Company Size
11-200
Region
- America
Country
- United States
Product
- Granular
Tech Stack
- Mobile Application
Implementation Scale
- Enterprise-wide Deployment
Impact Metrics
- Cost Savings
- Productivity Improvements
Technology Category
- Functional Applications - Inventory Management Systems
Applicable Industries
- Agriculture
Applicable Functions
- Logistics & Transportation
- Procurement
Use Cases
- Inventory Management
Services
- Software Design & Engineering Services
About The Customer
Clete Inc. is a diversified farming and cattle operation based in Gering, NE. The company farms corn, sugar beets, wheat, dry edible beans, and alfalfa, mostly under irrigation. They also run a cow/calf herd and operate three feedlots. The company is managed by Jeana Harms, the CFO, who has a background in finance and accounting. She worked as a loan officer at Farm Credit before joining Clete Inc. Her role at Clete Inc. extends beyond managing the financials; she is also responsible for all data management. She works closely with the farm owners, the agronomist, and the operations manager to plan and manage the farming operations.
The Challenge
Clete Inc., a diversified farming and cattle operation, was facing challenges in managing their input inventories. The process of planning for the inputs needed each growing season was manual and time-consuming. The team had to sit together to decide the acreage for each crop and then manually estimate the required inputs. They relied heavily on local suppliers for their inputs and valued the customer service and timely delivery. However, unexpected changes in plans or field activity often led to discrepancies and required constant communication and updates. The company was using Excel for inventory management, which was not efficient and prone to errors.
The Solution
Clete Inc. implemented Granular, a software solution, to manage their input inventories. The software helps them develop their crop plans and provides a quick total of each product they will need for the upcoming year. Granular is also used to manage unexpected changes in plans or field activity. If a change is known before the operator is in the field, the task is changed in Granular so that the work order is correct. If a change occurs while the operator is in the field, the operator can change it on the Granular app on his phone. As the tasks are completed and deliveries are made, the inventory in Granular is updated, providing real-time visibility into the inventory levels.
Operational Impact
Case Study missing?
Start adding your own!
Register with your work email and create a new case study profile for your business.
Related Case Studies.
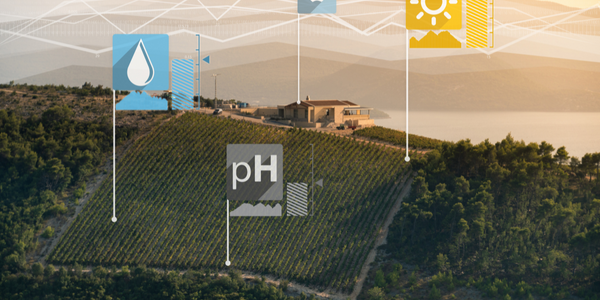
Case Study
Intelligent Farming with ThingWorx Analytics
Z Farms was facing three challenges: costly irrigation systems with water as a limited resource, narrow optimal ranges of soil moisture for growth with difficult maintenance and farm operators could not simply turn on irrigation systems like a faucet.
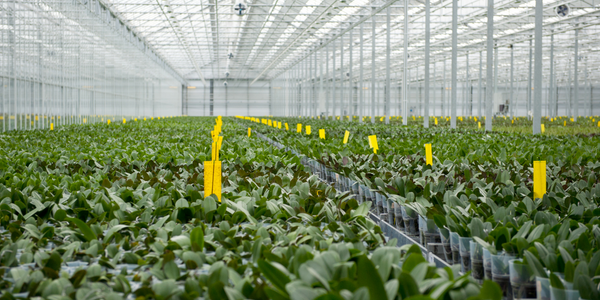
Case Study
Greenhouse Intelligent Monitoring and Control Solution
Farming Orchids is the most successful form of precision farming in Taiwan, and also the most exported flower. Orchids need a specific temperature and humidity conditions to grow and bloom, and its flowering time may not be in line with market demands, so the price collapses when there is overproduction. Therefore, some farmers began to import automated greenhouse control systems for breeding and forcing, which not only improves quality, but also effectively controls the production period and yield to ensure revenue. In 2012, an orchid farmer built a Forcing Greenhouse of about 200 pings (approximately 661 Square Meters) in Tainan, Taiwan. The system integrator adopted Advantech’s APAX-5000 series programmable automation controllers to build the control platform, coupled with Advantech WebAccess HMI/SCADA software, to achieve cloud monitoring. The staff of the orchid field can monitor important data anytime via smart phone, iPad, and other handheld devices, and control the growth and flowering conditions. System requirements: In the past, most environmental control systems of orchid greenhouses in Taiwan used PLCs (Programmable Logic Controller) with poorscalability and control, and could not be connected to the Internet formonitoring from the cloud. For advanced database analysis and networking capability, the PC platform must be adopted. Therefore, PAC Systems (Programmable Automation Controller) with both PLC programming capabilities andPC functions is a better choice.The environmental control of the Orchid greenhouse switches on and off devices like fan, shade net, cooling/heat pump, liquid flow control, water-cooling wall etc. It is controlled by a control panel of electric controllers, and is driven by a motor, to adjust the greenhouse temperature, humidity, and other environmental conditions to the set parameters.
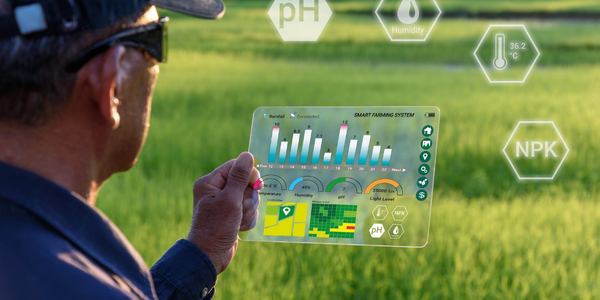
Case Study
Enabling Internet of Things Innovation in Agriculture
DigiBale, wanted to apply technology know-how and IP from implementations successfully to more agriculture sectors including cotton, forestry, sugarcane and cattle. However, farmers and growers still have worries about the connected technology.
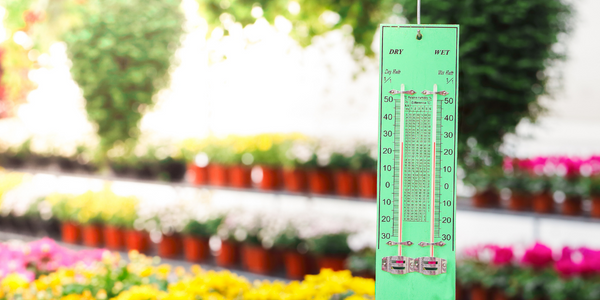
Case Study
Precision beekeeping with wireless temperature monitoring
Honeybees are insects of large economic value and provide a vital service to agriculture by pollinating a variety of crops. In addition, bees provide us with valuable products such as honey, beeswax, propolis, bee venom, etc. Monitoring of honeybee colony health, population, productivity, and environmental conditions affecting the colony health have always been exceedingly difficult tasks in apiculture. Research has shown that even small deviations (by more than 2°C) from the optimal temperatures have a significant influence on the development of the brood and the health of adult bees.