Isuzu Motors unit in Turkey acquires SoftExpert solution to boost operational efficiency
Customer Company Size
Large Corporate
Region
- Europe
Country
- Turkey
Product
- SoftExpert Excellence Suite
Tech Stack
- Analytics
- Process Management
- Document Management
- Workflow Management
Implementation Scale
- Departmental Deployment
Impact Metrics
- Productivity Improvements
- Customer Satisfaction
- Digital Expertise
Technology Category
- Analytics & Modeling - Real Time Analytics
- Application Infrastructure & Middleware - Data Exchange & Integration
- Functional Applications - Enterprise Resource Planning Systems (ERP)
Applicable Industries
- Automotive
Applicable Functions
- Business Operation
- Quality Assurance
Use Cases
- Process Control & Optimization
Services
- System Integration
- Training
About The Customer
Isuzu Motors, one of the biggest players in the world in the auto industry, has more than 37,000 employees worldwide. In the last fiscal year, the company sold more than 648,000 vehicles, generating revenue of over US$ 19 billion. Today, Isuzu is one of the largest producers of auto parts and diesel engines, operating in the manufacture, sale, and provision of services for automotive vehicles powered by internal combustion engines.
The Challenge
The company currently manufactures about 60 different types of diesel engines for industrial applications, in addition to equipping vehicles with capacities ranging from 1,000cc to 30,000cc, including pickups, trucks and heavy tractors. Isuzu currently has an annual production of 16 million units. The company's processes were not controlled in a standardized manner, making it difficult to manage responsibilities, meet deadlines and assess results. In this context, the Company began looking for a tool to improve operational efficiency, aimed at improving workflow, document and KPI management.
The Solution
The SoftExpert Excellence Suite implementation process began in the Quality Control sector. A number of processes have already been centrally controlled, which has given the company greater agility. The Analytics, Process, Form, Performance, Document, Indicator and Workflow components work together in an integrated manner and show the progress of activities in real time. The project was executed at the Turkish unit and was led by Süreç Yönetim Merkezi, a SoftExpert business partner.
Operational Impact
Quantitative Benefit
Case Study missing?
Start adding your own!
Register with your work email and create a new case study profile for your business.
Related Case Studies.
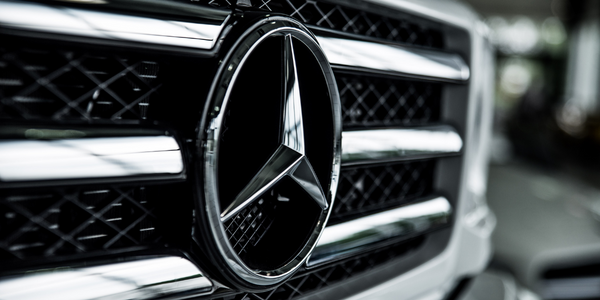
Case Study
Integral Plant Maintenance
Mercedes-Benz and his partner GAZ chose Siemens to be its maintenance partner at a new engine plant in Yaroslavl, Russia. The new plant offers a capacity to manufacture diesel engines for the Russian market, for locally produced Sprinter Classic. In addition to engines for the local market, the Yaroslavl plant will also produce spare parts. Mercedes-Benz Russia and his partner needed a service partner in order to ensure the operation of these lines in a maintenance partnership arrangement. The challenges included coordinating the entire maintenance management operation, in particular inspections, corrective and predictive maintenance activities, and the optimizing spare parts management. Siemens developed a customized maintenance solution that includes all electronic and mechanical maintenance activities (Integral Plant Maintenance).
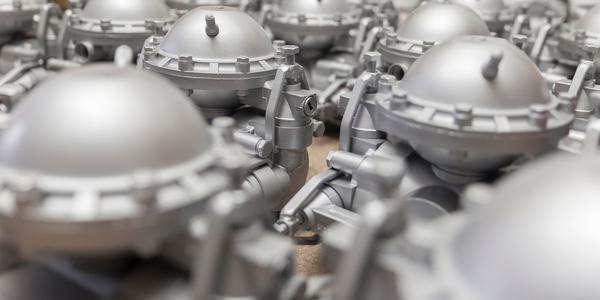
Case Study
Monitoring of Pressure Pumps in Automotive Industry
A large German/American producer of auto parts uses high-pressure pumps to deburr machined parts as a part of its production and quality check process. They decided to monitor these pumps to make sure they work properly and that they can see any indications leading to a potential failure before it affects their process.