PEDG Rocks the iHeartRadio Music Festival & NFL Kickoff
Customer Company Size
SME
Region
- America
Country
- United States
Product
- Vectorworks Designer
- AutoCAD
Tech Stack
- CAD Software
- Vectorworks
- AutoCAD
Implementation Scale
- Enterprise-wide Deployment
Impact Metrics
- Customer Satisfaction
- Innovation Output
- Productivity Improvements
Technology Category
- Application Infrastructure & Middleware - Data Visualization
- Application Infrastructure & Middleware - Data Exchange & Integration
Applicable Functions
- Business Operation
- Facility Management
Use Cases
- Remote Collaboration
- Visual Quality Detection
Services
- System Integration
- Software Design & Engineering Services
About The Customer
Performance Environment Design Group LLC (PEDG) is a scenic and lighting design company known for its transformational designs and industry accolades, including the Telly Award, Eddie Award, and Tour Link Top Dog Award for lighting design. With offices in Lancaster, Pennsylvania, and Los Angeles, PEDG has worked on high-profile events such as the NHL Winter Classic, Pepsi Fan Jam, MTV’s Iggy Awards, and A-list concerts. Their attention to detail and quality work have made them a go-to choice for clients like the iHeartRadio Music Festival and the NFL Kickoff event. PEDG's designs are known for their powerful, artful landscapes of light, fabric, video, and sound, delighting and inspiring audiences.
The Challenge
PEDG faced several challenges while planning the 2012 iHeartRadio event at the MGM Grand in Las Vegas. The logistics of accommodating 22 world-famous musicians and improving upon the previous year's show with a similar budget were significant hurdles. Additionally, the team lost three installation days due to a tight timeline, which didn't allow enough time to scale the show. The team had to ensure that every detail was perfect to avoid delays, as a single misstep could back up the entire project. They also had to contend with discrepancies in the initial AutoCAD drawings provided by the MGM Grand, which required them to travel to the site to measure it themselves.
The Solution
PEDG used Vectorworks Designer software, along with a few other applications, to coordinate the artists' needs and find cost-saving measures to meet the budget. The team spent a lot of time in the CAD program ironing out details to ensure everything fit perfectly. They began with AutoCAD drawings from the MGM Grand but had to create accurate drawings in Vectorworks after finding discrepancies. The program helped them manage all aspects of production, including occupancies, scenic, audio, and video elements. PEDG produced detailed drawings to communicate requirements and quantify components, ensuring everything was calculated down to the last detail. This meticulous planning allowed them to build the iHeartRadio set in three days, rehearse on the fourth day, and hold concerts on the fifth and sixth days.
Operational Impact
Quantitative Benefit
Case Study missing?
Start adding your own!
Register with your work email and create a new case study profile for your business.
Related Case Studies.

Case Study
Premium Appliance Producer Innovates with Internet of Everything
Sub-Zero faced the largest product launch in the company’s history:It wanted to launch 60 new products as scheduled while simultaneously opening a new “greenfield” production facility, yet still adhering to stringent quality requirements and manage issues from new supply-chain partners. A the same time, it wanted to increase staff productivity time and collaboration while reducing travel and costs.
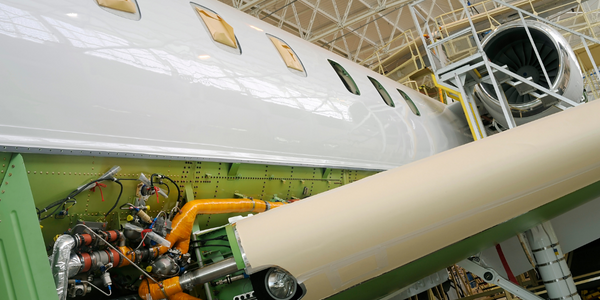
Case Study
Aerospace & Defense Case Study Airbus
For the development of its new wide-body aircraft, Airbus needed to ensure quality and consistency across all internal and external stakeholders. Airbus had many challenges including a very aggressive development schedule and the need to ramp up production quickly to satisfy their delivery commitments. The lack of communication extended design time and introduced errors that drove up costs.
