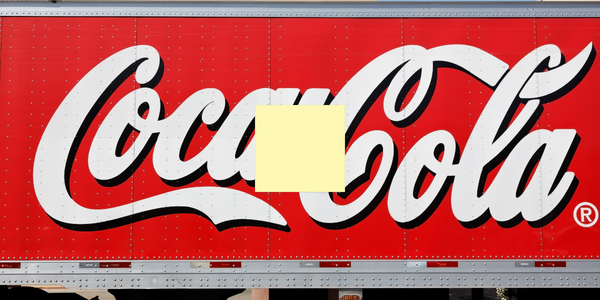
Case Study
Coca-Cola Refreshments, U.S.
Coca-Cola Refreshments owns and manages Coca-Cola branded refrigerators in retail establishments. Legacy systems were used to locate equipment information by logging onto multiple servers which took up to 8 hours to update information on 30-40 units. The company had no overall visibility into equipment status or maintenance history.