New aluminum, electric utility transport is green in more ways than one: half the weight with 60 percent fewer welds
Company Size
11-200
Region
- America
Country
- Canada
Product
- Simcenter
- NX Nastran
- Simcenter 3D
- SolidWorks
Tech Stack
- Finite Element Analysis (FEA)
- Computer-Aided Design (CAD)
- Simcenter 3D Thermal
- Simcenter synchronous technology
Implementation Scale
- Departmental Deployment
Impact Metrics
- Cost Savings
- Environmental Impact Reduction
- Innovation Output
- Productivity Improvements
Technology Category
- Analytics & Modeling - Predictive Analytics
- Functional Applications - Product Lifecycle Management Systems (PLM)
- Functional Applications - Remote Monitoring & Control Systems
Applicable Industries
- Specialty Vehicles
- Transportation
Applicable Functions
- Product Research & Development
- Quality Assurance
Use Cases
- Fleet Management
- Predictive Maintenance
- Remote Asset Management
- Vehicle Performance Monitoring
Services
- Software Design & Engineering Services
- System Integration
- Training
About The Customer
Services Précicad Inc. (Précicad) is a multidisciplinary team of engineers, industrial designers, technicians, and drafters providing consulting services for product development, with a special emphasis on industrial design, mechanical design, and finite element analysis (FEA). Their clients include notable companies such as Cirque de Soleil, Garant, RioTinto Alcan, SigmaDek, Volvo Buses, and GE Hydro. Another significant client is Aluminerie Alouette, a Canadian aluminum smelter. Aluminerie Alouette approached Précicad with a unique request to design electric utility vehicles made of aluminum to replace their existing steel vehicles. This change was driven by the need to operate in areas with strong static magnetic fields and to showcase Aluminerie Alouette's aluminum products while emphasizing environmental sustainability.
The Challenge
Précicad faced the challenge of designing and manufacturing a small fleet of electrically powered utility vehicles with bodies and frames made of aluminum instead of steel. Aluminerie Alouette requested a load-carrying capacity of 1,000 pounds. The smelter was at the point where it needed to replace its existing vehicles, so Précicad agreed to have a working model ready within six months to a year. The vehicles needed to operate in areas with strong static magnetic fields, which regular internal combustion engines couldn't handle.
The Solution
Précicad utilized a combination of SolidWorks for modeling and Simcenter software from Siemens PLM Software for finite element analysis (FEA) to design the aluminum utility vehicles. The process involved importing the SolidWorks assembly model into Simcenter 3D, simplifying the geometry, creating the finite element mesh, applying loads, and indicating boundary conditions. The engineers followed an iterative process, using analysis results to optimize the design. Simcenter's fast design-analysis iterations allowed for multiple iterations in a single day, significantly speeding up the development process. Additionally, Simcenter 3D Thermal analysis software was used to research ways to make the vehicle battery operate more effectively in cold weather.
Operational Impact
Quantitative Benefit
Case Study missing?
Start adding your own!
Register with your work email and create a new case study profile for your business.
Related Case Studies.
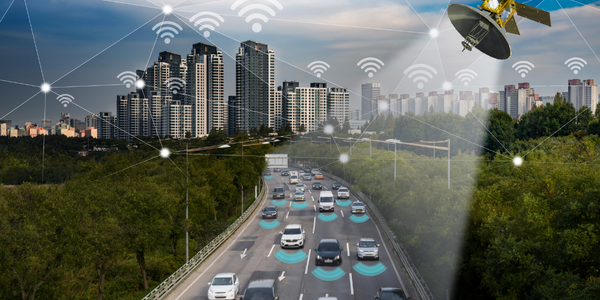
Case Study
Transformation for IoT Business Model in Connected Industrial Vehicles
CNH Industrial wanted to put IoT-enabled viechles onto the market. Whether monitoring a single machine or integrating an entire fleet, operators are able to track the status, speed, and movement of machines and their performance and also receive alerts on issues that may require service by a qualified technician to improve uptime and overall effectiveness of the vehicle.
