Technology Category
- Functional Applications - Manufacturing Execution Systems (MES)
- Sensors - Autonomous Driving Sensors
Applicable Industries
- Automotive
- Plastics
Applicable Functions
- Product Research & Development
Use Cases
- Manufacturing Process Simulation
- Smart Parking
About The Customer
KTM Technologies GmbH, founded in 2008, is a high-tech composites engineering and design company for the KTM group, a world leader in developing race-ready off-road and street motorcycles. With the development of the KTM X-Bow, the first four-wheel vehicle in KTM's motorsports history, KTM Technologies showcases its remarkable expertise and success in the field of high-performance composites. The company is known for bundling competencies in high-tech composites engineering and design, and the KTM X-Bow is a testament to their innovative approach and technical prowess.
The Challenge
KTM Technologies was tasked with the development of the KTM X-Bow, a unique super sports car featuring a monocoque made from carbon composites materials. The monocoque, the external skin of the vehicle, provides structural support, marking it as the world's first production car with such a feature. The challenge lay in the use of carbon composites, which, while ideal for their lightweight and high strength properties, presented engineering complexities. The process of engineering composites designs from concept to simulation and manufacturing included countless opportunities for engineers to choose materials, fiber orientation, manufacturing methods, and layup arrangements. The KTM X-Bow monocoque was to be manufactured using over 300 pre-cut composite plies, adding to the complexity of the task. The challenge was to address these complexities in composites engineering to develop one of the world's most exciting and modern sports cars.
The Solution
KTM Technologies turned to ANSYS for a solution. They used ANSYS Composite PrepPost to model and analyze the composites monocoque. This allowed them to analyze different possible layups, fiber orientations, and composites materials. They were also able to analyze the failure behavior of the composites design under different load scenarios. The intuitive approach of ANSYS Composite PrepPost enabled simulation-driven development of the composites monocoque. The simulation started with design concepts, included the influences of manufacturing, and allowed detailed evaluation of the monocoque. Different design studies of the composites layup were evaluated within a single day, speeding up the development process.
Operational Impact
Quantitative Benefit
Case Study missing?
Start adding your own!
Register with your work email and create a new case study profile for your business.
Related Case Studies.

Case Study
Plastic Spoons Case study: Injection Moulding
In order to meet customer expectations by supplying a wide variety of packaging units, from 36 to 1000 spoons per package, a new production and packaging line needed to be built. DeSter wanted to achieve higher production capacity, lower cycle time and a high degree of operator friendliness with this new production line.
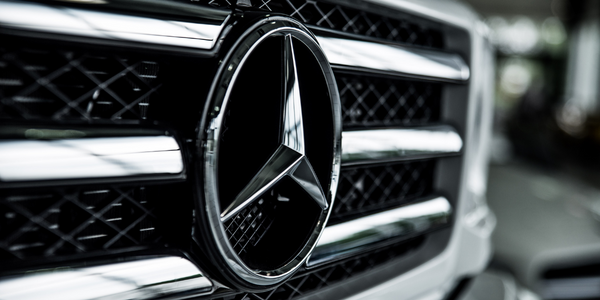
Case Study
Integral Plant Maintenance
Mercedes-Benz and his partner GAZ chose Siemens to be its maintenance partner at a new engine plant in Yaroslavl, Russia. The new plant offers a capacity to manufacture diesel engines for the Russian market, for locally produced Sprinter Classic. In addition to engines for the local market, the Yaroslavl plant will also produce spare parts. Mercedes-Benz Russia and his partner needed a service partner in order to ensure the operation of these lines in a maintenance partnership arrangement. The challenges included coordinating the entire maintenance management operation, in particular inspections, corrective and predictive maintenance activities, and the optimizing spare parts management. Siemens developed a customized maintenance solution that includes all electronic and mechanical maintenance activities (Integral Plant Maintenance).
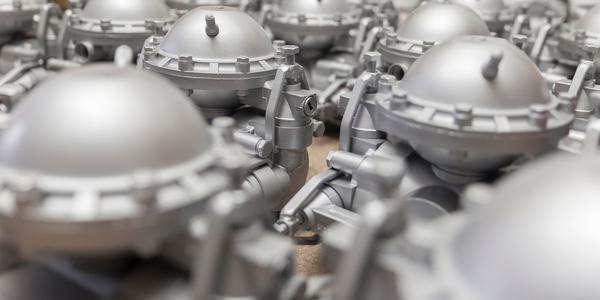
Case Study
Monitoring of Pressure Pumps in Automotive Industry
A large German/American producer of auto parts uses high-pressure pumps to deburr machined parts as a part of its production and quality check process. They decided to monitor these pumps to make sure they work properly and that they can see any indications leading to a potential failure before it affects their process.