Technology Category
- Application Infrastructure & Middleware - Data Visualization
- Platform as a Service (PaaS) - Application Development Platforms
Applicable Industries
- Automotive
- Electronics
Applicable Functions
- Logistics & Transportation
Use Cases
- Continuous Emission Monitoring Systems
- Demand Planning & Forecasting
Services
- System Integration
About The Customer
The customer is a leading producer of rolled aluminium and a global leader in beverage can recycling. They serve a wide range of industries including automotive, consumer electronics, construction, foil and packaging. The company has a complex, multi-stage production process that includes both internal and external operations. They are committed to sustainability and are actively seeking ways to reduce their carbon emissions. The company is also focused on improving their operational efficiency and performance, and they are leveraging digital transformation to achieve these goals.
The Challenge
The case study revolves around a leading producer of rolled aluminium and a global leader in beverage can recycling, which also serves customers in automotive, consumer electronics, construction, foil and packaging. The company has a complex, multi-stage production process that includes both internal and external operations. The challenge was to align these operations to maximize performance and streamline production. The company was also looking to reduce its carbon emissions. The planning processes were previously carried out via Excel, which was not efficient enough. The flow of information between the company and its operational partners was also crucial for driving performance improvements.
The Solution
The company adopted o9’s Supply Planning to match supply and demand across operational steps, visualize the plan, and enable reporting. This solution helped ensure orders were fulfilled on-time and in-full (OTIF) and proactively identified resolutions to disruptions that may impact performance. The company also integrated with o9’s open, cloud-native platform to establish better and more consistent data exchanges between internal and external operations. To minimize downtime, o9 implemented a third-party LP solver to create optimal production plans that sequence internal and external production operations. The company also used o9 to monitor and manage carbon emissions, reducing the volume of CO2 produced throughout production.
Operational Impact
Quantitative Benefit
Case Study missing?
Start adding your own!
Register with your work email and create a new case study profile for your business.
Related Case Studies.

Case Study
Remote Temperature Monitoring of Perishable Goods Saves Money
RMONI was facing temperature monitoring challenges in a cold chain business. A cold chain must be established and maintained to ensure goods have been properly refrigerated during every step of the process, making temperature monitoring a critical business function. Manual registration practice can be very costly, labor intensive and prone to mistakes.
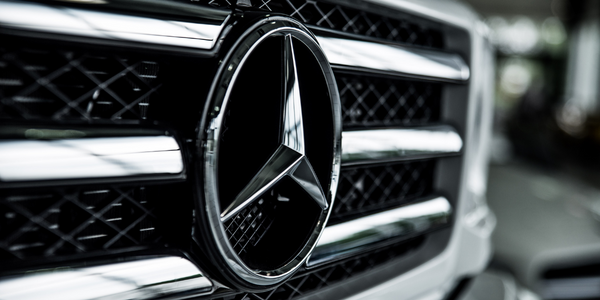
Case Study
Integral Plant Maintenance
Mercedes-Benz and his partner GAZ chose Siemens to be its maintenance partner at a new engine plant in Yaroslavl, Russia. The new plant offers a capacity to manufacture diesel engines for the Russian market, for locally produced Sprinter Classic. In addition to engines for the local market, the Yaroslavl plant will also produce spare parts. Mercedes-Benz Russia and his partner needed a service partner in order to ensure the operation of these lines in a maintenance partnership arrangement. The challenges included coordinating the entire maintenance management operation, in particular inspections, corrective and predictive maintenance activities, and the optimizing spare parts management. Siemens developed a customized maintenance solution that includes all electronic and mechanical maintenance activities (Integral Plant Maintenance).