Company Size
1,000+
Region
- America
Country
- United States
Product
- Blue Yonder Warehouse Management
Tech Stack
- Warehouse Management System (WMS)
Implementation Scale
- Enterprise-wide Deployment
Impact Metrics
- Cost Savings
- Productivity Improvements
Technology Category
- Functional Applications - Warehouse Management Systems (WMS)
Applicable Industries
- Healthcare & Hospitals
Applicable Functions
- Warehouse & Inventory Management
Use Cases
- Inventory Management
- Warehouse Automation
Services
- System Integration
About The Customer
Medifast is a rapidly growing company that provides clinically proven, easy-to-follow weight-loss plans to help customers lose weight quickly and safely. The company operates several distribution centers and was facing challenges in scaling its operations to accommodate increasing volume. Medifast was looking for a solution to optimize its distribution center operations, decrease labor costs in the shipping function, save in annual shipping costs, and reduce unloading time for trucks.
The Challenge
Medifast, a rapidly growing company, was facing challenges in scaling its ERP system to accommodate the increasing volume in each of its distribution centers. The company's goals were to decrease labor costs in the shipping function, save in annual shipping costs, and reduce unloading time for trucks by optimizing their distribution center operations. Prior to implementing a new solution, Medifast employees were hand-selecting boxes, measuring efficiency based on speed, and required two employees to scan, weigh, and apply shipping labels. This process was inefficient and led to excessive use of void fill and delays from repacking.
The Solution
Medifast implemented Blue Yonder Warehouse Management, a Warehouse Management System (WMS), to optimize its distribution center operations. The system provided real-time visibility into what was happening on the warehouse floor, enabling quicker and more effective decision-making. The direct-to-work queue in the warehouse management system allowed about 40 percent of Medifast’s distribution employees to work on tasks assigned by the system. This eliminated paperwork and movement transactions, enabling employees to work in real-time alongside the system. The system also had the product weights and dimensions loaded into it, which allowed it to choose the right box and apply the shipping label on the front end before the order was picked. This reduced double touches and wasted labor.
Operational Impact
Quantitative Benefit
Case Study missing?
Start adding your own!
Register with your work email and create a new case study profile for your business.
Related Case Studies.
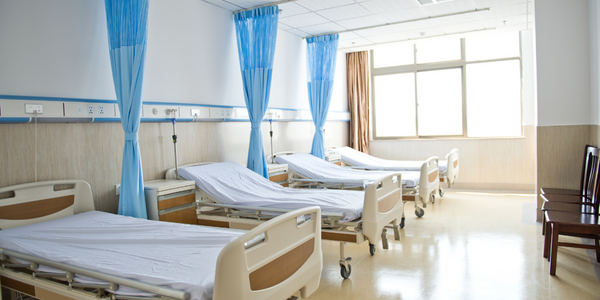
Case Study
Hospital Inventory Management
The hospital supply chain team is responsible for ensuring that the right medical supplies are readily available to clinicians when and where needed, and to do so in the most efficient manner possible. However, many of the systems and processes in use at the cancer center for supply chain management were not best suited to support these goals. Barcoding technology, a commonly used method for inventory management of medical supplies, is labor intensive, time consuming, does not provide real-time visibility into inventory levels and can be prone to error. Consequently, the lack of accurate and real-time visibility into inventory levels across multiple supply rooms in multiple hospital facilities creates additional inefficiency in the system causing over-ordering, hoarding, and wasted supplies. Other sources of waste and cost were also identified as candidates for improvement. Existing systems and processes did not provide adequate security for high-cost inventory within the hospital, which was another driver of cost. A lack of visibility into expiration dates for supplies resulted in supplies being wasted due to past expiry dates. Storage of supplies was also a key consideration given the location of the cancer center’s facilities in a dense urban setting, where space is always at a premium. In order to address the challenges outlined above, the hospital sought a solution that would provide real-time inventory information with high levels of accuracy, reduce the level of manual effort required and enable data driven decision making to ensure that the right supplies were readily available to clinicians in the right location at the right time.
