Hyundai Motor Company Automates Document Management with SoftExpert ECM
Customer Company Size
Large Corporate
Country
- Brazil
Product
- SoftExpert ECM
Tech Stack
- Enterprise Content Management (ECM)
Implementation Scale
- Enterprise-wide Deployment
Impact Metrics
- Customer Satisfaction
- Digital Expertise
- Productivity Improvements
Technology Category
- Application Infrastructure & Middleware - Data Exchange & Integration
- Functional Applications - Enterprise Resource Planning Systems (ERP)
Applicable Industries
- Automotive
Applicable Functions
- Business Operation
- Quality Assurance
Use Cases
- Regulatory Compliance Monitoring
Services
- Software Design & Engineering Services
- System Integration
About The Customer
Hyundai Motor Company is a global automotive manufacturer with a significant presence worldwide. The company operates eight manufacturing units and seven technical and design centers globally, employing over 110,000 people. In 2017, Hyundai sold 4.5 million vehicles, showcasing its substantial market presence. Hyundai Motor Brasil, a subsidiary of Hyundai, has a production capacity of 180,000 cars per year and employs 2,700 people. The company is known for its commitment to quality and innovation, continuously seeking ways to improve its operations and maintain high standards in its manufacturing processes.
The Challenge
Hyundai Motor Company faced a significant challenge in managing its extensive documentation while ensuring compliance with ISO 9001 standards. The company needed a robust solution to automate document management processes, streamline operations, and maintain high-quality standards. The existing manual processes were time-consuming, prone to errors, and did not meet the stringent requirements of ISO 9001. This situation necessitated a comprehensive solution that could handle the complexity of document management across multiple locations and departments, ensuring consistency and compliance.
The Solution
To address the document management challenge, Hyundai Motor Company implemented SoftExpert ECM, an Enterprise Content Management solution. This solution enabled Hyundai to automate and streamline its document management processes, ensuring compliance with ISO 9001 standards. SoftExpert ECM provided a centralized platform for managing quality documents, facilitating easy access, retrieval, and control. The solution also integrated with Hyundai's existing systems, ensuring seamless data exchange and process automation. By adopting SoftExpert ECM, Hyundai was able to enhance its document control capabilities, reduce manual efforts, and improve overall operational efficiency.
Operational Impact
Quantitative Benefit
Case Study missing?
Start adding your own!
Register with your work email and create a new case study profile for your business.
Related Case Studies.
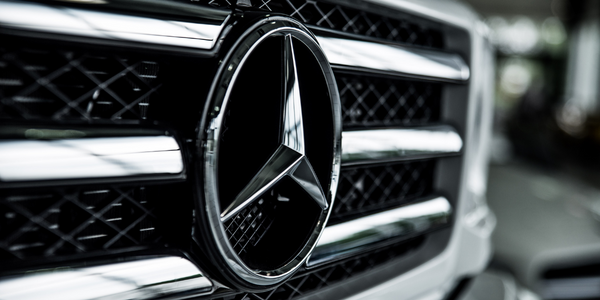
Case Study
Integral Plant Maintenance
Mercedes-Benz and his partner GAZ chose Siemens to be its maintenance partner at a new engine plant in Yaroslavl, Russia. The new plant offers a capacity to manufacture diesel engines for the Russian market, for locally produced Sprinter Classic. In addition to engines for the local market, the Yaroslavl plant will also produce spare parts. Mercedes-Benz Russia and his partner needed a service partner in order to ensure the operation of these lines in a maintenance partnership arrangement. The challenges included coordinating the entire maintenance management operation, in particular inspections, corrective and predictive maintenance activities, and the optimizing spare parts management. Siemens developed a customized maintenance solution that includes all electronic and mechanical maintenance activities (Integral Plant Maintenance).
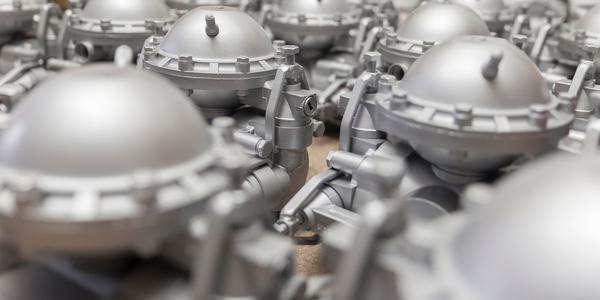
Case Study
Monitoring of Pressure Pumps in Automotive Industry
A large German/American producer of auto parts uses high-pressure pumps to deburr machined parts as a part of its production and quality check process. They decided to monitor these pumps to make sure they work properly and that they can see any indications leading to a potential failure before it affects their process.