Customer Company Size
Large Corporate
Country
- Switzerland
Product
- IBM Connections
Implementation Scale
- Enterprise-wide Deployment
Impact Metrics
- Productivity Improvements
- Brand Awareness
Technology Category
- Application Infrastructure & Middleware - API Integration & Management
Applicable Industries
- Chemicals
- Automotive
- Construction & Infrastructure
Applicable Functions
- Sales & Marketing
- Product Research & Development
Use Cases
- Collaborative Robotics
- Remote Collaboration
Services
- Software Design & Engineering Services
About The Customer
Sika AG is a specialty chemicals company with a leading position in the development and production of systems and products for bonding, sealing, damping, reinforcing, and protecting in the building sector and the motor vehicle industry. The company has subsidiaries in 84 countries around the world and manufactures in over 160 factories. Its more than 16,000 employees generate annual sales of CHF5.14 billion. As part of its recent growth strategy, Sika acquired numerous companies, creating challenges in quickly onboarding, integrating, and training people.
The Challenge
Sika AG, a specialty chemicals company, was facing challenges due to its accelerated growth through acquisitions. The company needed to simplify knowledge sharing among new and existing employees across different lines of business. The majority of new employees in 2013 joined the company through acquisitions, creating challenges in quickly onboarding, integrating, and training people. Sika needed a solution to continue further developing a competent, educated staff committed to delivering on the company’s brand promise. The leadership team envisioned a workplace of the future, serving thousands of employees based on one secure, flexible, integrated solution.
The Solution
Sika AG deployed IBM Connections software as part of its Global Enterprise Collaboration (GECO) initiative. The software provides a highly secure social network to help speed staff onboarding, integration, and training. The GECO platform was created with the help of IBM, providing a cost-efficient, scalable solution off the shelf, with no customization requirements. The software was deployed to pull together close to 11,500 employees around the world. The Connections software simplifies collaboration and strengthens personal networks, creating business value. It is also used in areas not originally envisioned, such as globally managing business processes.
Operational Impact
Case Study missing?
Start adding your own!
Register with your work email and create a new case study profile for your business.
Related Case Studies.

Case Study
IoT System for Tunnel Construction
The Zenitaka Corporation ('Zenitaka') has two major business areas: its architectural business focuses on structures such as government buildings, office buildings, and commercial facilities, while its civil engineering business is targeted at structures such as tunnels, bridges and dams. Within these areas, there presented two issues that have always persisted in regard to the construction of mountain tunnels. These issues are 'improving safety" and "reducing energy consumption". Mountain tunnels construction requires a massive amount of electricity. This is because there are many kinds of electrical equipment being used day and night, including construction machinery, construction lighting, and ventilating fan. Despite this, the amount of power consumption is generally not tightly managed. In many cases, the exact amount of power consumption is only ascertained when the bill from the power company becomes available. Sometimes, corporations install demand-monitoring equipment to help curb the maximum power demanded. However, even in these cases, the devices only allow the total volume of power consumption to be ascertained, or they may issue warnings to prevent the contracted volume of power from being exceeded. In order to tackle the issue of reducing power consumption, it was first necessary to obtain an accurate breakdown of how much power was being used in each particular area. In other words, we needed to be able to visualize the amount of power being consumed. Safety, was also not being managed very rigorously. Even now, tunnel construction sites often use a 'name label' system for managing entry into the work site. Specifically, red labels with white reverse sides that bear the workers' names on both sides are displayed at the tunnel work site entrance. The workers themselves then flip the name label to the appropriate side when entering or exiting from the work site to indicate whether or not they are working inside the tunnel at any given time. If a worker forgets to flip his or her name label when entering or exiting from the tunnel, management cannot be performed effectively. In order to tackle the challenges mentioned above, Zenitaka decided to build a system that could improve the safety of tunnel construction as well as reduce the amount of power consumed. In other words, this new system would facilitate a clear picture of which workers were working in each location at the mountain tunnel construction site, as well as which processes were being carried out at those respective locations at any given time. The system would maintain the safety of all workers while also carefully controlling the electrical equipment to reduce unnecessary power consumption. Having decided on the concept, our next concern was whether there existed any kind of robust hardware that would not break down at the construction work site, that could move freely in response to changes in the working environment, and that could accurately detect workers and vehicles using radio frequency identification (RFID). Given that this system would involve many components that were new to Zenitaka, we decided to enlist the cooperation of E.I.Sol Co., Ltd. ('E.I.Sol') as our joint development partner, as they had provided us with a highly practical proposal.
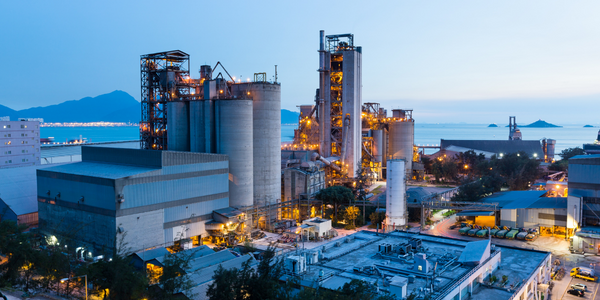
Case Study
Honeywell - Tata Chemicals Improves Data Accessibility with OneWireless
Tata was facing data accessibility challenges in the cement plant control room tapping signals from remote process control areas and other distant locations, including the gas scrubber. Tata needed a wireless solution to extend its control network securely to remote locations that would also provide seamless communication with existing control applications.
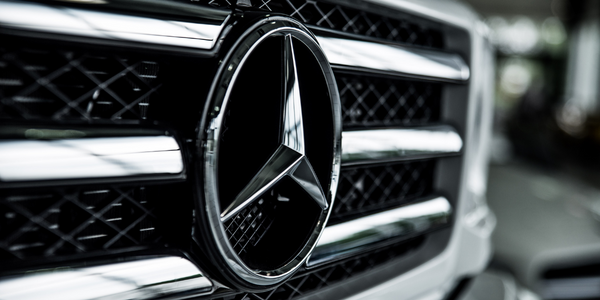
Case Study
Integral Plant Maintenance
Mercedes-Benz and his partner GAZ chose Siemens to be its maintenance partner at a new engine plant in Yaroslavl, Russia. The new plant offers a capacity to manufacture diesel engines for the Russian market, for locally produced Sprinter Classic. In addition to engines for the local market, the Yaroslavl plant will also produce spare parts. Mercedes-Benz Russia and his partner needed a service partner in order to ensure the operation of these lines in a maintenance partnership arrangement. The challenges included coordinating the entire maintenance management operation, in particular inspections, corrective and predictive maintenance activities, and the optimizing spare parts management. Siemens developed a customized maintenance solution that includes all electronic and mechanical maintenance activities (Integral Plant Maintenance).