Customer Company Size
Large Corporate
Region
- America
Country
- United States
Product
- Samsara Manufacturing Analytics
- Samsara HMI Interface
Tech Stack
- Real-Time Analytics
- Cellular Connectivity
- Automatic Downtime Logging
Implementation Scale
- Enterprise-wide Deployment
Impact Metrics
- Productivity Improvements
- Cost Savings
- Customer Satisfaction
Technology Category
- Analytics & Modeling - Real Time Analytics
- Functional Applications - Manufacturing Execution Systems (MES)
- Networks & Connectivity - Cellular
Applicable Industries
- Construction & Infrastructure
Applicable Functions
- Process Manufacturing
- Quality Assurance
Use Cases
- Predictive Maintenance
- Machine Condition Monitoring
- Factory Operations Visibility & Intelligence
Services
- System Integration
- Software Design & Engineering Services
About The Customer
Formed in 2016 with the merging of Boral Bricks and Forterra Brick, Meridian Brick is a leading manufacturer of sustainable building products and construction materials in North America. Meridian Brick builds on the two companies’ histories of innovation while expanding its catalog to over 1000 products targeted towards residential and commercial use cases. With a supply chain that spans from raw material extraction to finished brick, the company understands the importance of accurate, real-time data in driving efficiency in its operations. As the largest manufacturer of brick and masonry products in North America, Meridian Brick partners with Samsara to improve production efficiency with automatic downtime tracking and OEE analytics.
The Challenge
When a single hour of downtime at Meridian Brick costs thousands of dollars in lost revenue, having the most accurate downtime data is critical for the company’s bottom line. David Peters, Meridian Brick’s Director of Technical Services, is on a mission to improve operational efficiency, and knows that accurate production data is the first step in knowing what to improve. The most challenging part of their manual data logging process was never having accurate times. All of the 30-second downtimes that went unlogged ended up becoming death by a thousand papercuts. With Samsara, the impact of real-time analytics on uptime, throughput, and scrap rate that can be accessed from any device has been immediate. The data is way more accurate than what was possible with a manual system. They noticed, for example, that a significant amount of downtime was occurring at a particular plant due to raw material loading, something which wasn’t apparent in their manual data before. Accurate downtime logging has empowered David and the plant managers to make more informed decisions around processes, resourcing, and capital expenditures in order to improve production performance.
The Solution
Samsara first appeared on David’s radar during a quarterly best practices review where the plant manager for their Phenix City facility shared insights on using Samsara sensors for monitoring dryer temperatures. After further conversations, David realized Samsara’s Manufacturing Analytics solution, with its automatic downtime logging and flexible connectivity options, was a great answer to their most immediate data challenges surrounding inaccurate manual data. They had explored other solutions in the past, but they either didn’t have the connectivity options for their facilities or were priced for much larger enterprises. Samsara offered a compelling feature set at a price point that made it a no-brainer. Unlike other solutions - which required Wi-Fi access and created broader corporate concerns around network privacy - Samsara was able to provide the Manufacturing Analytics solution entirely through cellular signal, allowing for fast and secure deployment to get the system up and running. The plant managers for Meridian Brick’s Columbia and Augusta facilities quickly saw the value of Samsara Manufacturing Analytics as well, and both sites were able to self-install Samsara with minimal support. Samsara’s ease of use has made it an instant hit on the production floor as well. Operators at the Columbia facility were able to start and stop runs, enter downtime reasons, and view production progress through the Samsara HMI interface with zero training. Compared to the hours of manual work previously needed each week to log data, input the data into spreadsheets, and create customized reports, adding new products or shift schedules could be done in the Samsara dashboard in just a few clicks.
Operational Impact
Quantitative Benefit
Case Study missing?
Start adding your own!
Register with your work email and create a new case study profile for your business.
Related Case Studies.

Case Study
IoT System for Tunnel Construction
The Zenitaka Corporation ('Zenitaka') has two major business areas: its architectural business focuses on structures such as government buildings, office buildings, and commercial facilities, while its civil engineering business is targeted at structures such as tunnels, bridges and dams. Within these areas, there presented two issues that have always persisted in regard to the construction of mountain tunnels. These issues are 'improving safety" and "reducing energy consumption". Mountain tunnels construction requires a massive amount of electricity. This is because there are many kinds of electrical equipment being used day and night, including construction machinery, construction lighting, and ventilating fan. Despite this, the amount of power consumption is generally not tightly managed. In many cases, the exact amount of power consumption is only ascertained when the bill from the power company becomes available. Sometimes, corporations install demand-monitoring equipment to help curb the maximum power demanded. However, even in these cases, the devices only allow the total volume of power consumption to be ascertained, or they may issue warnings to prevent the contracted volume of power from being exceeded. In order to tackle the issue of reducing power consumption, it was first necessary to obtain an accurate breakdown of how much power was being used in each particular area. In other words, we needed to be able to visualize the amount of power being consumed. Safety, was also not being managed very rigorously. Even now, tunnel construction sites often use a 'name label' system for managing entry into the work site. Specifically, red labels with white reverse sides that bear the workers' names on both sides are displayed at the tunnel work site entrance. The workers themselves then flip the name label to the appropriate side when entering or exiting from the work site to indicate whether or not they are working inside the tunnel at any given time. If a worker forgets to flip his or her name label when entering or exiting from the tunnel, management cannot be performed effectively. In order to tackle the challenges mentioned above, Zenitaka decided to build a system that could improve the safety of tunnel construction as well as reduce the amount of power consumed. In other words, this new system would facilitate a clear picture of which workers were working in each location at the mountain tunnel construction site, as well as which processes were being carried out at those respective locations at any given time. The system would maintain the safety of all workers while also carefully controlling the electrical equipment to reduce unnecessary power consumption. Having decided on the concept, our next concern was whether there existed any kind of robust hardware that would not break down at the construction work site, that could move freely in response to changes in the working environment, and that could accurately detect workers and vehicles using radio frequency identification (RFID). Given that this system would involve many components that were new to Zenitaka, we decided to enlist the cooperation of E.I.Sol Co., Ltd. ('E.I.Sol') as our joint development partner, as they had provided us with a highly practical proposal.
