Customer Company Size
Mid-size Company
Region
- America
Country
- United States
Product
- IBM Kenexa LCMS Premier
Tech Stack
- Learning Content Management System (LCMS)
Implementation Scale
- Enterprise-wide Deployment
Impact Metrics
- Cost Savings
- Productivity Improvements
Technology Category
- Application Infrastructure & Middleware - Data Exchange & Integration
Applicable Industries
- Automotive
Services
- Training
About The Customer
I-CAR, formed in 1979, is a not-for-profit organization dedicated to training the collision repair inter-industry. It is one of the primary suppliers of technical training for the collision repair industry in the United States, Canada, Australia and New Zealand. The organization’s training reaches a broad base of students across each segment of the collision repair industry who must understand the latest methods for efficient, high-quality repair. I-CAR’s vision is that each person in the collision repair industry has the information, knowledge and skills required to perform complete, safe and quality repairs for the ultimate benefit of the consumer. And the organization’s mission is to deliver increasingly accessible, on-demand and relevant education, knowledge, services and solutions for the collision repair inter-industry.
The Challenge
I-CAR, a not-for-profit organization dedicated to training the collision repair inter-industry, was facing challenges in keeping up with the rapidly evolving lightweight vehicle materials and advanced technologies. The organization needed a robust system to deliver its training materials that could reach collision repair professionals in their workplaces. The system also needed to be easily updated at one time regardless of where the information was stored and used. The organization was also looking to enhance its training programs to become increasingly relevant, engaging, accessible and timely.
The Solution
I-CAR implemented IBM Kenexa LCMS Premier, a learning content management system (LCMS), to deliver its training materials. This solution is robust, adaptable and streamlined to help companies reach their business goals. It automates the content lifecycle, making it more effective and cost-efficient. Organizations use LCMS Premier to develop, maintain, manage and deliver personalized training for learners. The quality of the learning content can be improved with an automated workflow and review function, saving valuable time and resources. Using an LCMS also helps enable organizations to quickly find assets, perform analyses of the content and its usage, modify content and update changes to the learning content at one time, making it easier to deliver content when it is needed.
Operational Impact
Quantitative Benefit
Case Study missing?
Start adding your own!
Register with your work email and create a new case study profile for your business.
Related Case Studies.
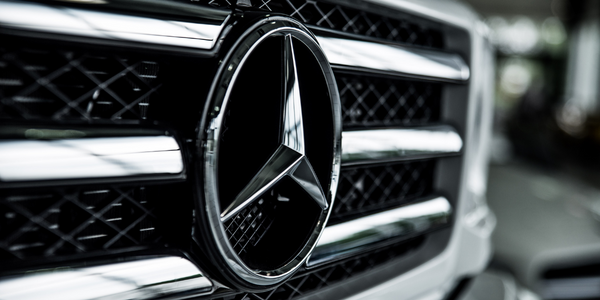
Case Study
Integral Plant Maintenance
Mercedes-Benz and his partner GAZ chose Siemens to be its maintenance partner at a new engine plant in Yaroslavl, Russia. The new plant offers a capacity to manufacture diesel engines for the Russian market, for locally produced Sprinter Classic. In addition to engines for the local market, the Yaroslavl plant will also produce spare parts. Mercedes-Benz Russia and his partner needed a service partner in order to ensure the operation of these lines in a maintenance partnership arrangement. The challenges included coordinating the entire maintenance management operation, in particular inspections, corrective and predictive maintenance activities, and the optimizing spare parts management. Siemens developed a customized maintenance solution that includes all electronic and mechanical maintenance activities (Integral Plant Maintenance).
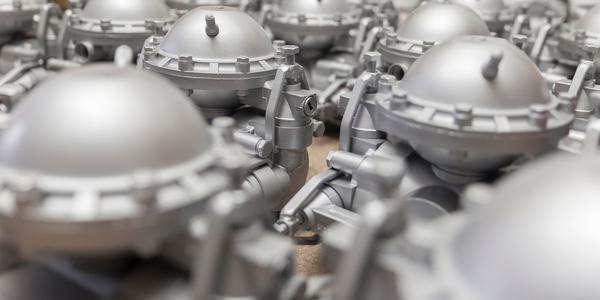
Case Study
Monitoring of Pressure Pumps in Automotive Industry
A large German/American producer of auto parts uses high-pressure pumps to deburr machined parts as a part of its production and quality check process. They decided to monitor these pumps to make sure they work properly and that they can see any indications leading to a potential failure before it affects their process.