Technology Category
- Analytics & Modeling - Digital Twin / Simulation
- Sensors - Haptic Sensors
Applicable Industries
- Equipment & Machinery
- Railway & Metro
Applicable Functions
- Product Research & Development
- Quality Assurance
Use Cases
- Digital Twin
- Virtual Reality
Services
- Testing & Certification
About The Customer
The customer in this case study is the Research Designs and Standards Organisation (RDSO), a unit under the Ministry of Railways in India. RDSO was established in 1957, integrating the Central Standards Office (CSO) and the Railway Testing and Research Centre (RTRC). The organization is responsible for testing and conducting applied research for the development of railway rolling stock, permanent way, and other related aspects. RDSO was tasked with the challenge of establishing Indian railways as a genuine supplier of Diesel locomotives for the South Asian and African market, requiring the development of a diesel locomotive that met stringent performance, reliability, and fuel economy demands.
The Challenge
The Research Designs and Standards Organisation (RDSO) was tasked with establishing Indian railways as a genuine supplier of Diesel locomotives for the South Asian and African market. The challenge was to develop a diesel locomotive that met performance, reliability, fuel economy, crashworthiness, and operator comfort demands. The locomotives needed to operate economically and safely for decades under harsh conditions with minimal downtime. Durability of components undergoing repeated fatigue cycles was a major concern, with most units logging more than 1 million miles during the first six years of operation and having a useful life of nearly 30 years. Some major components were expected to last more than 50 years in the used equipment market. Achieving these goals while shortening the development cycle was particularly challenging due to the significant time and cost factors associated with running physical tests on such large, complex machines. RDSO had been using simulation tools since 1990, but the time for pre-processing was too high due to limitations of computing machine and software.
The Solution
RDSO used HyperWorks for structural analysis in evaluating stress, deflection, and modal analysis of components. The simulation was also used to guide designers in sculpting the basic shape and topology optimization of parts early in development. Altair HyperMesh was used in detailed analysis of suspension dynamics, vibration isolation mounting of the cab and other subsystems, as well as in the validation of design/development and modifications of the crankcase, cylinder heads, piston rods, and other reciprocating parts of the locomotive’s diesel engine. Using Altair HyperMesh stress analysis of underframe/platform was performed and helped RDSO to optimize the under frame, also enabling to reduce weight which was penalty on account of increase in length due to induction on RE cab. HyperMesh is now a part of the standard design simulation process as a verification and validation tool.
Operational Impact
Quantitative Benefit
Case Study missing?
Start adding your own!
Register with your work email and create a new case study profile for your business.
Related Case Studies.

Case Study
Smart Water Filtration Systems
Before working with Ayla Networks, Ozner was already using cloud connectivity to identify and solve water-filtration system malfunctions as well as to monitor filter cartridges for replacements.But, in June 2015, Ozner executives talked with Ayla about how the company might further improve its water systems with IoT technology. They liked what they heard from Ayla, but the executives needed to be sure that Ayla’s Agile IoT Platform provided the security and reliability Ozner required.

Case Study
IoT enabled Fleet Management with MindSphere
In view of growing competition, Gämmerler had a strong need to remain competitive via process optimization, reliability and gentle handling of printed products, even at highest press speeds. In addition, a digitalization initiative also included developing a key differentiation via data-driven services offers.
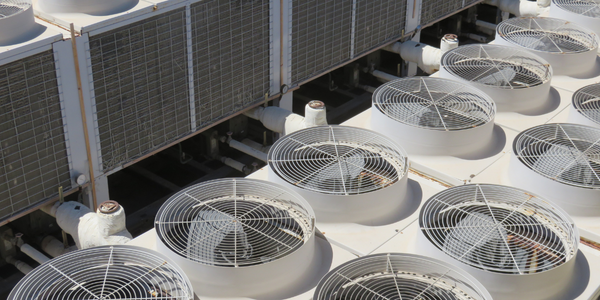
Case Study
Predictive Maintenance for Industrial Chillers
For global leaders in the industrial chiller manufacturing, reliability of the entire production process is of the utmost importance. Chillers are refrigeration systems that produce ice water to provide cooling for a process or industrial application. One of those leaders sought a way to respond to asset performance issues, even before they occur. The intelligence to guarantee maximum reliability of cooling devices is embedded (pre-alarming). A pre-alarming phase means that the cooling device still works, but symptoms may appear, telling manufacturers that a failure is likely to occur in the near future. Chillers who are not internet connected at that moment, provide little insight in this pre-alarming phase.

Case Study
Premium Appliance Producer Innovates with Internet of Everything
Sub-Zero faced the largest product launch in the company’s history:It wanted to launch 60 new products as scheduled while simultaneously opening a new “greenfield” production facility, yet still adhering to stringent quality requirements and manage issues from new supply-chain partners. A the same time, it wanted to increase staff productivity time and collaboration while reducing travel and costs.

Case Study
Integration of PLC with IoT for Bosch Rexroth
The application arises from the need to monitor and anticipate the problems of one or more machines managed by a PLC. These problems, often resulting from the accumulation over time of small discrepancies, require, when they occur, ex post technical operations maintenance.
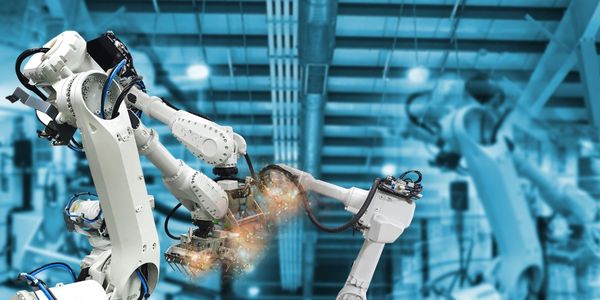
Case Study
Robot Saves Money and Time for US Custom Molding Company
Injection Technology (Itech) is a custom molder for a variety of clients that require precision plastic parts for such products as electric meter covers, dental appliance cases and spools. With 95 employees operating 23 molding machines in a 30,000 square foot plant, Itech wanted to reduce man hours and increase efficiency.