Technology Category
- Analytics & Modeling - Digital Twin / Simulation
- Automation & Control - Human Machine Interface (HMI)
Applicable Industries
- Aerospace
- Transportation
Applicable Functions
- Maintenance
- Product Research & Development
Use Cases
- Manufacturing Process Simulation
- Transportation Simulation
Services
- System Integration
- Testing & Certification
About The Customer
SOGECLAIR aerospace, part of the SOGECLAIR group, is a major partner in engineering and a prime contractor for the aerospace industry. The company is present in several countries including France, Spain, the United Kingdom, Germany, Tunisia, and Canada, as well as in the dollar zone and off-shore (India and Turkey). With a team of nearly 1000 highly qualified people, SOGECLAIR aerospace offers a variety of services including aero structures, systems installation, configuration and product data management, equipment, and manufacturing engineering. The company also provides Innovation & Development (I&D), project management, industrial cooperation programs, industrialization, integration, certification, processes, quality, IT resources, procurement, subcontracting, support, aftersales and more.
The Challenge
SOGECLAIR aerospace, a major partner in engineering and prime contractor for the aerospace industry, was tasked with the development of a new flooring concept for aircraft cabins. The challenge was to create a lighter structure, adjustable panels for all types of aircraft, and ensure easier installation and maintenance. The aerospace industry has always been at the forefront of weight optimization and lightweight design, hence it was not surprising that aerospace also was one of the first industries to use alternative materials such as composites. The engineers had to consider conflicting issues such as weight, design, maximal dimensions, strength, stiffness etc. The use of optimization technology is the solution to combine all of these constrains with respect to an optimal composite layout. In this context SOGECLAIR aerospace investigates innovative materials and processes to integrate them in the design, analysis, and optimization.
The Solution
To address these challenges, SOGECLAIR aerospace employed Altair's HyperWorks suite, particularly HyperMesh and HyperView as a pre- and postprocessor, OptiStruct for optimization issues, RADIOSS for linear and nonlinear simulation, and solidThinking Evolve/Inspire for concept modeling. In a typical project, the first step is a feasibility study of the objectives to clear up whether it is possible to create an efficient solution. To develop composite structures, the engineers conduct Freesize and Size optimizations defining different patches and layer thicknesses of the composite material, followed by a shuffle optimization to determine the optimal stacking sequence of the single layers. Also gauge optimizations are conducted in order to reach the optimal dimensions of the composite stiffener. In the subsequent development process, the engineers compare the numerical analysis results with tests data, in particular the strains in different stackings.
Operational Impact
Quantitative Benefit
Case Study missing?
Start adding your own!
Register with your work email and create a new case study profile for your business.
Related Case Studies.
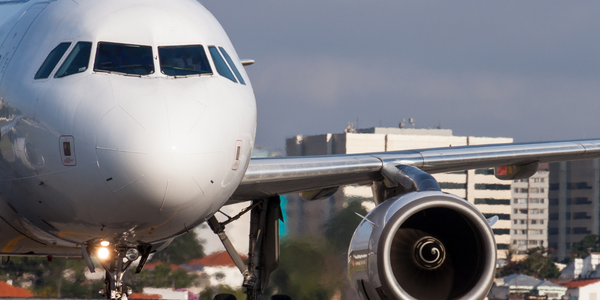
Case Study
Airbus Soars with Wearable Technology
Building an Airbus aircraft involves complex manufacturing processes consisting of thousands of moving parts. Speed and accuracy are critical to business and competitive advantage. Improvements in both would have high impact on Airbus’ bottom line. Airbus wanted to help operators reduce the complexity of assembling cabin seats and decrease the time required to complete this task.
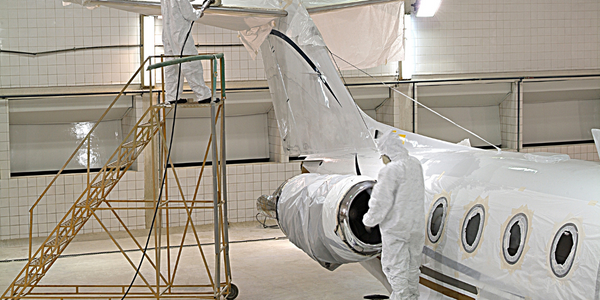
Case Study
Aircraft Predictive Maintenance and Workflow Optimization
First, aircraft manufacturer have trouble monitoring the health of aircraft systems with health prognostics and deliver predictive maintenance insights. Second, aircraft manufacturer wants a solution that can provide an in-context advisory and align job assignments to match technician experience and expertise.
