Iwarehouse® Protecting All Assets
Customer Company Size
Large Corporate
Region
- America
Country
- Canada
Product
- iWAREHOUSE®
- Raymond® trucks
Tech Stack
- Telematics System
Implementation Scale
- Enterprise-wide Deployment
Impact Metrics
- Cost Savings
- Productivity Improvements
- Employee Satisfaction
Technology Category
- Functional Applications - Fleet Management Systems (FMS)
- Analytics & Modeling - Predictive Analytics
Applicable Industries
- Retail
Applicable Functions
- Warehouse & Inventory Management
- Maintenance
Use Cases
- Fleet Management
- Predictive Maintenance
- Warehouse Automation
Services
- System Integration
- Training
About The Customer
The Nova Scotia Liquor Corporation (NSLC) story begins in the late 1920s — when Nova Scotians voted in favor of retailing beverage alcohol. This movement paved the way for the establishment of the Nova Scotia Liquor Commission on May 1, 1930. In 2001, the NSLC changed from a commission to a Canadian Crown corporation. Today, 106 retail stores and 60 agencies across the province, generating more than one half billion dollars annually. Stores continue to evolve as new concepts for layout, customer service and merchandising are brought forward. The retailer uses exclusively Raymond® trucks in its warehouse and works closely with G.N. Johnston, a Raymond Sales and Service Center, to optimize its facility.
The Challenge
The NSLC is especially proactive in protecting its biggest asset — its people. The NSLC encourages all employees to take personal responsibility for themselves and the equipment they use to do their jobs. But managers needed better insight into the daily activities of the operators to be able to support this, along with more information that would allow them to make general warehouse decisions and improvements.
The Solution
The NSLC selected iWAREHOUSE®, a telematics system that can be installed into every lift truck in a warehouse. The NSLC used the system to help manage its more than 40 trucks. The system allows managers to collect and report on operational and maintenance data for their industrial vehicle fleets and operators. Alerts related to improperly performing equipment or equipment that has sustained damage intrigued the NSLC, while features like customizable startup speeds and records of service history aiding in reporting sold them on the solution. As an added bonus, the NSLC found that iWAREHOUSE helped managers keep track of operator certifications and helped ensure they were up-to-date on training.
Operational Impact
Quantitative Benefit
Case Study missing?
Start adding your own!
Register with your work email and create a new case study profile for your business.
Related Case Studies.
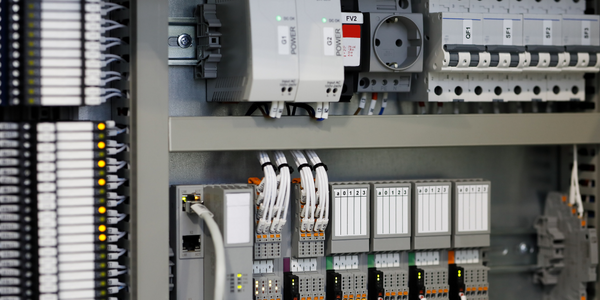
Case Study
Improving Production Line Efficiency with Ethernet Micro RTU Controller
Moxa was asked to provide a connectivity solution for one of the world's leading cosmetics companies. This multinational corporation, with retail presence in 130 countries, 23 global braches, and over 66,000 employees, sought to improve the efficiency of their production process by migrating from manual monitoring to an automatic productivity monitoring system. The production line was being monitored by ABB Real-TPI, a factory information system that offers data collection and analysis to improve plant efficiency. Due to software limitations, the customer needed an OPC server and a corresponding I/O solution to collect data from additional sensor devices for the Real-TPI system. The goal is to enable the factory information system to more thoroughly collect data from every corner of the production line. This will improve its ability to measure Overall Equipment Effectiveness (OEE) and translate into increased production efficiencies. System Requirements • Instant status updates while still consuming minimal bandwidth to relieve strain on limited factory networks • Interoperable with ABB Real-TPI • Small form factor appropriate for deployment where space is scarce • Remote software management and configuration to simplify operations
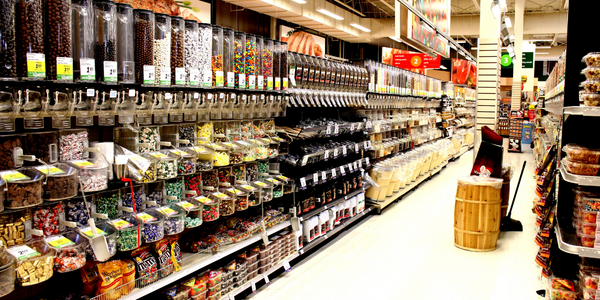
Case Study
How Sirqul’s IoT Platform is Crafting Carrefour’s New In-Store Experiences
Carrefour Taiwan’s goal is to be completely digital by end of 2018. Out-dated manual methods for analysis and assumptions limited Carrefour’s ability to change the customer experience and were void of real-time decision-making capabilities. Rather than relying solely on sales data, assumptions, and disparate systems, Carrefour Taiwan’s CEO led an initiative to find a connected IoT solution that could give the team the ability to make real-time changes and more informed decisions. Prior to implementing, Carrefour struggled to address their conversion rates and did not have the proper insights into the customer decision-making process nor how to make an immediate impact without losing customer confidence.