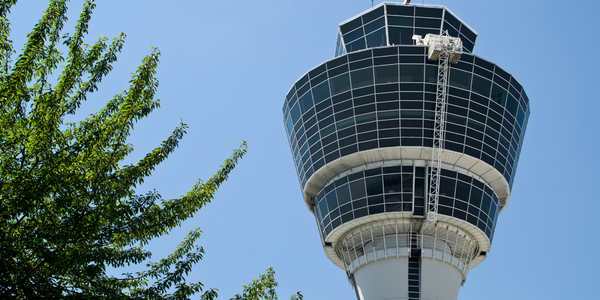
Case Study
Airport SCADA Systems Improve Service Levels
Modern airports are one of the busiest environments on Earth and rely on process automation equipment to ensure service operators achieve their KPIs. Increasingly airport SCADA systems are being used to control all aspects of the operation and associated facilities. This is because unplanned system downtime can cost dearly, both in terms of reduced revenues and the associated loss of customer satisfaction due to inevitable travel inconvenience and disruption.
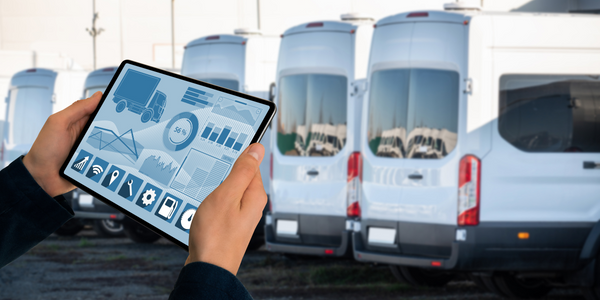
Case Study
IoT-based Fleet Intelligence Innovation
Speed to market is precious for DRVR, a rapidly growing start-up company. With a business model dependent on reliable mobile data, managers were spending their lives trying to negotiate data roaming deals with mobile network operators in different countries. And, even then, service quality was a constant concern.
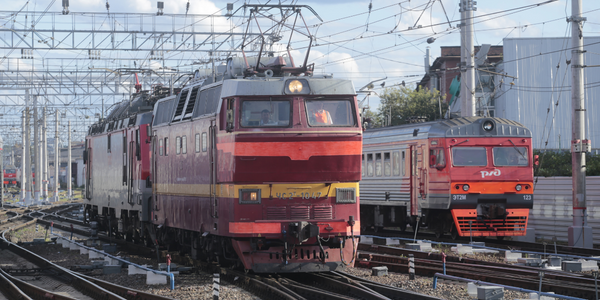
Case Study
Digitize Railway with Deutsche Bahn
To reduce maintenance costs and delay-causing failures for Deutsche Bahn. They need manual measurements by a position measurement system based on custom-made MEMS sensor clusters, which allow autonomous and continuous monitoring with wireless data transmission and long battery. They were looking for data pre-processing solution in the sensor and machine learning algorithms in the cloud so as to detect critical wear.
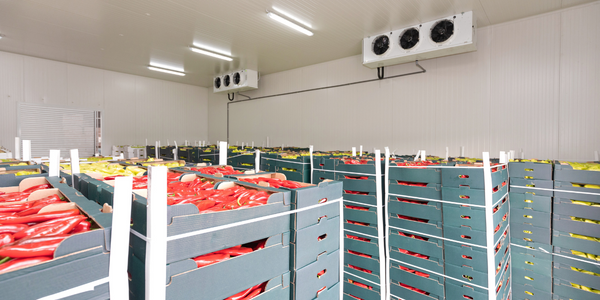
Case Study
Cold Chain Transportation and Refrigerated Fleet Management System
1) Create a digital connected transportation solution to retrofit cold chain trailers with real-time tracking and controls. 2) Prevent multi-million dollar losses due to theft or spoilage. 3) Deliver a digital chain-of-custody solution for door to door load monitoring and security. 4) Provide a trusted multi-fleet solution in a single application with granular data and access controls.