MES to Standardize Wafer Epitaxial Operations
Customer Company Size
Mid-size Company
Region
- Asia
Country
- China
Product
- Critical Manufacturing MES
Tech Stack
- Manufacturing Execution System
Implementation Scale
- Enterprise-wide Deployment
Impact Metrics
- Productivity Improvements
- Customer Satisfaction
Technology Category
- Functional Applications - Manufacturing Execution Systems (MES)
Applicable Industries
- Electronics
Applicable Functions
- Discrete Manufacturing
Use Cases
- Manufacturing System Automation
Services
- System Integration
About The Customer
Nanjing Guosheng Electronic Co. Ltd. (GS-EPI) is a professional silicon epitaxial wafer (Epi) OEM services provider. The company manufactures more than 200,000 6” EPI wafers per month on three types of equipment: ASML 2000 lithography, and LPE2061 and LPE 3061 reactors. They have a total of 60 production units, and volume is growing. The company's major semiconductor customers rely on GS-EPI’s output as a foundation for their products. The epi layer must have uniform thickness and resistance to perform well in the semiconductor fab. To meet the increasing number of orders and to comply with customer demands, GS-EPI decided to implement a manufacturing execution system (MES).
The Challenge
GS-EPI, a provider of professional silicon epitaxial wafer (Epi) OEM services, was facing a growing challenge. The company manufactures more than 200,000 6” EPI wafers per month on three types of equipment and the volume was growing. Historically, GS-EPI collected production data, recorded it on paper and put it into Excel spreadsheets. Querying production data was very difficult and in some cases, it was impossible to find the correct set of data from the past. To win customers, GS-EPI has to explain how they manage the production process, how they control quality and how they achieve wafer traceability. Their critical customers demanded that they implement an MES system. At the same time, managers knew that they needed a tool to help manage production efficiently to meet the increasing number of orders they were getting.
The Solution
GS-EPI decided to implement a manufacturing execution system (MES) to eliminate paper and automate data collection. They modeled production in the MES, which includes data from across the full production process, and the ability to collect equipment data and control production end-to-end. The implementation expanded in sequence, starting with paperless work, workshop visualization, single production data source, WIP wafer traceability, preventive maintenance, production process configuration, shipping management, and reports. They selected an internationally known MES software provider with experience in GS-EPI’s segment or at least in semiconductor, successful references in China, and a local team in China. The implementation was led by the VP of Production and involved a team from IT and end user groups, with the help of a consultant for MES selection and production optimization.
Operational Impact
Quantitative Benefit
Case Study missing?
Start adding your own!
Register with your work email and create a new case study profile for your business.
Related Case Studies.

Case Study
Remote Temperature Monitoring of Perishable Goods Saves Money
RMONI was facing temperature monitoring challenges in a cold chain business. A cold chain must be established and maintained to ensure goods have been properly refrigerated during every step of the process, making temperature monitoring a critical business function. Manual registration practice can be very costly, labor intensive and prone to mistakes.
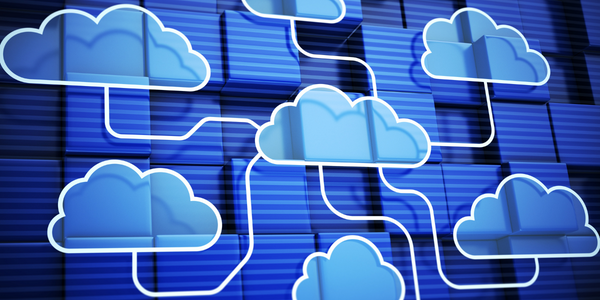
Case Study
Cloud Solution for Energy Management Platform-Schneider Electric
Schneider Electric required a cloud solution for its energy management platform to manage high computational operations, which were essential for catering to client requirements. As the business involves storage and analysis of huge amounts of data, the company also needed a convenient and scalable storage solution to facilitate operations efficiently.
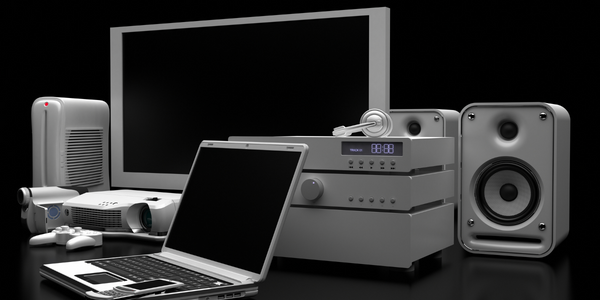
Case Study
Leveraging the IoT to Gain a Competitive Edge in International Competition
Many large manufacturers in and outside Japan are competing for larger market share in the same space, expecting a growing demand for projectors in the areas of entertainment, which requires glamor and strong visual performance as well as digital signage that can attract people’s attention. “It is becoming more and more difficult to differentiate ourselves with stand-alone hardware products,” says Kazuyuki Kitagawa, Director of Service & Support at Panasonic AVC Networks. “In order for Panasonic to grow market share and overall business, it is essential for us to develop solutions that deliver significant added value.” Panasonic believes projection failure and quality deterioration should never happen. This is what and has driven them to make their projectors IoT-enabled. More specifically, Panasonic has developed a system that collects data from projectors, visualizes detailed operational statuses, and predicts issues and address them before failure occurs. Their projectors are embedded with a variety of sensors that measure power supply, voltage, video input/ output signals, intake/exhaust air temperatures, cooling fan operations, and light bulb operating time. These sensors have been used to make the projector more intelligent, automatically suspending operation when the temperature rises excessively, and automatically switching light bulbs. Although this was a great first step, Panasonic projectors were still not equipped with any capability to send the data over a network.