Customer Company Size
Large Corporate
Region
- America
Country
- Mexico
Product
- VectorFurniture
Tech Stack
- Lean Manufacturing Principles
- DILO (Day In the Life Of) Studies
- Value Stream Mapping
- Overall Equipment Efficiency Analysis
Implementation Scale
- Enterprise-wide Deployment
Impact Metrics
- Cost Savings
- Productivity Improvements
- Customer Satisfaction
Technology Category
- Functional Applications - Manufacturing Execution Systems (MES)
- Functional Applications - Product Lifecycle Management Systems (PLM)
- Functional Applications - Remote Monitoring & Control Systems
Applicable Functions
- Process Manufacturing
- Quality Assurance
Use Cases
- Manufacturing System Automation
- Predictive Maintenance
- Process Control & Optimization
Services
- System Integration
- Training
About The Customer
Muebles Liz is a leading Mexican upholstered furniture manufacturer known for its high-quality products and competitive pricing. The company has been in the industry for several years and has built a reputation for delivering top-notch furniture to its customers. Muebles Liz operates on a 'just-in-time' production model, which requires precise and efficient manufacturing processes to meet customer demands promptly. The company employs a significant workforce and has been striving to improve its production capabilities to stay competitive in the market. With a focus on quality and customer satisfaction, Muebles Liz has been continuously looking for ways to optimize its manufacturing processes and reduce operational costs.
The Challenge
With an automated cutting solution in place, which was already more than 10 years old, Muebles Liz’s ‘just-in-time’ production was struggling to satisfy customer orders. In addition, their existing cutter was being used for fabric only, leaving nonwoven and other materials to be cut by hand. The main growth objectives were to improve product specifications both in terms of quality and price, and to be more competitive in the market. The main challenge was to meet demand, for which they were logging a lot of overtime hours from manual cutting labor. To overcome this challenge, the Muebles Liz team was looking to acquire a new automated cutting system. Working with Lectra experts it became clear that a new system was only one part of an overall solution and that Lectra’s expertise and know-how could bring even greater benefits. An in-depth analysis of the company’s current production processes formed the basis for a tailored action plan which enabled Muebles Liz to reduce operational costs by improving productivity through more efficient production processes.
The Solution
Lectra’s consultant analyzed all Muebles Liz's processes, including interviewing production staff to identify activities that added value and those which did not. Lectra suggested areas for improvement not only for the cutting department but for the entire manufacturing process. By following Lectra’s recommendations for optimizing their processes, Muebles Liz was able to eliminate non-value-added activities, increase production capacity, and achieve better product quality. These improvements were made possible by applying lean manufacturing principles and using assessment methods such as DILO (Day In the Life Of) studies, Value Stream Mapping, and analysis of overall equipment efficiency. Key Performance Indicators such as process time and cutting capacity were agreed to with Muebles Liz at the outset and monitored continuously throughout the project. The combination of hardware, software, and Lectra’s specialists helped Muebles Liz greatly in streamlining their processes.
Operational Impact
Quantitative Benefit
Case Study missing?
Start adding your own!
Register with your work email and create a new case study profile for your business.
Related Case Studies.

Case Study
Remote Monitoring & Predictive Maintenance App for a Solar Energy System
The maintenance & tracking of various modules was an overhead for the customer due to the huge labor costs involved. Being an advanced solar solutions provider, they wanted to ensure early detection of issues and provide the best-in-class customer experience. Hence they wanted to automate the whole process.
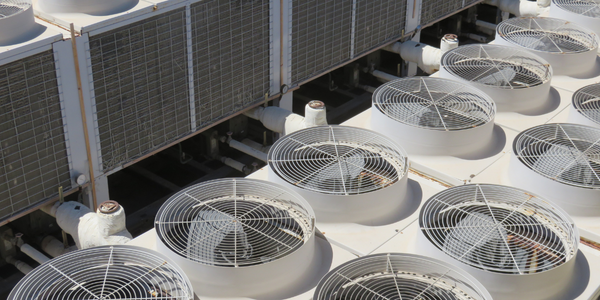
Case Study
Predictive Maintenance for Industrial Chillers
For global leaders in the industrial chiller manufacturing, reliability of the entire production process is of the utmost importance. Chillers are refrigeration systems that produce ice water to provide cooling for a process or industrial application. One of those leaders sought a way to respond to asset performance issues, even before they occur. The intelligence to guarantee maximum reliability of cooling devices is embedded (pre-alarming). A pre-alarming phase means that the cooling device still works, but symptoms may appear, telling manufacturers that a failure is likely to occur in the near future. Chillers who are not internet connected at that moment, provide little insight in this pre-alarming phase.

Case Study
System 800xA at Indian Cement Plants
Chettinad Cement recognized that further efficiencies could be achieved in its cement manufacturing process. It looked to investing in comprehensive operational and control technologies to manage and derive productivity and energy efficiency gains from the assets on Line 2, their second plant in India.

Case Study
Plastic Spoons Case study: Injection Moulding
In order to meet customer expectations by supplying a wide variety of packaging units, from 36 to 1000 spoons per package, a new production and packaging line needed to be built. DeSter wanted to achieve higher production capacity, lower cycle time and a high degree of operator friendliness with this new production line.
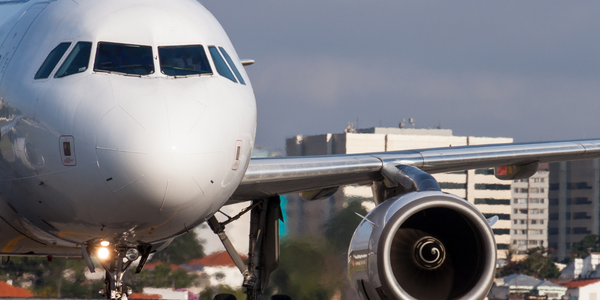
Case Study
Airbus Soars with Wearable Technology
Building an Airbus aircraft involves complex manufacturing processes consisting of thousands of moving parts. Speed and accuracy are critical to business and competitive advantage. Improvements in both would have high impact on Airbus’ bottom line. Airbus wanted to help operators reduce the complexity of assembling cabin seats and decrease the time required to complete this task.