Customer Company Size
Mid-size Company
Region
- America
Country
- United States
Product
- Kuebix TMS
- EFI Monarch
Tech Stack
- Cloud Computing
- ERP Integration
Implementation Scale
- Enterprise-wide Deployment
Impact Metrics
- Productivity Improvements
- Customer Satisfaction
Technology Category
- Platform as a Service (PaaS) - Connectivity Platforms
Applicable Functions
- Logistics & Transportation
Use Cases
- Supply Chain Visibility
- Inventory Management
Services
- System Integration
About The Customer
Grandville Printing has been a fixture in Grandville, MI for 64 years. As a third-generation family owned and operated business, the company has built its roots in its community and has grown to become the largest single-site printer in North America. Grandville Printing ships roughly 60,000 to 80,000 skids every year across the country as well as into Canada and the Bahamas. Their mission is to offer products for clients who need real solutions… more than just ink on paper. The company prides itself on being technologically savvy and understands the value of automation and operating in a digital, cloud environment.
The Challenge
Grandville Printing, a third-generation family-owned business and the largest single-site printer in North America, was facing challenges with its home-grown shipping platform. The platform required constant updating, especially when a carrier changed their website, which wasted valuable time for their developers. The platform also didn't integrate information with EFI Monarch, the company's ERP, resulting in wasted time, limited visibility, and slower operations. The company tried leveraging their ERP’s shipping software to integrate data flows and condense operations, but found that this solution lacked the ease of use and functionality they required.
The Solution
Grandville Printing first began using Kuebix Free Shipper to supplement the capabilities of their home-grown technology. After successfully using the free TMS in tandem with their own software, Grandville decided to assess Kuebix Business Pro and the modular features Kuebix offers. The company knew they needed a shipping solution that would do more than they could in-house while also integrating with their ERP system for efficient data flow. Grandville Printing’s entire logistics team now leverages Kuebix TMS to manage shipping operations. Working closely with Kuebix’s Development and Customer Success teams, the company’s order and shipment data were successfully integrated.
Operational Impact
Case Study missing?
Start adding your own!
Register with your work email and create a new case study profile for your business.
Related Case Studies.

Case Study
Remote Temperature Monitoring of Perishable Goods Saves Money
RMONI was facing temperature monitoring challenges in a cold chain business. A cold chain must be established and maintained to ensure goods have been properly refrigerated during every step of the process, making temperature monitoring a critical business function. Manual registration practice can be very costly, labor intensive and prone to mistakes.
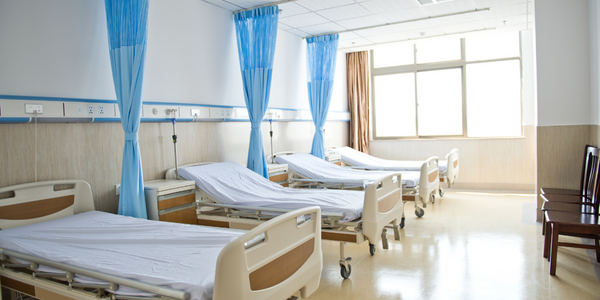
Case Study
Hospital Inventory Management
The hospital supply chain team is responsible for ensuring that the right medical supplies are readily available to clinicians when and where needed, and to do so in the most efficient manner possible. However, many of the systems and processes in use at the cancer center for supply chain management were not best suited to support these goals. Barcoding technology, a commonly used method for inventory management of medical supplies, is labor intensive, time consuming, does not provide real-time visibility into inventory levels and can be prone to error. Consequently, the lack of accurate and real-time visibility into inventory levels across multiple supply rooms in multiple hospital facilities creates additional inefficiency in the system causing over-ordering, hoarding, and wasted supplies. Other sources of waste and cost were also identified as candidates for improvement. Existing systems and processes did not provide adequate security for high-cost inventory within the hospital, which was another driver of cost. A lack of visibility into expiration dates for supplies resulted in supplies being wasted due to past expiry dates. Storage of supplies was also a key consideration given the location of the cancer center’s facilities in a dense urban setting, where space is always at a premium. In order to address the challenges outlined above, the hospital sought a solution that would provide real-time inventory information with high levels of accuracy, reduce the level of manual effort required and enable data driven decision making to ensure that the right supplies were readily available to clinicians in the right location at the right time.