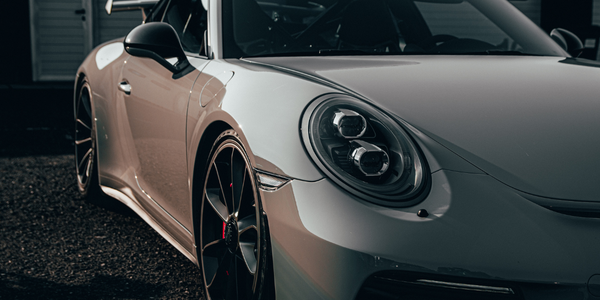
Case Study
Porsche Announces Augmented Reality at Scale, Powered by Atheer
The usual practice for car repairs at a Porsche car dealership is to have a factory representative or regional engineer visit to help diagnose the problem, and sometimes a faulty assembly is shipped back to company HQ for damage analysis. All that costs time and money for customers and dealers alike.
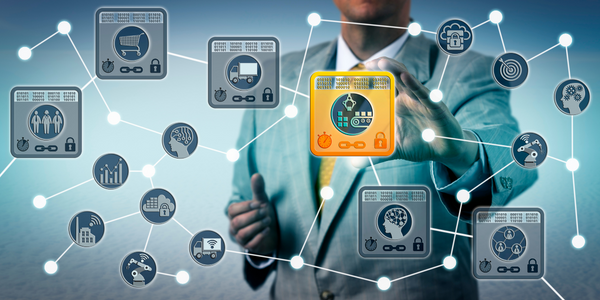
Case Study
Covisint Improves Mitsubishi's Collaboration With Its Supply Chain
Mitsubishi sought to improve supplier relationships on a global basis and to offer an easy-to-use solution to interact with them. In August 2004, Mitsubishi selected Covisint’s platform to help improve sharing of information and collaborative business processes with its global suppliers. Covisint enabled Mitsubishi to provide its suppliers with immediate access to information and applications to obtain more collaborative working relationships
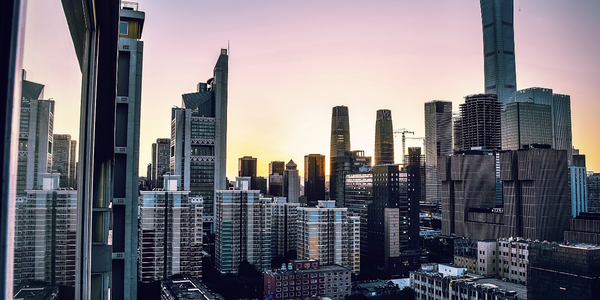
Case Study
Rapid and Simple Installation Provides Access to Critical Data
The customer needed to monitor non-contact alignment and non-contact process temperature in different positions along a 100-meter production line. Space around the line is tight and operators and forklift trucks are passing by constantly. Installation of correctly routed cables from sensors back to the control station would have been expensive and would have taken too long and caused too much disruption to ongoing operations.
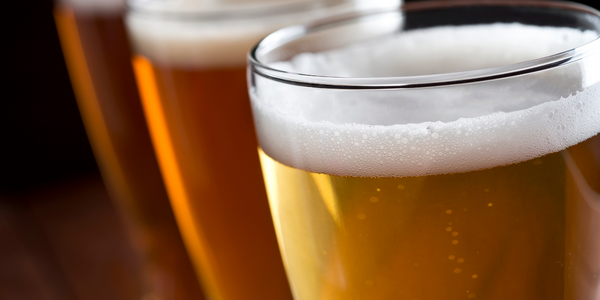
Case Study
Beer Distributor Improves Security, Shipping Capacity, and Service
Enjoy a beer on the upper Texas Gulf Coast, and you can probably thank Del Papa Distributing Company. Founded more than a century ago, the company today distributes 10 million cases of beer annually, from 30 suppliers. More than 375 employees work at headquarters in Texas City and two other distribution centers. The family-owned company has a simple aim: to be a great beer distribution company. So when Del Papa set out to build a new 27-acre headquarters, company leaders thought about how technology could contribute to its greatness. “We wanted the new distribution center to have a single, secure network we could use for physical security, communications, collaboration, and even monitoring the temperature of our inventory,” says Steve Holtsclaw, Manager of Information Systems for Del Papa. The old building, in contrast, had separate networks for voice, data, video, and physical security. Separate networks were expensive and got in the way of business. For example, personnel could only monitor video surveillance cameras from certain workstations. And Wi-Fi performance in the warehouse area wasn’t reliable enough for the voice-activated order-picking system.