Technology Category
- Analytics & Modeling - Digital Twin / Simulation
- Functional Applications - Manufacturing Execution Systems (MES)
Applicable Industries
- Life Sciences
- Plastics
Use Cases
- Manufacturing Process Simulation
- Virtual Reality
Services
- System Integration
About The Customer
The customer in this case study is not explicitly mentioned. However, it can be inferred that the customers are companies involved in the design and manufacturing of composite materials. These could include companies in the aerospace, automotive, and other industries that require complex composite materials for their products. These companies need to accurately represent and model the behavior of composite materials, generate realistic finite element models of wound parts, perform global simulations that include refined areas at a lower scale, and simulate the lay-up manufacturing process of complex composite parts to predict the orientation of fibers and fiber volume fraction.
The Challenge
The case study presents several challenges faced by companies in the field of composite material design and manufacturing. The first challenge is to accurately represent the behavior of composite material and choose the best option from many possibilities. The second challenge is to generate a realistic finite element model of a wound part. The third challenge is to perform a global simulation that includes refined areas at a lower scale. The fourth challenge is to simulate the lay-up manufacturing process of a complex composite part to predict the orientation of its fibers and its fiber volume fraction. The final challenge is to simulate the lay-up manufacturing process of an aeronautic radome, predict the orientation of its fibers, and consider these orientations in predicting the electromagnetic performance.
The Solution
The solutions to these challenges are provided by the KTex Family of software by CEDREM. For the first challenge, KTex Pattern is used to represent the composite material at the scale of the yarns, and KTex WovenProperty is used to calculate the homogenized macroscale mechanical properties of any given weave. For the second challenge, KTex Winding is used to visualize the paths followed by the yarns during the winding process and simulate the winding process considering the mechanical properties of the yarns. For the third challenge, KTex Pattern and KTex LayUp are used for precise simulation of the composite material at the scale of the yarns, refinement of the composite material in the chosen areas, and integration of the updated mechanical properties from the lower scale model to the upper scale global simulation. For the fourth and fifth challenges, KTex Pattern is used to build a mesoscopic FE model of several fabrics inside HyperMesh, and KTex Layup is used to set up a manufacturing process simulation inside HyperMesh and run with RADIOSS solver.
Operational Impact
Case Study missing?
Start adding your own!
Register with your work email and create a new case study profile for your business.
Related Case Studies.

Case Study
Plastic Spoons Case study: Injection Moulding
In order to meet customer expectations by supplying a wide variety of packaging units, from 36 to 1000 spoons per package, a new production and packaging line needed to be built. DeSter wanted to achieve higher production capacity, lower cycle time and a high degree of operator friendliness with this new production line.
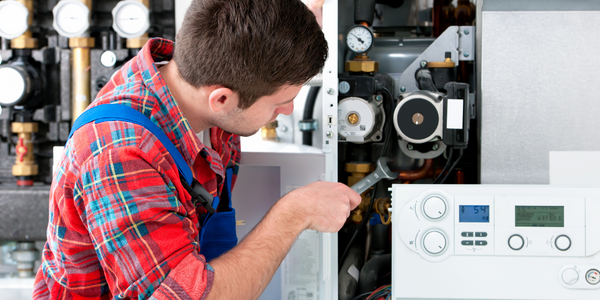
Case Study
Boiler Control System for Plastic Manufacturing Applications
Factory automation applications must be equipped to handle and monitor the myriads of information from attached devices. For plastic manufacturing applications, the boiler control system plays a critical role by gathering and regulating information to ensure production is accurate and smooth. In this particular case, the customer combines eight subsystems that include power meters, water meters, alarm output, displays, and I/O status to be controlled by several intelligent controllers with Modbus RTU interface. The Modbus TCP protocol is used for this application due to the distance. System Requirements: • Modbus serial to Modbus TCP translation • Multiple slaves/masters support • Automatic Modbus TCP response time detection
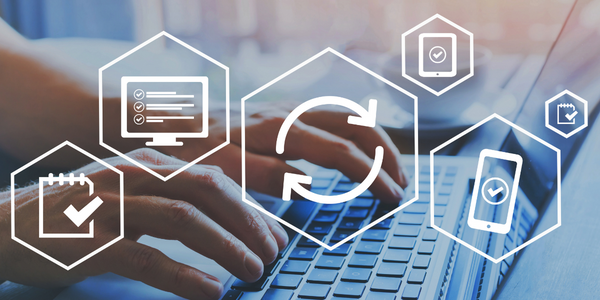
Case Study
Ascend Performance Materials Case Study
Ascend operations must access multiple software systems to manage day-to-day operations in an effective and secure manner. These systems generate large sets of data which contain critical information pertaining to management systems, planning and cost information in business systems and energy consumption. As a result, Ascend management was challenged with creating relevant reports reflecting performance measures in overall context of their operational process. The company’s previous process entailed collecting and analyzing data manually which was not effective, since the information collected was generated after the fact, and was too complex for collaborative use across the organization.
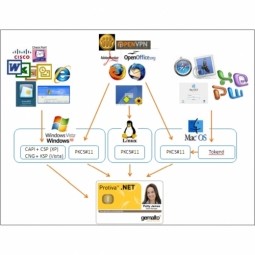
Case Study
Corporate Identity Solution Adds Convenience to Beckman Coulter
Beckman Coulter wanted to implement a single factor solution for physical and remote logical access to corporate network. Bechman Coulter's users were carrying smart card badges for doors, but also needed a one-time password token to access to our corporate network when they were not in the office. They wanted to simplify the process.
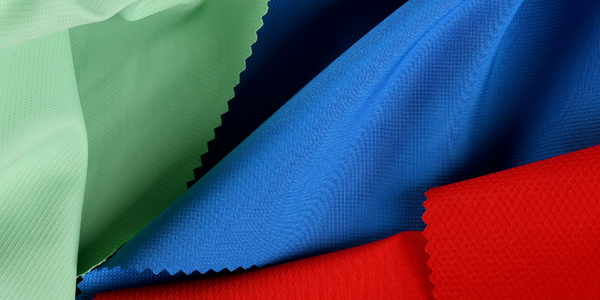
Case Study
Remake Enterprise-to-production System
The client was running a legacy material flow tracking system and wanted to replace the system with a more effective one as the system was increasingly expensive to maintain and support and also was not extendable. The client's IT landscape was filled with modern applications and it was difficult to interface the material flow tracking system with modern applications.
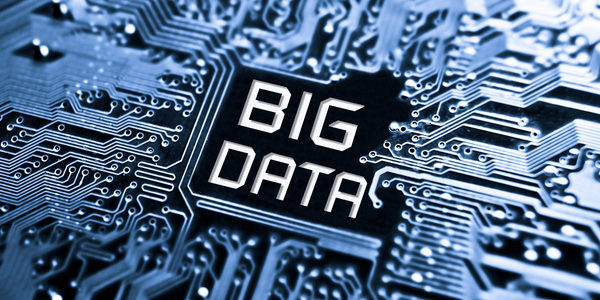
Case Study
Embracing Business Success in Real Time
· Increase control over growing Big Data to improve business decisions · Manage data for 28,000 biotechnology stockkeeping units in the fields of microbiology, molecular biology, animal cell cultures, plant tissue cultures, and lab ware for laboratory chemicals · Accelerate report generation and analysis with real-time data