Technology Category
- Analytics & Modeling - Digital Twin / Simulation
- Robots - Autonomous Guided Vehicles (AGV)
Applicable Industries
- Automotive
- Packaging
Applicable Functions
- Product Research & Development
Use Cases
- Structural Health Monitoring
- Vehicle Performance Monitoring
Services
- Training
About The Customer
The Deep Orange Program of the Clemson University International Center for Automotive Research (CUICAR) is a graduate automotive engineering program that immerses students into the working environment of the automotive OEM and supplier. Students, multi-disciplinary faculty, and participating partners focus on designing and fabricating a new vehicle prototype over a period of two years. Each project focuses on applying innovative design processes and tools to vehicle development and integrating the resulting design with breakthrough product components. This provides the automotive students with hands-on experience in vehicle design, engineering, and prototyping. The Deep Orange Program is part of the larger CUICAR strategic focus of conducting interdisciplinary research that addresses industry and societal challenges related to the adoption of advanced automotive design technologies and product innovation.
The Challenge
The Deep Orange Program of the Clemson University International Center for Automotive Research (CUICAR) was tasked with designing a six-seat sports car using innovative sheet-folding technology. The goal was to develop a vehicle based on the architecture of a mainstream hybrid concept marketed toward Generation Y. The design had to accommodate four 95th percentile male occupants in the outboard seats and two 50th percentile male occupants on the middle seats using a 2-row, 3+3 seating configuration. The body-in-white (BIW) structural design concept was chosen to explore the Industrial Origami® patented technology that enables the folding of lighter gauge material into complex shapes for the body structural members. The forming is completed with simple, low-cost fixtures, at the assembly location. The challenge was to balance design requirements for BIW stiffness, packaging space, cost, and weight.
The Solution
The Deep Orange Program partnered with Altair to apply advanced computational simulation methods to their vehicle designs. Altair-sponsored internships and fellowships enhanced student learning through providing webinar-based and on-sight instruction of Altair HyperWorks simulation technologies. A CAD model for the BIW design was built using SolidWorks and was imported into HyperMesh. All of the sheet-folding technology structural parts and tubular space frame components were modeled using 2D shell elements. Thicker-gauge BIW components, representing crucial design areas where the front subframe mounts to the body structure were meshed with 3D hexagonal elements. A series of in-depth finite element analyses covering torsional and bending stiffness, natural frequency, and dynamic pot-hole and bump loads were completed using the Altair OptiStruct finite-element solver. The finite element results, reviewed by applying the Altair HyperView post-processing module, showed that the BIW design met all the program requirements for body stiffness.
Operational Impact
Quantitative Benefit
Case Study missing?
Start adding your own!
Register with your work email and create a new case study profile for your business.
Related Case Studies.
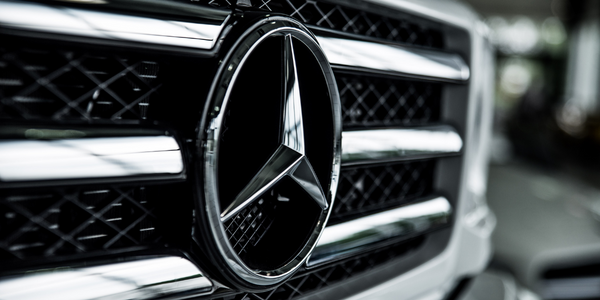
Case Study
Integral Plant Maintenance
Mercedes-Benz and his partner GAZ chose Siemens to be its maintenance partner at a new engine plant in Yaroslavl, Russia. The new plant offers a capacity to manufacture diesel engines for the Russian market, for locally produced Sprinter Classic. In addition to engines for the local market, the Yaroslavl plant will also produce spare parts. Mercedes-Benz Russia and his partner needed a service partner in order to ensure the operation of these lines in a maintenance partnership arrangement. The challenges included coordinating the entire maintenance management operation, in particular inspections, corrective and predictive maintenance activities, and the optimizing spare parts management. Siemens developed a customized maintenance solution that includes all electronic and mechanical maintenance activities (Integral Plant Maintenance).
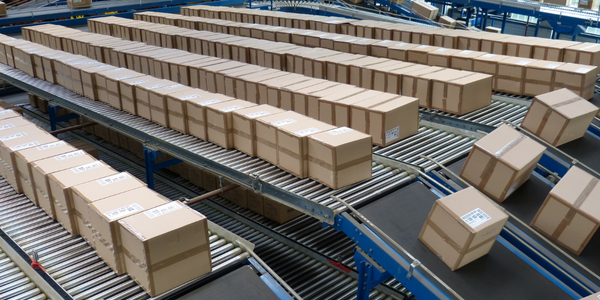
Case Study
IoT Data Analytics Case Study - Packaging Films Manufacturer
The company manufactures packaging films on made to order or configure to order basis. Every order has a different set of requirements from the product characteristics perspective and hence requires machine’s settings to be adjusted accordingly. If the film quality does not meet the required standards, the degraded quality impacts customer delivery causes customer dissatisfaction and results in lower margins. The biggest challenge was to identify the real root cause and devise a remedy for that.
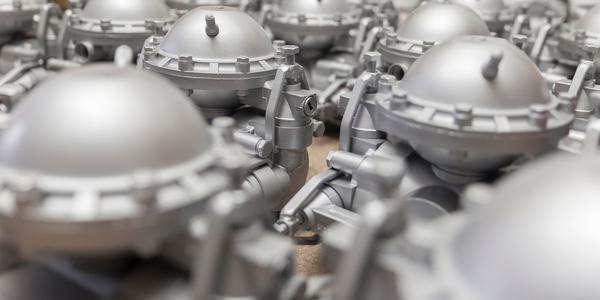
Case Study
Monitoring of Pressure Pumps in Automotive Industry
A large German/American producer of auto parts uses high-pressure pumps to deburr machined parts as a part of its production and quality check process. They decided to monitor these pumps to make sure they work properly and that they can see any indications leading to a potential failure before it affects their process.