How Toyota leverages Appsheet to drive productivity at its manufacturing plant
Customer Company Size
Large Corporate
Region
- America
Country
- United States
Product
- AppSheet
Tech Stack
- No-Code Development Platform
- Mobile Responsive Apps
Implementation Scale
- Enterprise-wide Deployment
Impact Metrics
- Productivity Improvements
- Customer Satisfaction
- Employee Satisfaction
Technology Category
- Platform as a Service (PaaS) - Application Development Platforms
- Functional Applications - Remote Monitoring & Control Systems
Applicable Industries
- Automotive
Applicable Functions
- Quality Assurance
- Product Research & Development
Use Cases
- Predictive Maintenance
- Machine Condition Monitoring
- Remote Asset Management
Services
- Software Design & Engineering Services
- System Integration
About The Customer
Toyota, a global leader in automotive manufacturing, is renowned for its commitment to lean production and continuous improvement. The company operates seven manufacturing plants across North America and is dedicated to optimizing its vehicle assembly process. Toyota's North American engineering headquarters is located in Lexington, Kentucky, where ergonomist Ben Atkinson oversees the collection and analysis of assembly line data to enhance productivity and worker comfort. The company is constantly seeking innovative solutions to streamline its operations and improve the quality of its vehicles, aligning with its philosophy of manufacturing excellence.
The Challenge
Toyota’s assembly data was trapped in spreadsheets, making it difficult to share data across plants or upstream. The company needed an enterprise application to collect data from the assembly lines and create a central database. However, IT was unable to justify the resources to build an application from scratch for a user base of fewer than 100 people. Existing applications offered by Toyota developers were not equipped to meet the specific needs without significant revision and lacked a mobile interface crucial for data collection on the plant floor. This led to frustration among non-developer line-of-business users like ergonomist Ben Atkinson, who saw the potential for data to drive productivity improvements but faced obstacles in collecting it from mobile workers.
The Solution
Toyota turned to AppSheet, a no-code app development platform, to address its data collection challenges. AppSheet allowed Toyota to quickly create mobile-responsive apps without the need for developer time or upfront costs. The platform's intuitive interface enabled easy adoption, drawing data from existing spreadsheets and ensuring data protection and security. With AppSheet, Toyota could gather assembly line data on the fly, providing real-time insights into productivity and quality improvements. The platform facilitated seamless data collection and sharing across plants, enabling teams to make informed decisions based on up-to-date information. This approach aligned with Toyota's lean philosophy, allowing for rapid iteration and refinement of the app to meet the specific needs of the assembly process.
Operational Impact
Quantitative Benefit
Case Study missing?
Start adding your own!
Register with your work email and create a new case study profile for your business.
Related Case Studies.
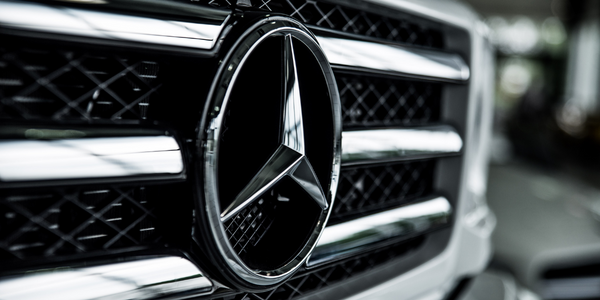
Case Study
Integral Plant Maintenance
Mercedes-Benz and his partner GAZ chose Siemens to be its maintenance partner at a new engine plant in Yaroslavl, Russia. The new plant offers a capacity to manufacture diesel engines for the Russian market, for locally produced Sprinter Classic. In addition to engines for the local market, the Yaroslavl plant will also produce spare parts. Mercedes-Benz Russia and his partner needed a service partner in order to ensure the operation of these lines in a maintenance partnership arrangement. The challenges included coordinating the entire maintenance management operation, in particular inspections, corrective and predictive maintenance activities, and the optimizing spare parts management. Siemens developed a customized maintenance solution that includes all electronic and mechanical maintenance activities (Integral Plant Maintenance).
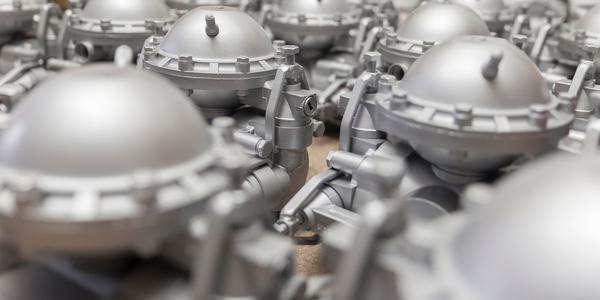
Case Study
Monitoring of Pressure Pumps in Automotive Industry
A large German/American producer of auto parts uses high-pressure pumps to deburr machined parts as a part of its production and quality check process. They decided to monitor these pumps to make sure they work properly and that they can see any indications leading to a potential failure before it affects their process.