Company Size
1,000+
Region
- America
Country
- Chile
Product
- Blue Yonder's warehouse management capabilities
Tech Stack
- Inventory Management System
Implementation Scale
- Enterprise-wide Deployment
Impact Metrics
- Customer Satisfaction
- Productivity Improvements
Technology Category
- Functional Applications - Warehouse Management Systems (WMS)
Applicable Industries
- Food & Beverage
Applicable Functions
- Warehouse & Inventory Management
Use Cases
- Inventory Management
Services
- Training
About The Customer
Ariztía is the second largest chicken and poultry producer in Chile. Founded in 1894, the company has grown significantly over the years. Ariztía's mission and vision is to provide quality products and excellent service to their customers. Their products, which have short shelf lives, are shipped either fresh or frozen to customers. The company places a high value on training and education, believing it to be a key factor in improving employee productivity.
The Challenge
Ariztía, the second largest chicken and poultry producer in Chile, was facing challenges in managing its short shelf life products. The company's products, which are shipped either fresh or frozen to customers, required tight inventory control to assure freshness. This was of paramount importance to Ariztía as it directly impacted their mission to provide quality products and excellent service to their customers. The company also strongly believed in the value of training and education to improve employee productivity. However, assuring freshness mandated strict adherence to first expired/first out inventory turnover practices, which was proving to be a challenge.
The Solution
Ariztía turned to Blue Yonder for a solution to their inventory management challenges. Blue Yonder's warehouse management capabilities enabled Ariztía to better manage their short shelf life inventory and more accurately match inventory practices to customer requirements. This resulted in greater customer satisfaction with reduced inventory losses. The solution also improved control over inventory, which in turn increased employee productivity and company profitability. In addition to the warehouse management solution, Blue Yonder also provided training to Ariztía, further enhancing their belief in the value of training and education for improving productivity.
Operational Impact
Case Study missing?
Start adding your own!
Register with your work email and create a new case study profile for your business.
Related Case Studies.

Case Study
The Kellogg Company
Kellogg keeps a close eye on its trade spend, analyzing large volumes of data and running complex simulations to predict which promotional activities will be the most effective. Kellogg needed to decrease the trade spend but its traditional relational database on premises could not keep up with the pace of demand.

Case Study
HEINEKEN Uses the Cloud to Reach 10.5 Million Consumers
For 2012 campaign, the Bond promotion, it planned to launch the campaign at the same time everywhere on the planet. That created unprecedented challenges for HEINEKEN—nowhere more so than in its technology operation. The primary digital content for the campaign was a 100-megabyte movie that had to play flawlessly for millions of viewers worldwide. After all, Bond never fails. No one was going to tolerate a technology failure that might bruise his brand.Previously, HEINEKEN had supported digital media at its outsourced datacenter. But that datacenter lacked the computing resources HEINEKEN needed, and building them—especially to support peak traffic that would total millions of simultaneous hits—would have been both time-consuming and expensive. Nor would it have provided the geographic reach that HEINEKEN needed to minimize latency worldwide.

Case Study
Energy Management System at Sugar Industry
The company wanted to use the information from the system to claim under the renewable energy certificate scheme. The benefit to the company under the renewable energy certificates is Rs 75 million a year. To enable the above, an end-to-end solution for load monitoring, consumption monitoring, online data monitoring, automatic meter data acquisition which can be exported to SAP and other applications is required.

Case Study
Coca Cola Swaziland Conco Case Study
Coco Cola Swaziland, South Africa would like to find a solution that would enable the following results: - Reduce energy consumption by 20% in one year. - Formulate a series of strategic initiatives that would enlist the commitment of corporate management and create employee awareness while helping meet departmental targets and investing in tools that assist with energy management. - Formulate a series of tactical initiatives that would optimize energy usage on the shop floor. These would include charging forklifts and running cold rooms only during off-peak periods, running the dust extractors only during working hours and basing lights and air-conditioning on someone’s presence. - Increase visibility into the factory and other processes. - Enable limited, non-intrusive control functions for certain processes.

Case Study
Temperature Monitoring for Restaurant Food Storage
When it came to implementing a solution, Mr. Nesbitt had an idea of what functionality that he wanted. Although not mandated by Health Canada, Mr. Nesbitt wanted to ensure quality control issues met the highest possible standards as part of his commitment to top-of-class food services. This wish list included an easy-to use temperature-monitoring system that could provide a visible display of the temperatures of all of his refrigerators and freezers, including historical information so that he could review the performance of his equipment. It also had to provide alert notification (but email alerts and SMS text message alerts) to alert key staff in the event that a cooling system was exceeding pre-set warning limits.
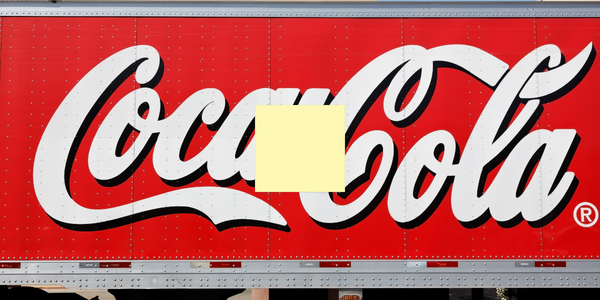
Case Study
Coca-Cola Refreshments, U.S.
Coca-Cola Refreshments owns and manages Coca-Cola branded refrigerators in retail establishments. Legacy systems were used to locate equipment information by logging onto multiple servers which took up to 8 hours to update information on 30-40 units. The company had no overall visibility into equipment status or maintenance history.