Moving to a Paperless Way of Working at Vandemoortele Zeewolde (NL)
Company Size
1,000+
Region
- Europe
Country
- Netherlands
Product
- Proceedix digital work instruction and inspection workflow execution platform
Tech Stack
- Not mentioned
Implementation Scale
- Enterprise-wide Deployment
Impact Metrics
- Productivity Improvements
- Waste Reduction
Technology Category
- Functional Applications - Remote Monitoring & Control Systems
Applicable Industries
- Food & Beverage
Applicable Functions
- Discrete Manufacturing
- Quality Assurance
Use Cases
- Condition Monitoring
- Manufacturing System Automation
Services
- System Integration
About The Customer
Vandemoortele is a leading European food group that manufactures and sells high-quality food products. Vandemoortele focuses on two activities: Bakery Products and Margarines, Culinary Oils & Fats. The Group is present in 12 European countries and the United States with own sales organisations and/or production sites. The Vandemoortele Zeewolde factory is one of the production sites of the group.
The Challenge
Vandemoortele Zeewolde factory aimed to start an autonomous maintenance project for its production line operators. The regular way of working used to be on paper. For example, the proposal for improvement procedure by the production team was filled on a paper form. These proposals were reviewed regularly, but there was a need for more insight into the status of the review and better communication about the actions. Paper instruction and inspections were used in production, maintenance, Health Safety and Environment, facility and quality assurance.
The Solution
Vandemoortele Zeewolde implemented the Proceedix digital work instruction and inspection workflow execution platform to eliminate paper throughout the factory operations. Instructions are enriched with movies to show operators how to inspect the different machines, allowing them to detect any faults in an early stage and to prevent stops of the production line. The agreed standards of 5S and cleanliness of every machine on the production floor are captured in pictures and put in a procedure workflow in Proceedix. During shift transfers this procedure is executed and any deviations with the standard is photographed and registered for follow-up discussion and action.
Operational Impact
Case Study missing?
Start adding your own!
Register with your work email and create a new case study profile for your business.
Related Case Studies.

Case Study
The Kellogg Company
Kellogg keeps a close eye on its trade spend, analyzing large volumes of data and running complex simulations to predict which promotional activities will be the most effective. Kellogg needed to decrease the trade spend but its traditional relational database on premises could not keep up with the pace of demand.

Case Study
HEINEKEN Uses the Cloud to Reach 10.5 Million Consumers
For 2012 campaign, the Bond promotion, it planned to launch the campaign at the same time everywhere on the planet. That created unprecedented challenges for HEINEKEN—nowhere more so than in its technology operation. The primary digital content for the campaign was a 100-megabyte movie that had to play flawlessly for millions of viewers worldwide. After all, Bond never fails. No one was going to tolerate a technology failure that might bruise his brand.Previously, HEINEKEN had supported digital media at its outsourced datacenter. But that datacenter lacked the computing resources HEINEKEN needed, and building them—especially to support peak traffic that would total millions of simultaneous hits—would have been both time-consuming and expensive. Nor would it have provided the geographic reach that HEINEKEN needed to minimize latency worldwide.

Case Study
Energy Management System at Sugar Industry
The company wanted to use the information from the system to claim under the renewable energy certificate scheme. The benefit to the company under the renewable energy certificates is Rs 75 million a year. To enable the above, an end-to-end solution for load monitoring, consumption monitoring, online data monitoring, automatic meter data acquisition which can be exported to SAP and other applications is required.

Case Study
Coca Cola Swaziland Conco Case Study
Coco Cola Swaziland, South Africa would like to find a solution that would enable the following results: - Reduce energy consumption by 20% in one year. - Formulate a series of strategic initiatives that would enlist the commitment of corporate management and create employee awareness while helping meet departmental targets and investing in tools that assist with energy management. - Formulate a series of tactical initiatives that would optimize energy usage on the shop floor. These would include charging forklifts and running cold rooms only during off-peak periods, running the dust extractors only during working hours and basing lights and air-conditioning on someone’s presence. - Increase visibility into the factory and other processes. - Enable limited, non-intrusive control functions for certain processes.

Case Study
Temperature Monitoring for Restaurant Food Storage
When it came to implementing a solution, Mr. Nesbitt had an idea of what functionality that he wanted. Although not mandated by Health Canada, Mr. Nesbitt wanted to ensure quality control issues met the highest possible standards as part of his commitment to top-of-class food services. This wish list included an easy-to use temperature-monitoring system that could provide a visible display of the temperatures of all of his refrigerators and freezers, including historical information so that he could review the performance of his equipment. It also had to provide alert notification (but email alerts and SMS text message alerts) to alert key staff in the event that a cooling system was exceeding pre-set warning limits.
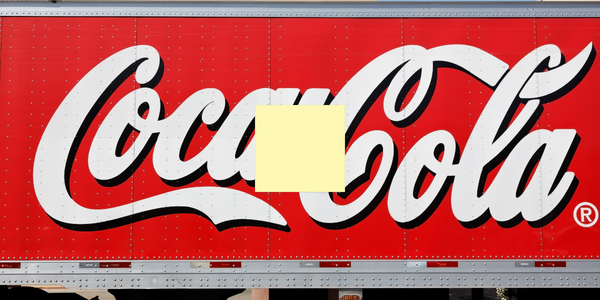
Case Study
Coca-Cola Refreshments, U.S.
Coca-Cola Refreshments owns and manages Coca-Cola branded refrigerators in retail establishments. Legacy systems were used to locate equipment information by logging onto multiple servers which took up to 8 hours to update information on 30-40 units. The company had no overall visibility into equipment status or maintenance history.