Kiabi growth story underpinned by Manhattan’s supply chain solutions
Company Size
1,000+
Region
- Europe
Country
- China
- France
- Italy
- Russia
- Spain
Product
- Manhattan Warehouse Management
- RF equipment Motorola
- Conveyor (Savoye)
- Put-to-Light (L4Logistics)
Tech Stack
- Warehouse Management System
- RF equipment
- Conveyor Systems
- Put-to-Light Systems
Implementation Scale
- Enterprise-wide Deployment
Impact Metrics
- Cost Savings
- Customer Satisfaction
- Digital Expertise
- Productivity Improvements
Technology Category
- Automation & Control - Automation & Process Control Systems
- Functional Applications - Warehouse Management Systems (WMS)
- Networks & Connectivity - RF Transceivers
Applicable Industries
- Apparel
- Retail
Applicable Functions
- Logistics & Transportation
- Warehouse & Inventory Management
Use Cases
- Inventory Management
- Process Control & Optimization
- Supply Chain Visibility
- Warehouse Automation
Services
- Software Design & Engineering Services
- System Integration
- Testing & Certification
About The Customer
Kiabi is one of France’s leading, value-clothing fashion retailers, offering an extensive range of womenswear, menswear, childrenswear and baby clothing. The company employs 6,000 staff and fulfils more than 40,000 store orders each year. These orders amount to 100 million individual items and are bought by customers in Kiabi’s 188 stores in France, 42 stores in Spain, 6 stores in Italy, and its first stores in China and Russia. The company also sells goods through its website at www.kiabi.com.
The Challenge
Following a review of the business several years ago, Kiabi’s management team determined that the company’s supply chain systems infrastructure would not be robust enough to support the future expansion of the business. Kiabi’s proprietary warehouse management system had reached its limit in terms of throughput capacity, optimisation potential and flexibility. Picking waves could not be modified once they were underway, and the system did not offer the required flexibility for customs clearance. Kiabi reviewed the solutions available on the market with a view to helping the rapidly growing company achieve the following goals: Cost reduction and logistics performance improvement, Reduction in order-to-delivery cycle time, Support for Kiabi’s global expansion plans, Centralised execution and better control over the fulfilment of store orders, Optimisation of operational processes, Reliability and scalability of supply chain execution system.
The Solution
Kiabi selected Manhattan’s Warehouse Management solution because it offered a wide and deep functionality that required few custom enhancements. In addition, its technical architecture was consistent with Kiabi’s standards and the company’s broad experience in the fashion industry enabled it to understand Kiabi’s challenges quickly. The multi-site solution roll-out began with the Mâcon warehouse in South-East France. Following completion of the design phase, the Kiabi and Manhattan teams integrated Warehouse Management with the company’s internally developed sales system. As Kiabi’s activities are based on seasons and include a very large number of products, the company conducted a rigorous scenario testing phase before going live. Based on the Mâcon implementation, the Kiabi and Manhattan teams designed a deployment replication model to facilitate installations at other sites. Subsequently, Kiabi implemented Warehouse Management at the Villeneuve d’Ascq warehouse in Northern France. As the Villeneuve d’Ascq facility runs exactly like the Mâcon site, the same level of ‘stress’ testing was not required and this second site went ‘live’ successfully in under a month. Kiabi then deployed the Manhattan solution in Dourges in Northern France and Madrid. The replication model enabled Kiabi to implement the solution in just 10 days at these sites.
Operational Impact
Quantitative Benefit
Case Study missing?
Start adding your own!
Register with your work email and create a new case study profile for your business.
Related Case Studies.
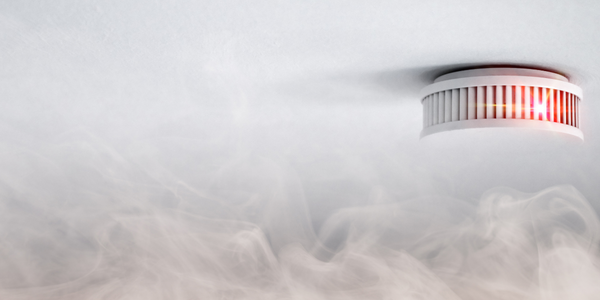
Case Study
Fire Alarm System and Remote Monitoring Sytem
Fire alarm systems are essential in providing an early warning in the event of fire. They help to save lives and protect property whilst also fulfilling the needs of insurance companies and government departments.Fire alarm systems typically consist of several inter-linked components, such as smoke detectors, heat detector, carbon monoxide, manual call points, sounders, alarm and buzzer. The fire alarm system should give immediate information in order to prevent the fire spread and protect live and property.To get maximum protection a shoe manufacturer in Indonesia opted for a new fire alarm system to monitor 13 production sites spread over 160 hectars. Although the company had an existing fire alarm system, it could not be monitored remotely.It was essential that the new system would be able to be monitored from a central control room. It needed to be able to connect to the existing smoke detector and manual call point. Information should be easily collected and passed on to the Supervisory Control and Data Acquisition (SCADA) system. Furthermore, the system should have several features such as alarm management, auto reporting, being connected to many client computers without additional cost, and run 24/7 without fails. The company also needed a system which could be implemented without changing the architecture of the existing fire alarm system.