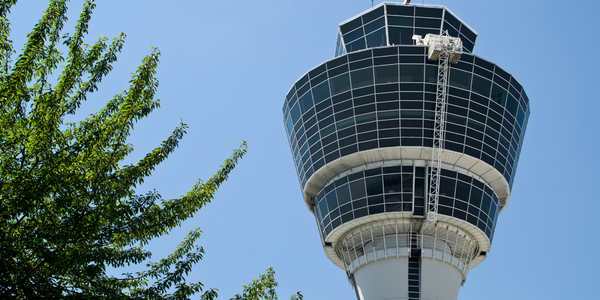
Case Study
Airport SCADA Systems Improve Service Levels
Modern airports are one of the busiest environments on Earth and rely on process automation equipment to ensure service operators achieve their KPIs. Increasingly airport SCADA systems are being used to control all aspects of the operation and associated facilities. This is because unplanned system downtime can cost dearly, both in terms of reduced revenues and the associated loss of customer satisfaction due to inevitable travel inconvenience and disruption.
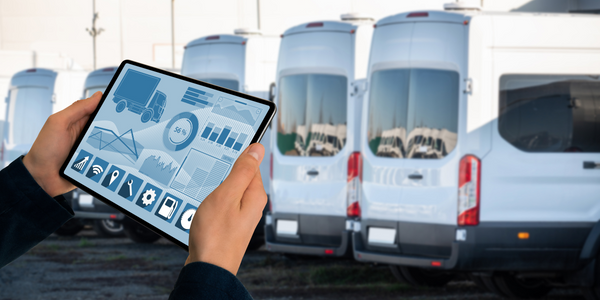
Case Study
IoT-based Fleet Intelligence Innovation
Speed to market is precious for DRVR, a rapidly growing start-up company. With a business model dependent on reliable mobile data, managers were spending their lives trying to negotiate data roaming deals with mobile network operators in different countries. And, even then, service quality was a constant concern.
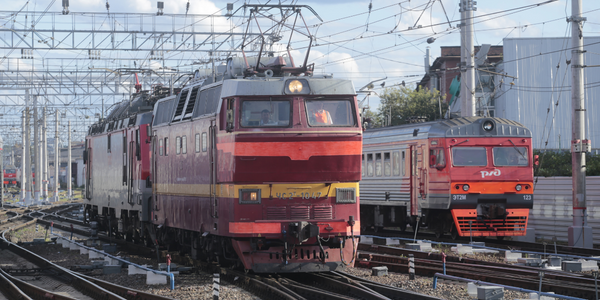
Case Study
Digitize Railway with Deutsche Bahn
To reduce maintenance costs and delay-causing failures for Deutsche Bahn. They need manual measurements by a position measurement system based on custom-made MEMS sensor clusters, which allow autonomous and continuous monitoring with wireless data transmission and long battery. They were looking for data pre-processing solution in the sensor and machine learning algorithms in the cloud so as to detect critical wear.
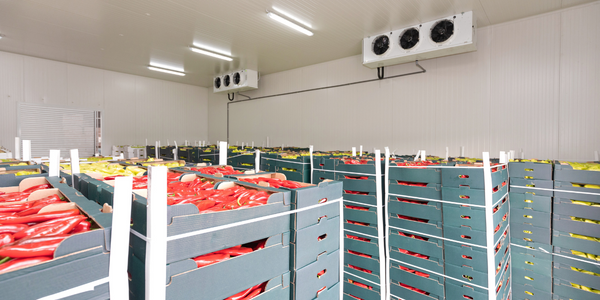
Case Study
Cold Chain Transportation and Refrigerated Fleet Management System
1) Create a digital connected transportation solution to retrofit cold chain trailers with real-time tracking and controls. 2) Prevent multi-million dollar losses due to theft or spoilage. 3) Deliver a digital chain-of-custody solution for door to door load monitoring and security. 4) Provide a trusted multi-fleet solution in a single application with granular data and access controls.