Company Size
1,000+
Region
- America
Country
- United States
Product
- nGeniusONE Service Assurance platform
- InfiniStreamNG appliances
- vSTREAM virtual appliances
Tech Stack
- VMware ESX servers
Implementation Scale
- Enterprise-wide Deployment
Impact Metrics
- Cost Savings
- Productivity Improvements
Technology Category
- Analytics & Modeling - Real Time Analytics
- Application Infrastructure & Middleware - Data Exchange & Integration
Applicable Industries
- Electronics
Applicable Functions
- Discrete Manufacturing
- Quality Assurance
Use Cases
- Manufacturing System Automation
- Predictive Maintenance
Services
- Cloud Planning, Design & Implementation Services
- System Integration
About The Customer
This large North American manufacturer builds and sells household appliances, electric motors, lighting products, and many other electrical products for household, commercial, and industrial applications. From small to large appliances for the kitchen and laundry room to commercial HVAC systems, this manufacturer has become a staple in homes and businesses around the world. Their other products range from state-of-the-art light bulbs and specialized lighting solutions, to household and industrial motors and generators. With dozens of factories and R&D facilities worldwide, as well as, point-of-sale ordering capabilities throughout stores in multiple large retail chains, IT service performance is critical.
The Challenge
The company’s distributed, worldwide factories are critical to achieving overall production quotas, and they must perform as well as the main manufacturing facilities. Not surprisingly, the distributed plants rely heavily on IT technology, such as automated assembly lines that communicate instructions and status between equipment on the lines. In addition, not all the company’s remote facilities use centralized IT services; rather, they use locally hosted applications. These remote facilities are run on a “network in a box,” where VMware ESX servers are used to host manufacturing / production applications that are responsible for bar code scanning, printing, and communications as well as underlying network protocols like DNS, file services, and LDAP. These applications are critical to operating the production line and business processes at the plants. When communication between machines slows or stops, the symptoms may not be quickly apparent locally and can persist for a few hours, leading to delays on the lines, halting the lines completely, or creating issues requiring rework.
The Solution
The networking staff selected the vSTREAM virtual appliance that complements existing ASI-based InfiniStreamNG hardware instrumentation to provide the same level of visibility at each of the factories and directly on the applications supporting the production lines. With vSTREAM, they were able to implement local monitoring directly on the “network in a box” on the ESX servers already deployed at each remote facility, providing proactive network and application monitoring. At very small sites, vSTREAMs are implemented on server blades where “network in a router” configurations are deployed. The network operations team now has visibility to services in action at the plants, ranging from the bar code application for inventory management to the assembly line, to maintain efficient production services.
Operational Impact
Quantitative Benefit
Case Study missing?
Start adding your own!
Register with your work email and create a new case study profile for your business.
Related Case Studies.

Case Study
Remote Temperature Monitoring of Perishable Goods Saves Money
RMONI was facing temperature monitoring challenges in a cold chain business. A cold chain must be established and maintained to ensure goods have been properly refrigerated during every step of the process, making temperature monitoring a critical business function. Manual registration practice can be very costly, labor intensive and prone to mistakes.
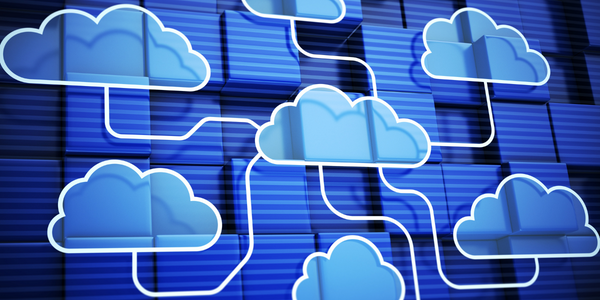
Case Study
Cloud Solution for Energy Management Platform-Schneider Electric
Schneider Electric required a cloud solution for its energy management platform to manage high computational operations, which were essential for catering to client requirements. As the business involves storage and analysis of huge amounts of data, the company also needed a convenient and scalable storage solution to facilitate operations efficiently.
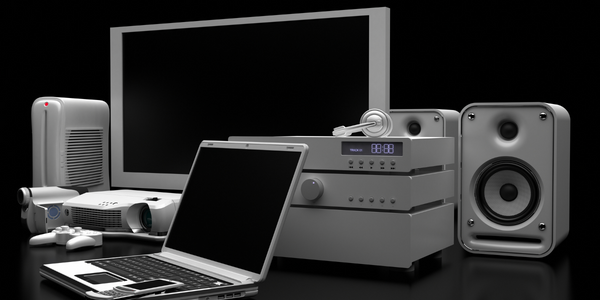
Case Study
Leveraging the IoT to Gain a Competitive Edge in International Competition
Many large manufacturers in and outside Japan are competing for larger market share in the same space, expecting a growing demand for projectors in the areas of entertainment, which requires glamor and strong visual performance as well as digital signage that can attract people’s attention. “It is becoming more and more difficult to differentiate ourselves with stand-alone hardware products,” says Kazuyuki Kitagawa, Director of Service & Support at Panasonic AVC Networks. “In order for Panasonic to grow market share and overall business, it is essential for us to develop solutions that deliver significant added value.” Panasonic believes projection failure and quality deterioration should never happen. This is what and has driven them to make their projectors IoT-enabled. More specifically, Panasonic has developed a system that collects data from projectors, visualizes detailed operational statuses, and predicts issues and address them before failure occurs. Their projectors are embedded with a variety of sensors that measure power supply, voltage, video input/ output signals, intake/exhaust air temperatures, cooling fan operations, and light bulb operating time. These sensors have been used to make the projector more intelligent, automatically suspending operation when the temperature rises excessively, and automatically switching light bulbs. Although this was a great first step, Panasonic projectors were still not equipped with any capability to send the data over a network.