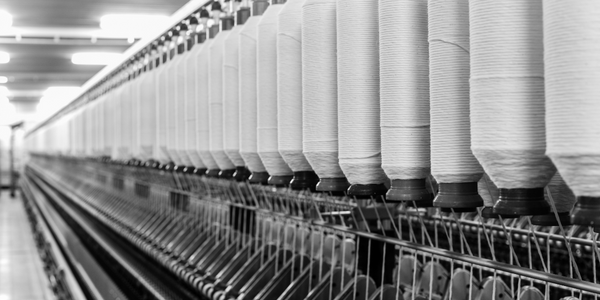
Case Study
IoT Applications and Upgrades in Textile Plant
At any given time, the textile company’s manufacturing facility has up to 2,000 textile carts in use. These carts are pushed from room to room, carrying materials or semi-finished products. Previously, a paper with a hand-written description was attached to each cart. This traditional method of processing made product tracking extremely difficult. Additionally, making sure that every cart of materials or semi-finished products went to its correct processing work station was also a problem. Therefore, the company desired an intelligent solution for tracking assets at their factories. They also wanted a solution that would help them collect process data so they could improve their manufacturing efficiency.
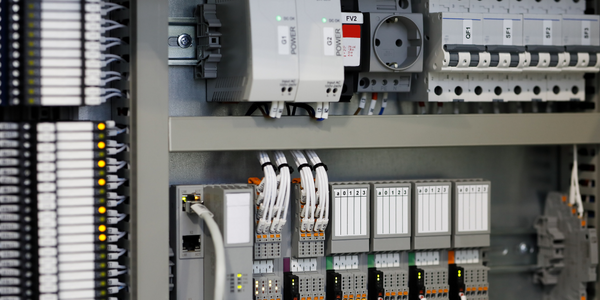
Case Study
Improving Production Line Efficiency with Ethernet Micro RTU Controller
Moxa was asked to provide a connectivity solution for one of the world's leading cosmetics companies. This multinational corporation, with retail presence in 130 countries, 23 global braches, and over 66,000 employees, sought to improve the efficiency of their production process by migrating from manual monitoring to an automatic productivity monitoring system. The production line was being monitored by ABB Real-TPI, a factory information system that offers data collection and analysis to improve plant efficiency. Due to software limitations, the customer needed an OPC server and a corresponding I/O solution to collect data from additional sensor devices for the Real-TPI system. The goal is to enable the factory information system to more thoroughly collect data from every corner of the production line. This will improve its ability to measure Overall Equipment Effectiveness (OEE) and translate into increased production efficiencies. System Requirements • Instant status updates while still consuming minimal bandwidth to relieve strain on limited factory networks • Interoperable with ABB Real-TPI • Small form factor appropriate for deployment where space is scarce • Remote software management and configuration to simplify operations
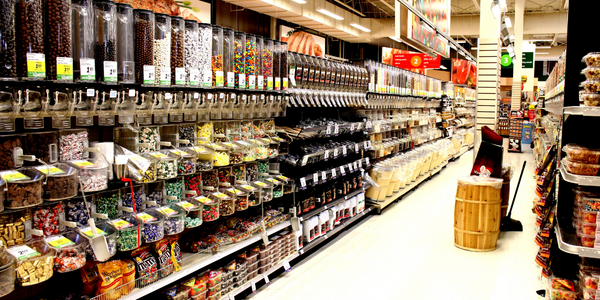
Case Study
How Sirqul’s IoT Platform is Crafting Carrefour’s New In-Store Experiences
Carrefour Taiwan’s goal is to be completely digital by end of 2018. Out-dated manual methods for analysis and assumptions limited Carrefour’s ability to change the customer experience and were void of real-time decision-making capabilities. Rather than relying solely on sales data, assumptions, and disparate systems, Carrefour Taiwan’s CEO led an initiative to find a connected IoT solution that could give the team the ability to make real-time changes and more informed decisions. Prior to implementing, Carrefour struggled to address their conversion rates and did not have the proper insights into the customer decision-making process nor how to make an immediate impact without losing customer confidence.
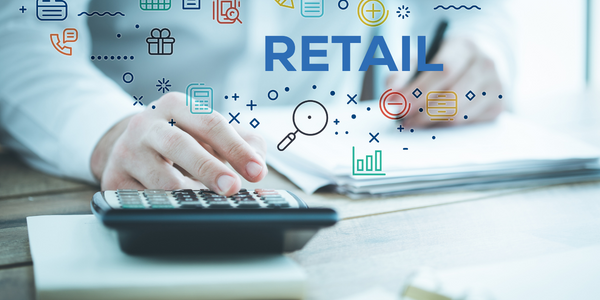
Case Study
Digital Retail Security Solutions
Sennco wanted to help its retail customers increase sales and profits by developing an innovative alarm system as opposed to conventional connected alarms that are permanently tethered to display products. These traditional security systems were cumbersome and intrusive to the customer shopping experience. Additionally, they provided no useful data or analytics.