Company Size
1,000+
Region
- America
Country
- United States
Product
- Intelex EHS Incident Management
- Intelex Claims Management
- Intelex Safety Hazards
- Intelex Observations
- Intelex Training Management
Tech Stack
- Data Integration
- Predictive Analysis
Implementation Scale
- Enterprise-wide Deployment
Impact Metrics
- Cost Savings
- Employee Satisfaction
- Productivity Improvements
Technology Category
- Analytics & Modeling - Predictive Analytics
- Application Infrastructure & Middleware - Data Exchange & Integration
Applicable Industries
- Construction & Infrastructure
Applicable Functions
- Discrete Manufacturing
- Quality Assurance
Use Cases
- Predictive Maintenance
- Process Control & Optimization
Services
- Software Design & Engineering Services
- System Integration
About The Customer
Moss is a leader in the construction business in America, building residential, educational, correctional, public assembly and military projects, with a specialization in solar construction. With offices that extend from Florida to Hawaii, the family-owned company has been recognized by the Occupational Safety and Health Administration (OSHA) as an elite construction company within the agency’s Safety Recognition Program. Moss specializes in creating work environments that are safe, secure and supportive. At Moss, they recognize safety as a value and expect the same from every partner, vendor and subcontractor with whom they work.
The Challenge
Moss, a leader in the construction business in America, was looking for a fully integrated safety, risk and claims management platform. The company needed to integrate its dispersed and siloed data into a single database. They could use it to extract knowledge that could be used to understand what was happening in the business and to identify opportunities for improvement. Legacy manual systems simply would not allow Moss to be predictive and achieve the kind of growth rate they were seeking. Moss’ Safety Management System had a good foundation, but lacked comprehensive and analytical views – including the ability to assess incidents and claims together. It also did not have predictive analysis capabilities. Moss wanted to move to an SMS/RMIS (Safety Management System/Risk Management Information System) that provides a more integrated view of a working environment.
The Solution
Moss turned to Intelex in early 2016, not only because they saw how the software could benefit their operations, but also because they recognized that Intelex shared its corporate values and culture. The more Moss learned about Intelex, the more natural a fit the partnership seemed to be. Moss launched the Intelex EHS Incident Management and Claims Management applications in late 2016. In 2018, Safety Hazards, Observations, Training Management, and Safety Meeting Management went live. With the Intelex EHSQ platform, Moss’ 20-member cross-country safety team has moved beyond its older flat-file processes, which were powered on a shared server for 14 years, to a fully integrated platform that provides safety, risk and claims management. Having everything driven through Intelex integrates all data into a single database where more comprehensive analysis can occur. Moss is now able to see trends across the entire footprint of the company. Intelex told them where to spend their safety-related efforts.
Operational Impact
Quantitative Benefit
Case Study missing?
Start adding your own!
Register with your work email and create a new case study profile for your business.
Related Case Studies.

Case Study
IoT System for Tunnel Construction
The Zenitaka Corporation ('Zenitaka') has two major business areas: its architectural business focuses on structures such as government buildings, office buildings, and commercial facilities, while its civil engineering business is targeted at structures such as tunnels, bridges and dams. Within these areas, there presented two issues that have always persisted in regard to the construction of mountain tunnels. These issues are 'improving safety" and "reducing energy consumption". Mountain tunnels construction requires a massive amount of electricity. This is because there are many kinds of electrical equipment being used day and night, including construction machinery, construction lighting, and ventilating fan. Despite this, the amount of power consumption is generally not tightly managed. In many cases, the exact amount of power consumption is only ascertained when the bill from the power company becomes available. Sometimes, corporations install demand-monitoring equipment to help curb the maximum power demanded. However, even in these cases, the devices only allow the total volume of power consumption to be ascertained, or they may issue warnings to prevent the contracted volume of power from being exceeded. In order to tackle the issue of reducing power consumption, it was first necessary to obtain an accurate breakdown of how much power was being used in each particular area. In other words, we needed to be able to visualize the amount of power being consumed. Safety, was also not being managed very rigorously. Even now, tunnel construction sites often use a 'name label' system for managing entry into the work site. Specifically, red labels with white reverse sides that bear the workers' names on both sides are displayed at the tunnel work site entrance. The workers themselves then flip the name label to the appropriate side when entering or exiting from the work site to indicate whether or not they are working inside the tunnel at any given time. If a worker forgets to flip his or her name label when entering or exiting from the tunnel, management cannot be performed effectively. In order to tackle the challenges mentioned above, Zenitaka decided to build a system that could improve the safety of tunnel construction as well as reduce the amount of power consumed. In other words, this new system would facilitate a clear picture of which workers were working in each location at the mountain tunnel construction site, as well as which processes were being carried out at those respective locations at any given time. The system would maintain the safety of all workers while also carefully controlling the electrical equipment to reduce unnecessary power consumption. Having decided on the concept, our next concern was whether there existed any kind of robust hardware that would not break down at the construction work site, that could move freely in response to changes in the working environment, and that could accurately detect workers and vehicles using radio frequency identification (RFID). Given that this system would involve many components that were new to Zenitaka, we decided to enlist the cooperation of E.I.Sol Co., Ltd. ('E.I.Sol') as our joint development partner, as they had provided us with a highly practical proposal.
