Industrial Products Company Improves On-time Delivery and Reduces Inventory
Customer Company Size
Large Corporate
Region
- America
Country
- United States
Product
- Hertzler System
Tech Stack
- Data Capture
- Actionable Intelligence
- Legacy Systems Integration
Implementation Scale
- Enterprise-wide Deployment
Impact Metrics
- Cost Savings
- Customer Satisfaction
- Productivity Improvements
Technology Category
- Analytics & Modeling - Predictive Analytics
- Application Infrastructure & Middleware - Data Exchange & Integration
- Functional Applications - Manufacturing Execution Systems (MES)
Use Cases
- Predictive Maintenance
- Process Control & Optimization
- Supply Chain Visibility
Services
- Data Science Services
- System Integration
About The Customer
The customer is an industrial products company facing significant challenges in improving their manufacturing supply chain processes. They are under immense pressure to enhance performance but struggle to obtain actionable insights quickly due to a fragmented data landscape. Their data is scattered across various formats, including spreadsheets, custom applications, paper systems, and disconnected legacy systems. This disjointed data environment makes it difficult for them to react promptly to issues, often leading to delayed responses and dealing with problems only after they have escalated. The company experiences increased work-in-progress (WIP) and extended order-to-cash cycle times due to the need for extensive sort and rework efforts. Unplanned downtime further disrupts their schedule adherence, forcing them to maintain a buffer in finished goods inventory, which drives up costs. Additionally, defects that escape to customers erode trust and confidence in their products.
The Challenge
Pressure to Improve\nIf you’re like our other clients, you’re frustrated. You’re under pressure to improve performance, but you can’t get the insights you need fast enough. One described it like running through a room full of furniture with the lights out: you keep crashing into things but you have to get up and keep moving.\nThis situation is grossly unfair. To drive performance you need to turn on the lights with insights provided by actionable data.\nThe most frustrating thing is that most people are buried in data. But it’s not usable because it’s a hodge-podge patchwork of spreadsheets, custom apps, paper systems, and disconnected legacy systems.\nDriving improvement in this kind of world is really, really hard because you’re always reacting, and you’re always late. You’re reacting because you can’t see problems until they become obvious. And you’re late because it takes too long to get to actionable information. This is not a sustainable way to drive performance improvement.\nDealing with Yesterday’s Problems\nIf you’re reacting and you’re late, you’re dealing with yesterday’s problems.\nExpensive sort and rework efforts must go all the way back to the last good data point. That increases WIP and increases order-to- cash cycle times. Unplanned downtime impacts schedule adherence, and to compensate, many leaders create a buffer in finished goods inventory, driving up costs. And when defects escape to the customer, they damage trust and confidence.
The Solution
Hertzler takes a different approach. Their system captures data immediately across all aspects of the process, improving visibility so processes can be analyzed in more detail. By compiling disparate manufacturing data and turning it into useful, actionable intelligence, Hertzler's clients can triage, prioritize, and address issues faster and more reliably. This approach enables them to diagnose the root cause of problems more quickly and uncover hidden opportunities to increase revenue, grow margins, and improve asset performance. The system's ability to provide real-time data capture and analysis allows for proactive decision-making, reducing the need for reactive measures and minimizing the impact of unplanned downtime. As a result, the company can optimize their manufacturing supply chain processes, leading to significant improvements in on-time delivery, inventory reduction, and cycle time for improvement projects.
Operational Impact
Quantitative Benefit
Case Study missing?
Start adding your own!
Register with your work email and create a new case study profile for your business.
Related Case Studies.

Case Study
Remote Monitoring & Predictive Maintenance App for a Solar Energy System
The maintenance & tracking of various modules was an overhead for the customer due to the huge labor costs involved. Being an advanced solar solutions provider, they wanted to ensure early detection of issues and provide the best-in-class customer experience. Hence they wanted to automate the whole process.

Case Study
Remote Temperature Monitoring of Perishable Goods Saves Money
RMONI was facing temperature monitoring challenges in a cold chain business. A cold chain must be established and maintained to ensure goods have been properly refrigerated during every step of the process, making temperature monitoring a critical business function. Manual registration practice can be very costly, labor intensive and prone to mistakes.
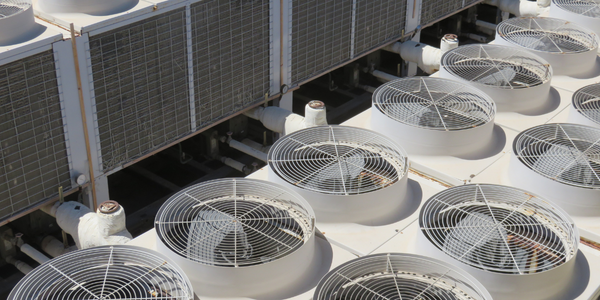
Case Study
Predictive Maintenance for Industrial Chillers
For global leaders in the industrial chiller manufacturing, reliability of the entire production process is of the utmost importance. Chillers are refrigeration systems that produce ice water to provide cooling for a process or industrial application. One of those leaders sought a way to respond to asset performance issues, even before they occur. The intelligence to guarantee maximum reliability of cooling devices is embedded (pre-alarming). A pre-alarming phase means that the cooling device still works, but symptoms may appear, telling manufacturers that a failure is likely to occur in the near future. Chillers who are not internet connected at that moment, provide little insight in this pre-alarming phase.

Case Study
System 800xA at Indian Cement Plants
Chettinad Cement recognized that further efficiencies could be achieved in its cement manufacturing process. It looked to investing in comprehensive operational and control technologies to manage and derive productivity and energy efficiency gains from the assets on Line 2, their second plant in India.
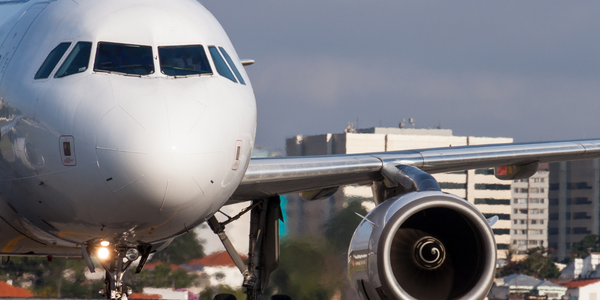
Case Study
Airbus Soars with Wearable Technology
Building an Airbus aircraft involves complex manufacturing processes consisting of thousands of moving parts. Speed and accuracy are critical to business and competitive advantage. Improvements in both would have high impact on Airbus’ bottom line. Airbus wanted to help operators reduce the complexity of assembling cabin seats and decrease the time required to complete this task.