Leading Pulp & Paper Manufacturer Detects and Avoids Major Fire Using Aspen Mtell
Product
- Aspen Mtell
Tech Stack
- Machine Learning
- Data Analysis
Implementation Scale
- Enterprise-wide Deployment
Impact Metrics
- Productivity Improvements
- Cost Savings
Technology Category
- Analytics & Modeling - Machine Learning
Applicable Industries
- Paper & Pulp
Applicable Functions
- Process Manufacturing
Use Cases
- Predictive Maintenance
Services
- Data Science Services
About The Customer
The customer in this case study is a leading manufacturer in the Pulp & Paper industry. The company operates a wood products processing plant where it faced challenges with process and mechanical events that were causing product quality and throughput interruptions. These interruptions were leading to product losses and potential operational shutdowns. The company needed a solution that could help it detect and prevent these events to maintain product quality and avoid costly shutdowns.
The Challenge
The company faced process and mechanical events at one of its wood products processing plants that had created product quality and throughput interruptions, causing product losses. The challenge was to identify and prevent these events to avoid operational shutdowns and maintain product quality.
The Solution
The company implemented Aspen Mtell, a machine learning solution that scans archived data in the plant historian and correlates it with posted failure incidents in its asset management system. Aspen Mtell was able to identify the failure signature for an overheating situation in a kiln. The solution's industrial machine learning found this same pattern among dozens of sensor signal data streams, where no single sensor could provide a clear indication of impending failure. Live autonomous agents then constantly monitored incoming signals for this failure signature.
Operational Impact
Quantitative Benefit
Case Study missing?
Start adding your own!
Register with your work email and create a new case study profile for your business.
Related Case Studies.

Case Study
Wireless Improves Efficiency in Compressed Air Systems
Hollingsworth and Vose wanted to improve the efficiency of their compressed air system, lower the electricity expense component of manufacturing cost in their commodity industry, and conserve energy leading to lowered greenhouse gas emissions. Compressed air systems degrade over time and become leaky and inefficient. Hollingsworth and Vose wanted to increase the frequency of system inspections without paying the high cost of manual labor.
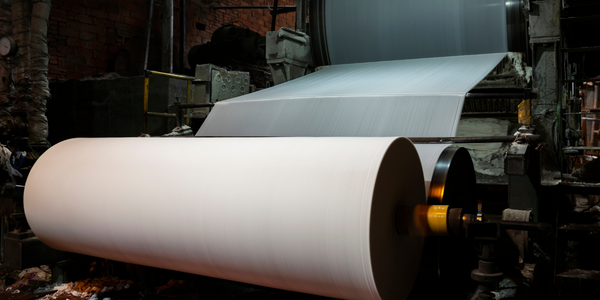
Case Study
Process Predictive Analysis in Pulp and Paper Mill
Common paper breaks consequently lead up to 60 minutes of downtime, delaying a potential $10K per hour of production value process. Thus, defective products cause financial and damage company's reputation. Improving quality and reducing defect rates can generate millions of dollars of revenue per year for your company.
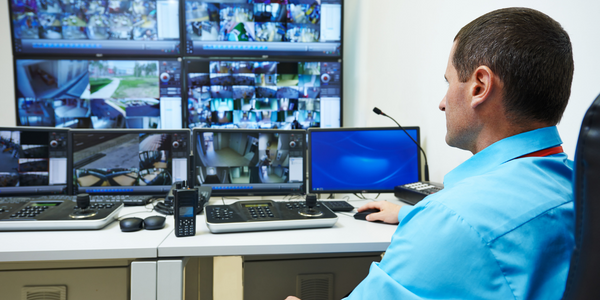
Case Study
Industrial Video Monitoring for Security and Regulatory Compliance
Because of the Stevenson mill’s proximity to the Tennessee River, WestRock was required by the USCG to comply with the Maritime Security 33CFR (MARSEC) regulations. WestRock needed a video security system but wanted to add other applications not required by the government, such as video process monitoring, condition monitoring, and wireless network management. WestRock needed a reliable video solution to avoid the compliance fines and possible security risks – but the solution needed to be implemented in the most cost-effective manner possible.
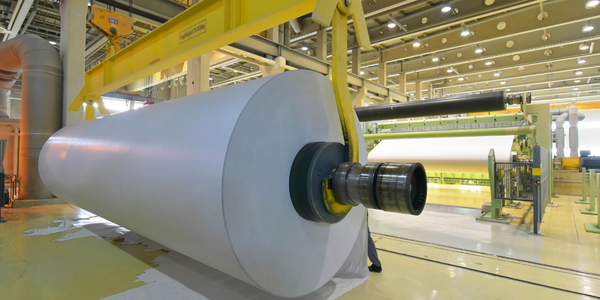
Case Study
ECOsine Active Increased Reliability in the Paper Industry
The paper and pulp industry is interlinking intelligent hi-tech machines to highly efficient production lines. Higher power DC and AC motor drives perform the automation tasks. Every kind of interference that negatively affects the reliability and safety of the installation may lead to production downtime and consequently to significant financial losses. AC and DC motor drives are so-called non-linear loads as they draw a nonsinusoidal current from the grid. Resulting harmonics of current and voltage can interfere with the operation of nearby consumers and overload the electrical infrastructure. In this particular application, the load cycles of the drives often caused interruptions in the production process because of disturbances coupling into the fieldbus system.