Improving automotive die-cast tooling development with SolidWorks Enterprise PDM
Customer Company Size
Large Corporate
Region
- America
Country
- United States
Product
- SolidWorks 3D CAD
- SolidWorks Enterprise PDM
- PDMWorks
Tech Stack
- 3D CAD
- Product Data Management (PDM)
- Workflow Automation
Implementation Scale
- Enterprise-wide Deployment
Impact Metrics
- Productivity Improvements
- Cost Savings
- Customer Satisfaction
Technology Category
- Functional Applications - Product Data Management Systems
- Analytics & Modeling - Predictive Analytics
- Functional Applications - Computerized Maintenance Management Systems (CMMS)
Applicable Industries
- Automotive
Applicable Functions
- Product Research & Development
- Quality Assurance
Use Cases
- Predictive Maintenance
- Digital Twin
- Process Control & Optimization
Services
- System Integration
- Software Design & Engineering Services
About The Customer
Burlington Technologies, Inc. is a world-class tooling manufacturer specializing in high-pressure aluminum die castings used by automotive companies to produce various parts. The company operates through its Centennial division, which continually seeks ways to enhance productivity in the development and machining of die-casting tools. With a focus on innovation and efficiency, Burlington Technologies transitioned to 3D solid modeling in 2006 and sought to implement a robust product data management (PDM) system to streamline their design processes and improve accuracy.
The Challenge
Burlington Technologies, Inc. faced significant challenges in managing design revisions, file confusion, and incorrect data problems while developing high-pressure aluminum die castings for the automotive industry. The transition to 3D solid modeling in 2006 created an opportunity to implement a product data management (PDM) system to control workflow and ensure accurate design revisions. The company needed a solution that could integrate seamlessly with their existing SolidWorks 3D CAD system, automate workflows, and eliminate design errors.
The Solution
Burlington Technologies consulted with Javelin Technologies, their SolidWorks reseller, to evaluate PDM solutions and ultimately implemented SolidWorks Enterprise PDM software. This solution was chosen for its ease of use, full integration with SolidWorks, and cost-effectiveness. The implementation process was swift, with SolidWorks 3D CAD up and running within a month and SolidWorks Enterprise PDM installed within a week. The PDM system provided automated workflows, revision control, and seamless integration with SolidWorks, addressing the company's needs for managing design data and eliminating errors. The system also facilitated workflow automation, ensuring that design documents moved efficiently from one stage to the next, and provided complete traceability of user interactions and revisions.
Operational Impact
Quantitative Benefit
Case Study missing?
Start adding your own!
Register with your work email and create a new case study profile for your business.
Related Case Studies.
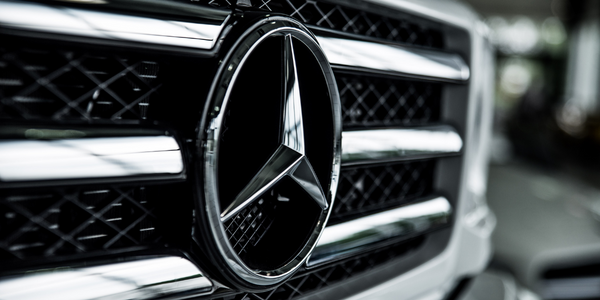
Case Study
Integral Plant Maintenance
Mercedes-Benz and his partner GAZ chose Siemens to be its maintenance partner at a new engine plant in Yaroslavl, Russia. The new plant offers a capacity to manufacture diesel engines for the Russian market, for locally produced Sprinter Classic. In addition to engines for the local market, the Yaroslavl plant will also produce spare parts. Mercedes-Benz Russia and his partner needed a service partner in order to ensure the operation of these lines in a maintenance partnership arrangement. The challenges included coordinating the entire maintenance management operation, in particular inspections, corrective and predictive maintenance activities, and the optimizing spare parts management. Siemens developed a customized maintenance solution that includes all electronic and mechanical maintenance activities (Integral Plant Maintenance).
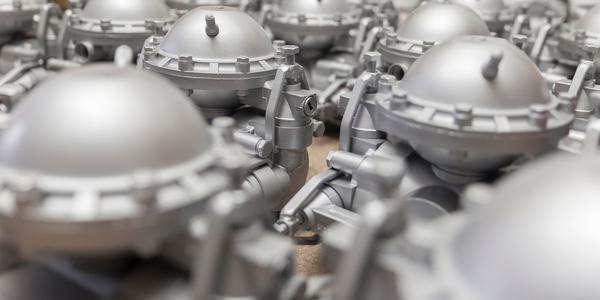
Case Study
Monitoring of Pressure Pumps in Automotive Industry
A large German/American producer of auto parts uses high-pressure pumps to deburr machined parts as a part of its production and quality check process. They decided to monitor these pumps to make sure they work properly and that they can see any indications leading to a potential failure before it affects their process.