Technology Category
- Cybersecurity & Privacy - Identity & Authentication Management
- Sensors - Temperature Sensors
Applicable Industries
- Recycling & Waste Management
Applicable Functions
- Quality Assurance
Use Cases
- Predictive Waste Reduction
- Time Sensitive Networking
Services
- Testing & Certification
- Training
About The Customer
The customer in this case study is the Dover Corporation, a diversified global manufacturer. The company has been implementing continuous improvement and quality management programs around the world, under the guidance of Maneesh Bhatnagar, the Director of Quality & Continuous Improvement. The company has been focusing on creating a work environment that promotes problem-solving, ensuring that employees are always finding ways to improve and deliver more value to customers and the company. The company has been successful in implementing continuous improvement initiatives, creating a culture that recognizes opportunities and implements improvements into the day-to-day operations.
The Challenge
Companies, regardless of their size, often struggle with keeping their employees motivated towards shared goals. The challenge lies in creating a culture where teams are invested in company goals and are constantly working towards streamlining processes. The lack of a problem-solving culture can lead to disengaged employees, inefficient workflows, and increased waste and rework. This can ultimately impact the bottom line, reducing the value delivered to customers. Additionally, many companies have a wealth of processes and information locked in tribal knowledge, which is not transferable and cannot be improved upon. This presents a major risk, as without a standard, there is no benchmark to improve upon.
The Solution
The solution lies in implementing continuous improvement, or Kaizen, a method that promotes a problem-solving culture and respects its people. This involves creating guidelines for eliminating waste and non-value add activities. The first step is to document existing processes and standards, breaking down each process step as much as possible and clearly identifying the actions involved. This sets teams up for success with continuous improvement. The next step is to gather feedback from employees, even those who aren’t familiar with the process, as they can provide fresh perspectives to identify opportunities for improvement. Once teams have decided on a new process, it’s important to communicate with all impacted employees and make necessary modifications to accommodate the improvements. Consistency is paramount in sharing improved processes to prevent them from getting lost in translation.
Operational Impact
Quantitative Benefit
Case Study missing?
Start adding your own!
Register with your work email and create a new case study profile for your business.
Related Case Studies.

Case Study
Water Treatment Energy Management
Water pumping, treatment and conveyance are among the largest energy and cost outlays for many local and regional municipalities. Electricity time-of-use rates and peak pricing tariffs are driving those costs even higher. This case study describes how Monterey Regional Water Pollution Control Agency (MRWPCA) implemented a process data monitoring and control solution in order to analyze and optimize energy use, reduce deployment costs and save operational expenses.
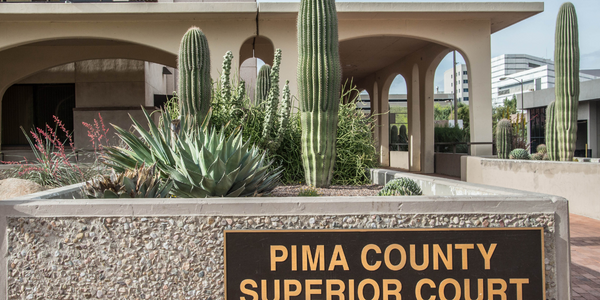
Case Study
Pima County takes significant steps in preserving water source
Pima County is facing the following challenges: - Management of more than 60 million gallons of sewage each day to support the region’s population of more than 1 million people. - To take immediate action when alarms sound alerting operators to issues within the plant The solution should be able to enable the following feature: - To ensure capture of institutional knowledge of current workforce for effective training of future operators - To employ an effective Situational Awareness strategy enabling personnel to effectively understand and address operations of the facility - With assets spread out over more than 700 miles, operational management is difficult
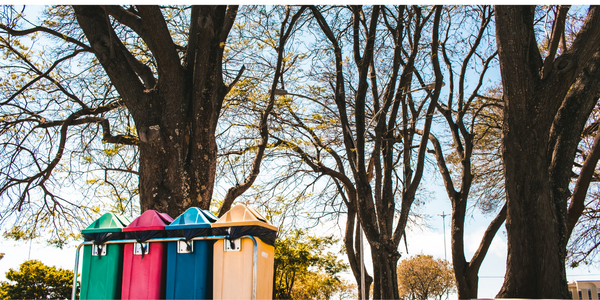
Case Study
A SMART SOLUTION FOR A CIRCULAR ECONOMY
A detailed study conducted by a student from Universidad Pontificia Comillas ICAI in Spain highlighted the need for ecologically safe and sustainable products. While recycling plays an important role in the circular economy, many consumers don’t recycle for a variety of reasons, including lack of space, inconveniently located recycling centers and collection containers, or distrust and/or disbelief in the recycling process. Organizations needed a model that made recycling easier and more accessible for everyone.

Case Study
Conveyor Belt Monitoring
In a smart environment of management, control and industrial automation, one of the key elements to anticipate failures and increase productivity is to be able to monitor the status and use of conveyor belts of any kind of sector, whether it is for logistics or manufacturing.