Company Size
1,000+
Region
- America
Country
- Mexico
Product
- JDA Demand Manager
- JDA Supply Chain Planner
Tech Stack
- Supply Chain Management Software
- Demand Forecasting Software
Implementation Scale
- Enterprise-wide Deployment
Impact Metrics
- Cost Savings
- Customer Satisfaction
- Productivity Improvements
Technology Category
- Functional Applications - Inventory Management Systems
- Functional Applications - Manufacturing Execution Systems (MES)
Applicable Industries
- Apparel
Applicable Functions
- Discrete Manufacturing
- Procurement
Use Cases
- Inventory Management
- Predictive Maintenance
Services
- Cloud Planning, Design & Implementation Services
- System Integration
About The Customer
Grupo Flexi is a leading footwear manufacturer in Mexico, with over 75 years of experience in designing, manufacturing, and selling quality footwear. The company produces more than 13 million pairs of shoes annually, making it the largest leather footwear manufacturer in Mexico. Each pair of shoes can have up to 30 different components and several raw materials, making the manufacturing process labor-intensive. Flexi sources materials from several countries and distributes them to its manufacturing operations, which include 30 company-owned and subcontracted factories. The company has expanded its product assortment, introducing new products for different market segments, which has increased the complexity of managing more raw materials and stock-keeping units (SKUs), as well as more construction of shoes.
The Challenge
Grupo Flexi, a leading footwear manufacturer in Mexico, faced increasing complexity in its supply chain as it expanded its product assortment. The company produces over 13 million pairs of shoes annually, with each pair requiring up to 30 different components and several raw materials. One of the most critical materials, leather, has variable lead times ranging from three weeks to three months, depending on the supplier. Flexi sources materials from several countries and distributes them to its manufacturing operations, which include 30 company-owned and subcontracted factories. Eight years ago, Flexi decided to expand its product assortment, introducing new products for different market segments. This initiative increased the complexity of managing more raw materials and stock-keeping units (SKUs), as well as more construction of shoes, which required different specializations and capacities in different factories.
The Solution
To manage the increased complexity, Flexi engaged JDA Consulting Services for a six-week consulting engagement. The consultants introduced Flexi to JDA’s supply chain planning best practices, identified areas of opportunity, and developed a roadmap to implement these recommendations. Flexi selected JDA Supply Chain Planner and JDA Demand Manager to improve its forecasting abilities, optimize its supply chain, and plan for the production, capacities and purchase of materials. The company worked with JDA to implement process and organizational recommendations and implement JDA’s solutions to improve the demand management and master planning process. JDA solutions have enabled Flexi to plan for a much higher variety of products. With most of the calculations and optimizations done by the software, Flexi can focus on strategic decisions.
Operational Impact
Quantitative Benefit
Case Study missing?
Start adding your own!
Register with your work email and create a new case study profile for your business.
Related Case Studies.
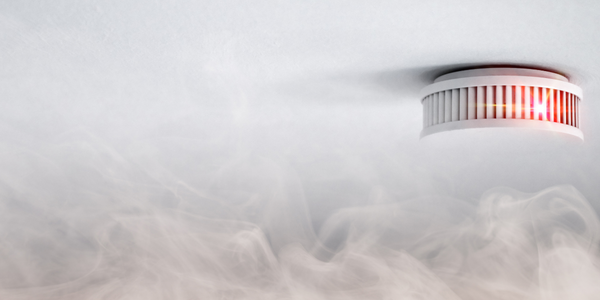
Case Study
Fire Alarm System and Remote Monitoring Sytem
Fire alarm systems are essential in providing an early warning in the event of fire. They help to save lives and protect property whilst also fulfilling the needs of insurance companies and government departments.Fire alarm systems typically consist of several inter-linked components, such as smoke detectors, heat detector, carbon monoxide, manual call points, sounders, alarm and buzzer. The fire alarm system should give immediate information in order to prevent the fire spread and protect live and property.To get maximum protection a shoe manufacturer in Indonesia opted for a new fire alarm system to monitor 13 production sites spread over 160 hectars. Although the company had an existing fire alarm system, it could not be monitored remotely.It was essential that the new system would be able to be monitored from a central control room. It needed to be able to connect to the existing smoke detector and manual call point. Information should be easily collected and passed on to the Supervisory Control and Data Acquisition (SCADA) system. Furthermore, the system should have several features such as alarm management, auto reporting, being connected to many client computers without additional cost, and run 24/7 without fails. The company also needed a system which could be implemented without changing the architecture of the existing fire alarm system.
