JTAPE Unlocks the Power of Accurate Inventory
Customer Company Size
SME
Country
- United Kingdom
Product
- RF-SMART
- NetSuite
Tech Stack
- Barcode Scanning
- Label Printing
Implementation Scale
- Enterprise-wide Deployment
Impact Metrics
- Productivity Improvements
- Customer Satisfaction
- Waste Reduction
Technology Category
- Functional Applications - Inventory Management Systems
- Functional Applications - Warehouse Management Systems (WMS)
Applicable Industries
- Automotive
- Aerospace
- Marine & Shipping
Applicable Functions
- Warehouse & Inventory Management
- Business Operation
Use Cases
- Inventory Management
- Warehouse Automation
- Predictive Replenishment
Services
- System Integration
- Training
About The Customer
Established in 2003, JTAPE manufactures specialist masking and detailing tape products for the automotive aftermarket. The company ships globally to manufacturers, body shops, and distributors, with their products being used by automobile repair companies, aerospace, and marine industries. As a long-time NetSuite customer, JTAPE recognized the need for better inventory control to support their growing operations. With leadership fully backing technology investments, JTAPE sought to implement a solution that would streamline their inventory management and improve overall efficiency.
The Challenge
JTAPE, a manufacturer of specialist masking and detailing tape products, faced challenges in managing their inventory effectively. The company needed a structured system to keep their inventory stock accurate and operations efficient. Manual cycle counts and incorrect inventory management were leading to inefficiencies and potential stockouts, which could disrupt their production process.
The Solution
JTAPE implemented RF-SMART, a solution with native integration to NetSuite, to gain better control over their inventory. The implementation was quick and seamless, allowing the team to start using the system immediately. JTAPE focused on their assembly build process, implementing label printing as part of their receipt process to ensure all stock was labeled right away. This provided control from the beginning and allowed for real-time inventory management. RF-SMART enabled JTAPE to complete purchase order receiving, assembly picks and builds, and regular cycle counts, replacing the need for annual counts. The system also provided greater visibility into inventory, reducing the need to manage for worst-case scenarios and ensuring timely replenishment and reduced wastage.
Operational Impact
Quantitative Benefit
Case Study missing?
Start adding your own!
Register with your work email and create a new case study profile for your business.
Related Case Studies.
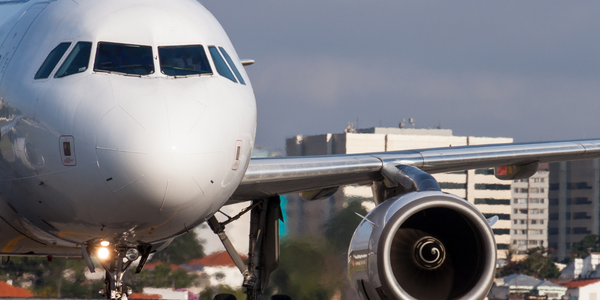
Case Study
Airbus Soars with Wearable Technology
Building an Airbus aircraft involves complex manufacturing processes consisting of thousands of moving parts. Speed and accuracy are critical to business and competitive advantage. Improvements in both would have high impact on Airbus’ bottom line. Airbus wanted to help operators reduce the complexity of assembling cabin seats and decrease the time required to complete this task.
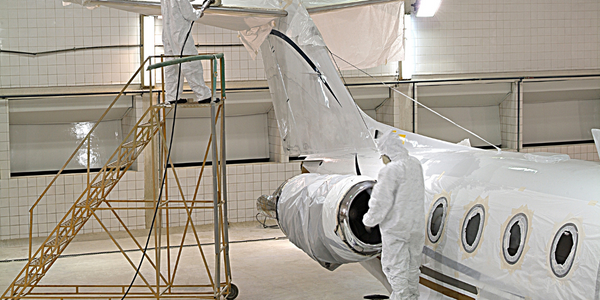
Case Study
Aircraft Predictive Maintenance and Workflow Optimization
First, aircraft manufacturer have trouble monitoring the health of aircraft systems with health prognostics and deliver predictive maintenance insights. Second, aircraft manufacturer wants a solution that can provide an in-context advisory and align job assignments to match technician experience and expertise.
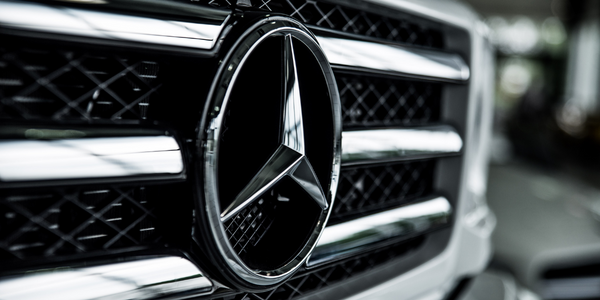
Case Study
Integral Plant Maintenance
Mercedes-Benz and his partner GAZ chose Siemens to be its maintenance partner at a new engine plant in Yaroslavl, Russia. The new plant offers a capacity to manufacture diesel engines for the Russian market, for locally produced Sprinter Classic. In addition to engines for the local market, the Yaroslavl plant will also produce spare parts. Mercedes-Benz Russia and his partner needed a service partner in order to ensure the operation of these lines in a maintenance partnership arrangement. The challenges included coordinating the entire maintenance management operation, in particular inspections, corrective and predictive maintenance activities, and the optimizing spare parts management. Siemens developed a customized maintenance solution that includes all electronic and mechanical maintenance activities (Integral Plant Maintenance).
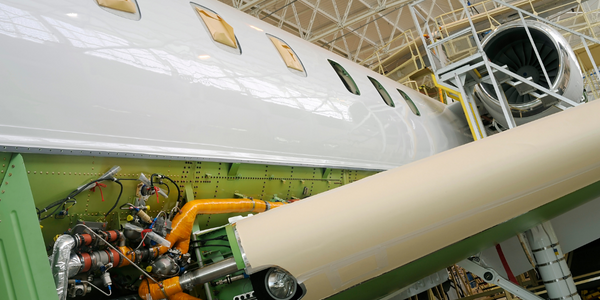
Case Study
Aerospace & Defense Case Study Airbus
For the development of its new wide-body aircraft, Airbus needed to ensure quality and consistency across all internal and external stakeholders. Airbus had many challenges including a very aggressive development schedule and the need to ramp up production quickly to satisfy their delivery commitments. The lack of communication extended design time and introduced errors that drove up costs.