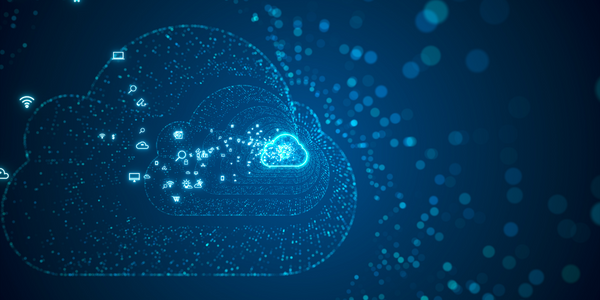
Case Study
Splunk Partnership Ties Together Big Data & IoT Services
Splunk was faced with the need to meet emerging customer demands for interfacing IoT projects to its suite of services. The company required an IoT partner that would be able to easily and quickly integrate with its Splunk Enterprise platform, rather than allocating development resources and time to building out an IoT interface and application platform.
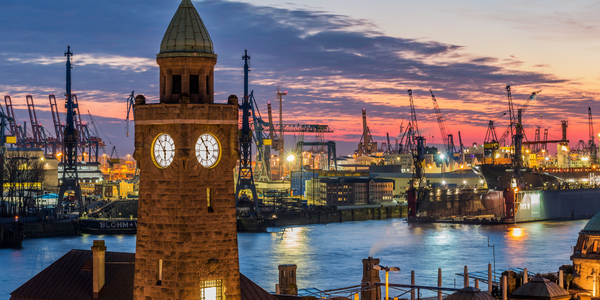
Case Study
Bridge monitoring in Hamburg Port
Kattwyk Bridge is used for both rail and road transport, and it has played an important role in the Port of Hamburg since 1973. However, the increasing pressure from traffic requires a monitoring solution. The goal of the project is to assess in real-time the bridge's status and dynamic responses to traffic and lift processes.
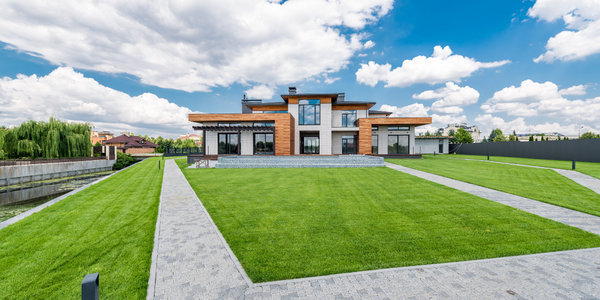
Case Study
Bellas Landscaping
Leading landscaping firm serving central Illinois streamlines operations with Samsara’s real-time fleet tracking solution: • 30+ vehicle fleet includes International Terrastar dump trucks and flatbeds, medium- and light-duty pickups from Ford and Chevrolet. Winter fleet includes of snow plows and salters.
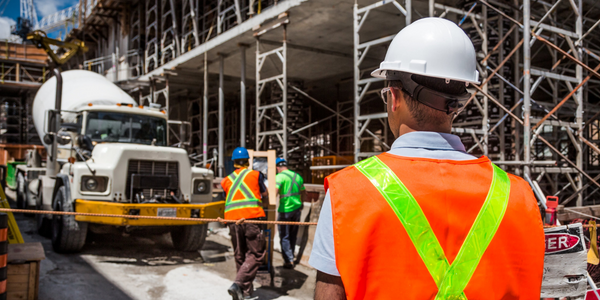
Case Study
Condition Based Monitoring for Industrial Systems
A large construction aggregate plant operates 10 high horsepower Secondary Crusher Drive Motors and associated conveyor belts, producing 600 tons of product per hour. All heavy equipment requires maintenance, but the aggregate producer’s costs were greatly magnified any time that the necessary maintenance was unplanned and unscheduled. The product must be supplied to the customers on a tight time schedule to fulfill contracts, avoid penalties, and prevent the loss of future business. Furthermore, a sudden failure in one of the drive motors would cause rock to pile up in unwanted locations, extending the downtime and increasing the costs.Clearly, preventative maintenance was preferable to unexpected failures. So, twice each year, the company brought in an outside vendor to attach sensors to the motors, do vibration studies, measure bearing temperatures and attempt to assess the health of the motors. But that wasn’t enough. Unexpected breakdowns continued to occur. The aggregate producer decided to upgrade to a Condition Based Monitoring (CBM) sensor system that could continually monitor the motors in real time, apply data analytics to detect changes in motor behavior before they developed into major problems, and alert maintenance staff via email or text, anywhere they happened to be.A wired sensor network would have been cost prohibitive. An aggregate plant has numerous heavy vehicles moving around, so any cabling would have to be protected. But the plant covers 400 acres, and the cable would have to be trenched to numerous locations. Cable wasn’t going to work. The aggregate producer needed a wireless solution.