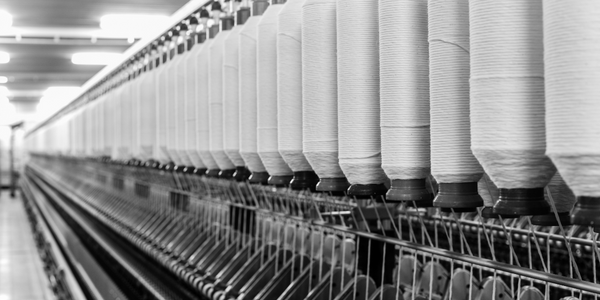
Case Study
IoT Applications and Upgrades in Textile Plant
At any given time, the textile company’s manufacturing facility has up to 2,000 textile carts in use. These carts are pushed from room to room, carrying materials or semi-finished products. Previously, a paper with a hand-written description was attached to each cart. This traditional method of processing made product tracking extremely difficult. Additionally, making sure that every cart of materials or semi-finished products went to its correct processing work station was also a problem. Therefore, the company desired an intelligent solution for tracking assets at their factories. They also wanted a solution that would help them collect process data so they could improve their manufacturing efficiency.
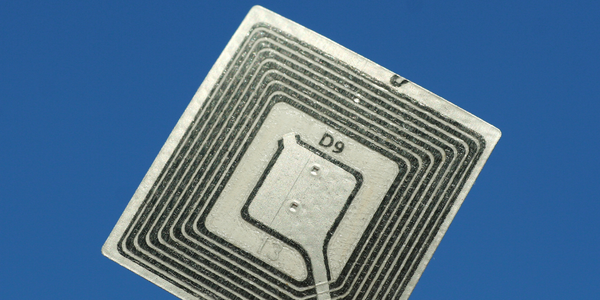
Case Study
Retailer Uses RFID Scanner to Improve Efficiency
Patrizia Pepe wished to improve the logistics of their warehouse: accepting incoming goods from their production sites, movement of items throughout
the warehouse, and packaging of goods for distribution to the retail locations. They initially tried to use barcodes for this function. Because barcodes must be individually scanned within a line-of-sight, the acceptance of goods coming into the warehouse was too time consuming. Working with the University of Florence, Patrizia Pepe instituted a five-month pilot project beginning in August of 2009 to test the validity of an RFID solution. The pilot involved tagging of about 60,000 items for the second seasonal collection, and convinced the company to move forward with tagging all items.
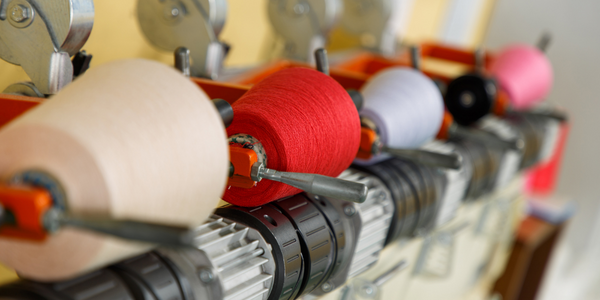
Case Study
Monitoring and Controlling Automatic Mixing and Dispensing Machines
As technology advances, textile manufacturing has been transformed from a labor-intensive to a partially or fully automated industry. Automation is significant in all segments of textile production - from spinning to printing, and textile machinery manufacturers are constantly searching for new technologies and automation processes will increase the productivity of their machines. The color paste mixing and dispensing machine is an essential part of the printing and dyeing process. With the advantage of automatically computerized controls and database management, the system can significantly improve its dispensing precision, working efficiency and production quality as well as reducing material consumption.