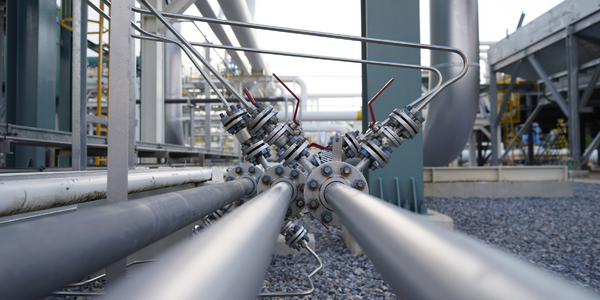
Case Study
Gas Pipeline Monitoring System for Hospitals
This system integrator focuses on providing centralized gas pipeline monitoring systems for hospitals. The service they provide makes it possible for hospitals to reduce both maintenance and labor costs. Since hospitals may not have an existing network suitable for this type of system, GPRS communication provides an easy and ready-to-use solution for remote, distributed monitoring systems System Requirements - GPRS communication - Seamless connection with SCADA software - Simple, front-end control capability - Expandable I/O channels - Combine AI, DI, and DO channels
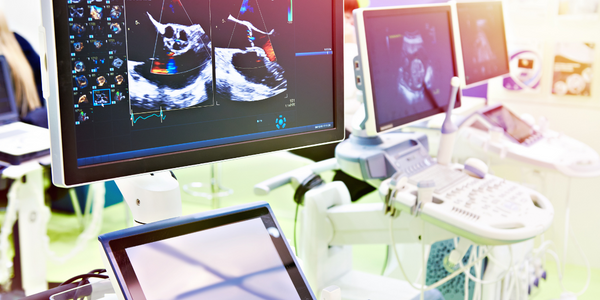
Case Study
Driving Digital Transformations for Vitro Diagnostic Medical Devices
Diagnostic devices play a vital role in helping to improve healthcare delivery. In fact, an estimated 60 percent of the world’s medical decisions are made with support from in vitrodiagnostics (IVD) solutions, such as those provided by Roche Diagnostics, an industry leader. As the demand for medical diagnostic services grows rapidly in hospitals and clinics across China, so does the market for IVD solutions. In addition, the typically high cost of these diagnostic devices means that comprehensive post-sales services are needed. Wanteed to improve three portions of thr IVD:1. Remotely monitor and manage IVD devices as fixed assets.2. Optimizing device availability with predictive maintenance.3. Recommending the best IVD solution for a customer’s needs.
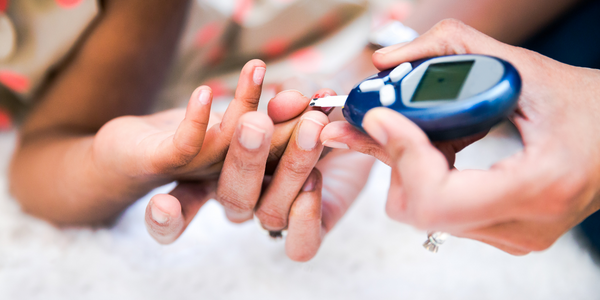
Case Study
HaemoCloud Global Blood Management System
1) Deliver a connected digital product system to protect and increase the differentiated value of Haemonetics blood and plasma solutions. 2) Improve patient outcomes by increasing the efficiency of blood supply flows. 3) Navigate and satisfy a complex web of global regulatory compliance requirements. 4) Reduce costly and labor-intensive maintenance procedures.
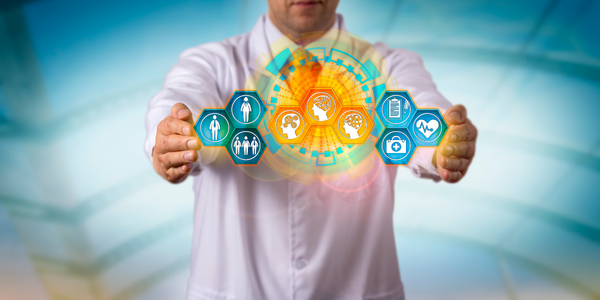
Case Study
Harnessing real-time data to give a holistic picture of patient health
Every day, vast quantities of data are collected about patients as they pass through health service organizations—from operational data such as treatment history and medications to physiological data captured by medical devices. The insights hidden within this treasure trove of data can be used to support more personalized treatments, more accurate diagnosis and more advanced preparative care. But since the information is generated faster than most organizations can consume it, unlocking the power of this big data can be a struggle. This type of predictive approach not only improves patient care—it also helps to reduce costs, because in the healthcare industry, prevention is almost always more cost-effective than treatment. However, collecting, analyzing and presenting these data-streams in a way that clinicians can easily understand can pose a significant technical challenge.