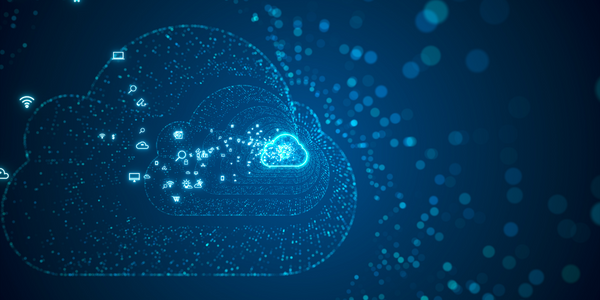
Case Study
Splunk Partnership Ties Together Big Data & IoT Services
Splunk was faced with the need to meet emerging customer demands for interfacing IoT projects to its suite of services. The company required an IoT partner that would be able to easily and quickly integrate with its Splunk Enterprise platform, rather than allocating development resources and time to building out an IoT interface and application platform.
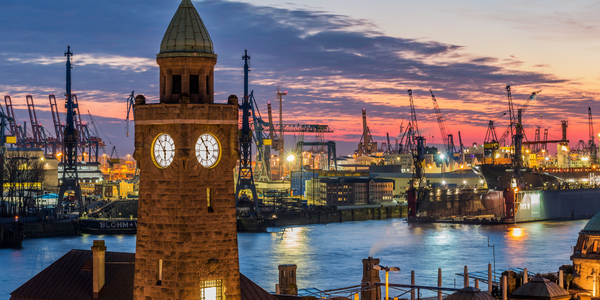
Case Study
Bridge monitoring in Hamburg Port
Kattwyk Bridge is used for both rail and road transport, and it has played an important role in the Port of Hamburg since 1973. However, the increasing pressure from traffic requires a monitoring solution. The goal of the project is to assess in real-time the bridge's status and dynamic responses to traffic and lift processes.
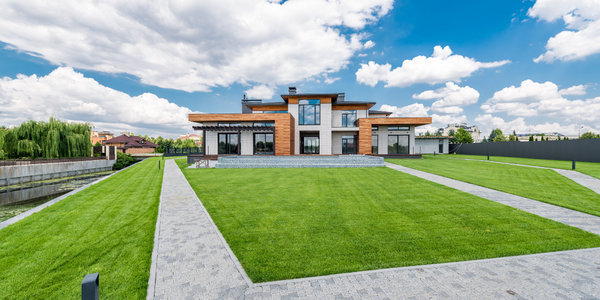
Case Study
Bellas Landscaping
Leading landscaping firm serving central Illinois streamlines operations with Samsara’s real-time fleet tracking solution: • 30+ vehicle fleet includes International Terrastar dump trucks and flatbeds, medium- and light-duty pickups from Ford and Chevrolet. Winter fleet includes of snow plows and salters.
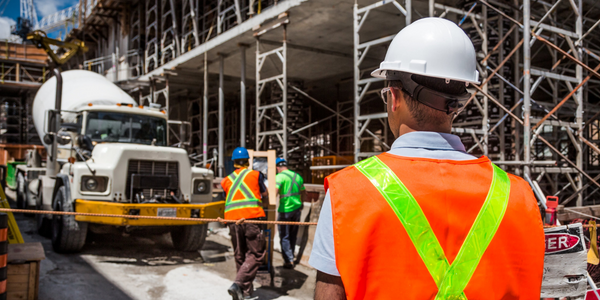
Case Study
Condition Based Monitoring for Industrial Systems
A large construction aggregate plant operates 10 high horsepower Secondary Crusher Drive Motors and associated conveyor belts, producing 600 tons of product per hour. All heavy equipment requires maintenance, but the aggregate producer’s costs were greatly magnified any time that the necessary maintenance was unplanned and unscheduled. The product must be supplied to the customers on a tight time schedule to fulfill contracts, avoid penalties, and prevent the loss of future business. Furthermore, a sudden failure in one of the drive motors would cause rock to pile up in unwanted locations, extending the downtime and increasing the costs.Clearly, preventative maintenance was preferable to unexpected failures. So, twice each year, the company brought in an outside vendor to attach sensors to the motors, do vibration studies, measure bearing temperatures and attempt to assess the health of the motors. But that wasn’t enough. Unexpected breakdowns continued to occur. The aggregate producer decided to upgrade to a Condition Based Monitoring (CBM) sensor system that could continually monitor the motors in real time, apply data analytics to detect changes in motor behavior before they developed into major problems, and alert maintenance staff via email or text, anywhere they happened to be.A wired sensor network would have been cost prohibitive. An aggregate plant has numerous heavy vehicles moving around, so any cabling would have to be protected. But the plant covers 400 acres, and the cable would have to be trenched to numerous locations. Cable wasn’t going to work. The aggregate producer needed a wireless solution.