Improving Mold, Tool, and Die Design with SolidWorks Software
Customer Company Size
SME
Region
- America
Country
- United States
Product
- SolidWorks
- MoldWorks
- SplitWorks
- eDrawings
Tech Stack
- SolidWorks
- MoldWorks
- SplitWorks
- eDrawings
Implementation Scale
- Enterprise-wide Deployment
Impact Metrics
- Productivity Improvements
- Cost Savings
- Customer Satisfaction
Technology Category
- Functional Applications - Product Lifecycle Management Systems (PLM)
- Functional Applications - Computerized Maintenance Management Systems (CMMS)
Applicable Industries
- Automotive
Applicable Functions
- Product Research & Development
- Quality Assurance
Use Cases
- Predictive Maintenance
- Manufacturing System Automation
Services
- Software Design & Engineering Services
- System Integration
- Training
About The Customer
Quality Tooling, Inc. designs and builds molds, tools, and dies for some of the world’s leading manufacturers. The company has been in the tooling market for many years and has established a reputation for quality and precision. As the market became more competitive, Quality Tooling sought to enhance its technology to maintain its edge. The company is known for its commitment to innovation and continuous improvement, which drives its efforts to adopt advanced CAD systems and software solutions.
The Challenge
Quality Tooling, Inc. faced increasing competition in the tooling market and needed to increase production and reduce design errors. The company identified that many of their mistakes were related to design changes impacting other components in an assembly. They required a CAD system that could handle diverse types of CAD data more efficiently to improve productivity.
The Solution
Quality Tooling evaluated three parametric CAD systems—SolidWorks, Pro/ENGINEER, and Unigraphics—and chose SolidWorks for its ease of use, value for price, large assembly capabilities, data flexibility, and mold development tools. They implemented SolidWorks software in 2003 and also acquired MoldWorks and SplitWorks from R&B Ltd., which are integrated with SolidWorks. These add-on applications automate important mold development tasks, saving time and money. SolidWorks' interference detection capabilities help identify collisions within tooling assemblies, enhancing the accuracy and efficiency of their designs.
Operational Impact
Quantitative Benefit
Case Study missing?
Start adding your own!
Register with your work email and create a new case study profile for your business.
Related Case Studies.
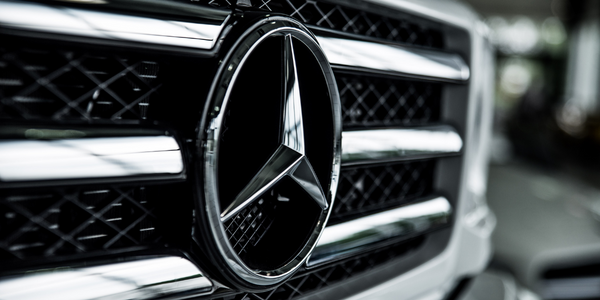
Case Study
Integral Plant Maintenance
Mercedes-Benz and his partner GAZ chose Siemens to be its maintenance partner at a new engine plant in Yaroslavl, Russia. The new plant offers a capacity to manufacture diesel engines for the Russian market, for locally produced Sprinter Classic. In addition to engines for the local market, the Yaroslavl plant will also produce spare parts. Mercedes-Benz Russia and his partner needed a service partner in order to ensure the operation of these lines in a maintenance partnership arrangement. The challenges included coordinating the entire maintenance management operation, in particular inspections, corrective and predictive maintenance activities, and the optimizing spare parts management. Siemens developed a customized maintenance solution that includes all electronic and mechanical maintenance activities (Integral Plant Maintenance).
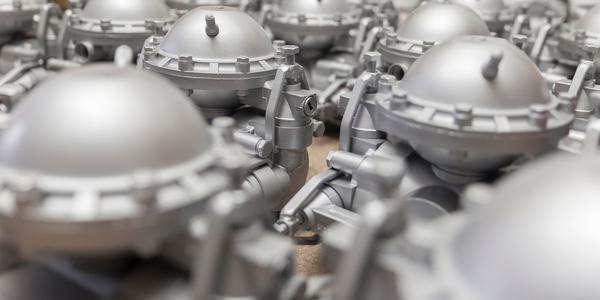
Case Study
Monitoring of Pressure Pumps in Automotive Industry
A large German/American producer of auto parts uses high-pressure pumps to deburr machined parts as a part of its production and quality check process. They decided to monitor these pumps to make sure they work properly and that they can see any indications leading to a potential failure before it affects their process.