Customer Company Size
Large Corporate
Region
- Europe
Country
- Germany
Product
- COMSOL Multiphysics
- MEMS Generator
- TPMS
Tech Stack
- Fluid-Structure Interaction Simulation
- Piezoelectric Ceramic Material
- Silicon Carrier Layer
Implementation Scale
- Pilot projects
Impact Metrics
- Cost Savings
- Environmental Impact Reduction
- Innovation Output
Technology Category
- Analytics & Modeling - Predictive Analytics
- Analytics & Modeling - Digital Twin / Simulation
- Analytics & Modeling - Real Time Analytics
Applicable Industries
- Automotive
- Electronics
Applicable Functions
- Product Research & Development
- Quality Assurance
Use Cases
- Predictive Maintenance
- Machine Condition Monitoring
- Remote Asset Management
Services
- Software Design & Engineering Services
- System Integration
About The Customer
Siemens Corporate Technology, based in Munich, Germany, is a research and development division of Siemens AG. The team at Siemens Corporate Technology is dedicated to exploring and developing platform technologies for future applications rather than focusing on specific products. Their research spans a wide range of fields, including energy harvesting, microelectromechanical systems (MEMS), and fluid-structure interaction simulations. Siemens Corporate Technology collaborates with various partners, such as Continental AG, to demonstrate the commercial potential of their research. The team is composed of senior engineers and researchers who are committed to advancing technology and innovation.
The Challenge
The desire to eliminate batteries and power lines is motivating a wide range of research. In the quest for systems that are energy autonomous, the concept of energy harvesting is attracting a great deal of attention. For researchers at Siemens Corporate Technology in Munich, exploring the potential of an energy-harvesting microelectromechanical system (MEMS) generator holds strong appeal. The researchers chose to design a microgenerator for an innovative tire pressure monitoring system (TPMS) driven by motion. Yet locating the device within the tire requires that the assembly be extremely robust and able to withstand gravitational accelerations up to 2500 g. Moreover, to avoid tire imbalance it would have to be very light, and in terms of operational life it would need to match that of a tire—a minimum of eight years.
The Solution
The Siemens team designed a piezoelectric microgenerator to be mounted inside a tire, capable of harvesting energy from the compression created each time the tire touched the ground. The cantilever was designed with a thin film of self-polarized piezoelectric ceramic material and a silicon carrier layer for mechanical stability. The team settled on a triangular design for the spring-loaded piezoelectric cantilever to enable uniform stress distribution. They conducted fluid-structure interaction (FSI) analysis to optimize the cantilever's design, focusing on minimizing damping and ensuring mechanical oscillation. The use of COMSOL Multiphysics simulation software was critical in numerically describing the behavior of the structure and optimizing system components and integration.
Operational Impact
Quantitative Benefit
Case Study missing?
Start adding your own!
Register with your work email and create a new case study profile for your business.
Related Case Studies.

Case Study
Remote Temperature Monitoring of Perishable Goods Saves Money
RMONI was facing temperature monitoring challenges in a cold chain business. A cold chain must be established and maintained to ensure goods have been properly refrigerated during every step of the process, making temperature monitoring a critical business function. Manual registration practice can be very costly, labor intensive and prone to mistakes.
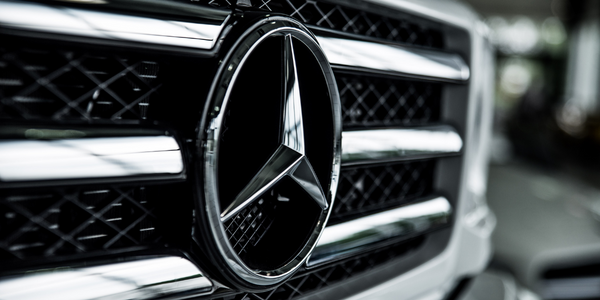
Case Study
Integral Plant Maintenance
Mercedes-Benz and his partner GAZ chose Siemens to be its maintenance partner at a new engine plant in Yaroslavl, Russia. The new plant offers a capacity to manufacture diesel engines for the Russian market, for locally produced Sprinter Classic. In addition to engines for the local market, the Yaroslavl plant will also produce spare parts. Mercedes-Benz Russia and his partner needed a service partner in order to ensure the operation of these lines in a maintenance partnership arrangement. The challenges included coordinating the entire maintenance management operation, in particular inspections, corrective and predictive maintenance activities, and the optimizing spare parts management. Siemens developed a customized maintenance solution that includes all electronic and mechanical maintenance activities (Integral Plant Maintenance).