Technology Category
- Analytics & Modeling - Digital Twin / Simulation
- Platform as a Service (PaaS) - Application Development Platforms
Applicable Industries
- Electronics
- Packaging
Applicable Functions
- Product Research & Development
- Quality Assurance
Use Cases
- Time Sensitive Networking
- Visual Quality Detection
Services
- System Integration
- Testing & Certification
About The Customer
Lenovo is a Chinese multinational technology company with headquarters in Beijing, China and North Carolina, USA. Founded in 1984, Lenovo has a 30-year history and in 2013, it became the world's number one personal computer manufacturer. Lenovo manufactures a wide range of products including personal computers, tablet computers, smartphones, workstations, servers, electronic storage devices, and smart televisions. The company operates in more than 60 countries and sells its products in over 160 countries. Lenovo has a dedicated CAE technology platform in its Beijing Innovation Design Center, which supports the development of all its product series.
The Challenge
Lenovo, a leading multinational technology company, was facing intense competition in the computer industry, which necessitated continuous cost reduction, improved product quality and reliability, and shortened product development cycles. The traditional product development methodology was no longer efficient for rapid time to market. Lenovo sought to use computer-aided engineering (CAE) tools for optimizing performance in the initial product design phase to simulate and evaluate its products’ mechanical behavior under loads like impact and vibration. However, engineers were spending 80 percent of their time on pre-processing tasks in the simulation process. The pre-processing tools provided by some CAE software offerings were not strong enough to meet the manufacturer’s requirements, and the quality of the pre-processing mesh was not dependable. Lenovo needed a powerful pre-processing tool that would meet the demands of scientific research and engineering innovation.
The Solution
Lenovo chose HyperMesh, an important component of the Altair HyperWorks suite, to increase efficiency, improve the quality of meshing, and shorten CAE simulation time. HyperMesh is a high-performance finite element pre-processor that provides a highly interactive and visual environment to analyze product design performance. It delivered the speed-to-quality results that Lenovo was seeking, yielding results that enabled a very fast development cycle. Lenovo also expanded their use of the HyperWorks suite to apply OptiStruct to the design of hard-disk drives. OptiStruct was used to optimize the system, overcoming many of the frustrations inherent in the trial and error method. Lenovo’s engineers conducted modal analysis with OptiStruct to optimize the fixed side of the computer system, averting resonance with the 120 Hz natural frequency of the spinning hard-disk. Lenovo also capitalized on the user-friendly HyperMesh interface with CFD software and powerful geometric processing to quickly generate high-quality CFD elements.
Operational Impact
Quantitative Benefit
Case Study missing?
Start adding your own!
Register with your work email and create a new case study profile for your business.
Related Case Studies.

Case Study
Remote Temperature Monitoring of Perishable Goods Saves Money
RMONI was facing temperature monitoring challenges in a cold chain business. A cold chain must be established and maintained to ensure goods have been properly refrigerated during every step of the process, making temperature monitoring a critical business function. Manual registration practice can be very costly, labor intensive and prone to mistakes.
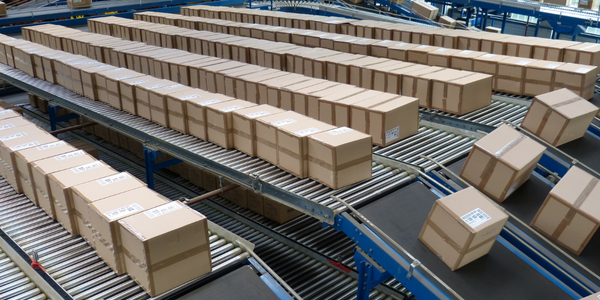
Case Study
IoT Data Analytics Case Study - Packaging Films Manufacturer
The company manufactures packaging films on made to order or configure to order basis. Every order has a different set of requirements from the product characteristics perspective and hence requires machine’s settings to be adjusted accordingly. If the film quality does not meet the required standards, the degraded quality impacts customer delivery causes customer dissatisfaction and results in lower margins. The biggest challenge was to identify the real root cause and devise a remedy for that.
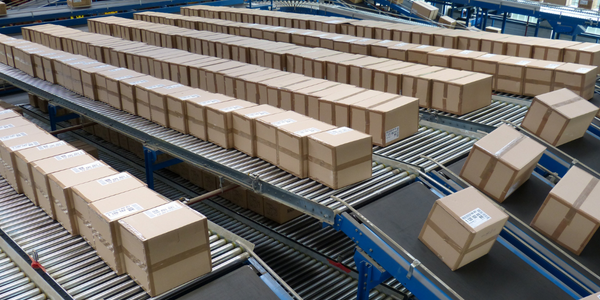
Case Study
Zenon the Ideal Basis for An Ergonomic HMI
KHS develops and produces machines and equipment for filling and packaging in the drinks industry. Because drinks manufacturing, filling and packaging consist of a number of highly complex processes, the user-friendly and intuitive operation of equipment is increasingly gaining in significance. In order to design these processes as simple as possible for the user, KHS decided to introduce a uniform, transparent and standardized solution to the company. The HMI interface should meet the requirement for people with different qualifications and enable them to work on a standard platform.
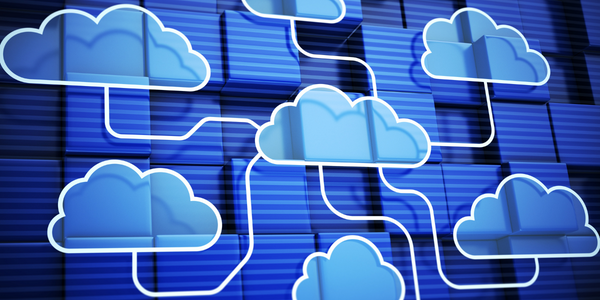
Case Study
Cloud Solution for Energy Management Platform-Schneider Electric
Schneider Electric required a cloud solution for its energy management platform to manage high computational operations, which were essential for catering to client requirements. As the business involves storage and analysis of huge amounts of data, the company also needed a convenient and scalable storage solution to facilitate operations efficiently.