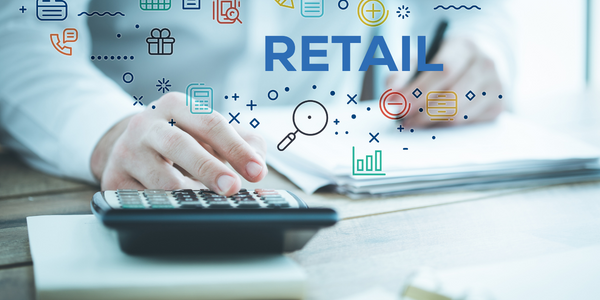
Case Study
Digital Retail Security Solutions
Sennco wanted to help its retail customers increase sales and profits by developing an innovative alarm system as opposed to conventional connected alarms that are permanently tethered to display products. These traditional security systems were cumbersome and intrusive to the customer shopping experience. Additionally, they provided no useful data or analytics.
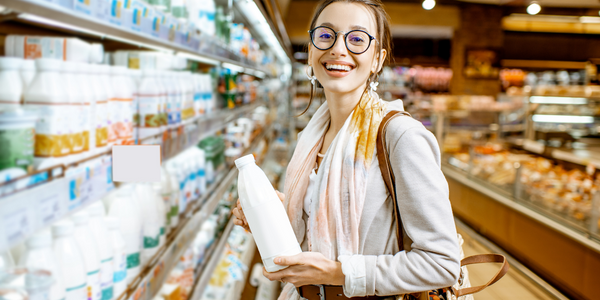
Case Study
Ensures Cold Milk in Your Supermarket
As of 2014, AK-Centralen has over 1,500 Danish supermarkets equipped, and utilizes 16 operators, and is open 24 hours a day, 365 days a year. AK-Centralen needed the ability to monitor the cooling alarms from around the country, 24 hours a day, 365 days a year. Each and every time the door to a milk cooler or a freezer does not close properly, an alarm goes off on a computer screen in a control building in southwestern Odense. This type of alarm will go off approximately 140,000 times per year, equating to roughly 400 alarms in a 24-hour period. Should an alarm go off, then there is only a limited amount of time to act before dairy products or frozen pizza must be disposed of, and this type of waste can quickly start to cost a supermarket a great deal of money.
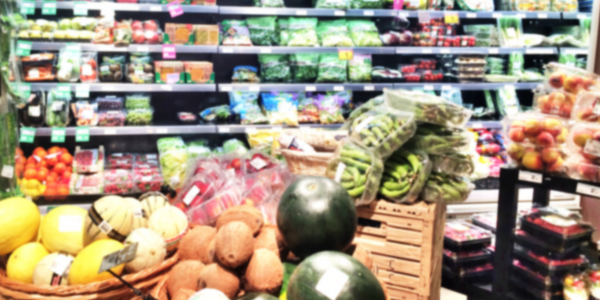
Case Study
Supermarket Energy Savings
The client had previously deployed a one-meter-per-store monitoring program. Given the manner in which energy consumption changes with external temperature, hour of the day, day of week and month of year, a single meter solution lacked the ability to detect the difference between a true problem and a changing store environment. Most importantly, a single meter solution could never identify root cause of energy consumption changes. This approach never reduced the number of truck-rolls or man-hours required to find and resolve issues.