How Dana masters supply chain risk with The riskmethods Solution
Customer Company Size
Large Corporate
Country
- China
- Mexico
- Turkey
Product
- The riskmethods Solution
Tech Stack
- AI Engine
Implementation Scale
- Enterprise-wide Deployment
Impact Metrics
- Customer Satisfaction
- Digital Expertise
- Productivity Improvements
Technology Category
- Analytics & Modeling - Predictive Analytics
- Analytics & Modeling - Real Time Analytics
- Application Infrastructure & Middleware - Data Exchange & Integration
Applicable Industries
- Automotive
Applicable Functions
- Procurement
- Logistics & Transportation
- Quality Assurance
Use Cases
- Supply Chain Visibility
- Predictive Maintenance
Services
- System Integration
- Data Science Services
About The Customer
Dana is a world leader in highly-engineered solutions aimed at improving the efficiency, performance, and sustainability of powered vehicles and machinery. With a vision to be the global technology leader in efficient power conveyance and energy-management solutions, Dana helps its customers achieve their sustainability objectives. The company operates 145 major facilities, including 26 tech centers, employs 36,000 people across 33 countries, and serves 15,000 customers in 141 countries. Dana's global supply chain includes approximately 10,000 supply paths, making risk management a critical aspect of their operations.
The Challenge
Dana, a major supplier in the automotive industry, faced significant challenges in managing their complex supply chain. With over 100 manufacturing sites, thousands of supplier sites, and nearly 10,000 supply paths globally, Dana needed a more efficient way to gather information and respond to customer inquiries during supply chain disruptions. Additionally, they lacked sufficient data to monitor risks related to geographic regions, such as natural disasters or geopolitical events. This made it difficult for Dana to proactively manage risks and ensure the stability of their supply chain.
The Solution
Dana implemented The riskmethods Solution to enhance their risk management capabilities. The solution's AI engine provides Dana with the necessary risk data to gain a comprehensive and accurate picture of the risks threatening their supply chain. This information allows Dana to identify risky suppliers and develop action plans in case a supplier is compromised. The riskmethods Solution also features a world map displayed in Dana's offices, raising awareness of supply chain risks across various departments, including procurement, quality, material planning, and logistics. Additionally, the solution has significantly reduced customer-response times regarding disruptions, making Dana a preferred partner for OEMs.
Operational Impact
Quantitative Benefit
Case Study missing?
Start adding your own!
Register with your work email and create a new case study profile for your business.
Related Case Studies.
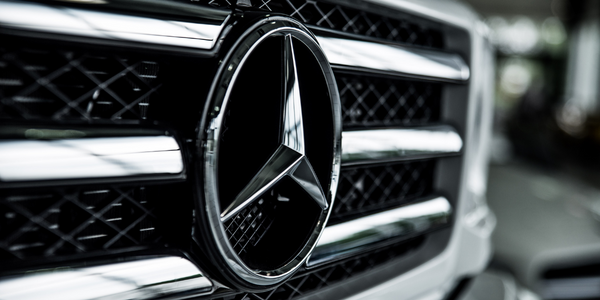
Case Study
Integral Plant Maintenance
Mercedes-Benz and his partner GAZ chose Siemens to be its maintenance partner at a new engine plant in Yaroslavl, Russia. The new plant offers a capacity to manufacture diesel engines for the Russian market, for locally produced Sprinter Classic. In addition to engines for the local market, the Yaroslavl plant will also produce spare parts. Mercedes-Benz Russia and his partner needed a service partner in order to ensure the operation of these lines in a maintenance partnership arrangement. The challenges included coordinating the entire maintenance management operation, in particular inspections, corrective and predictive maintenance activities, and the optimizing spare parts management. Siemens developed a customized maintenance solution that includes all electronic and mechanical maintenance activities (Integral Plant Maintenance).
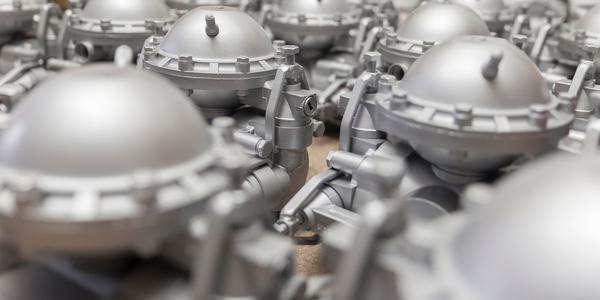
Case Study
Monitoring of Pressure Pumps in Automotive Industry
A large German/American producer of auto parts uses high-pressure pumps to deburr machined parts as a part of its production and quality check process. They decided to monitor these pumps to make sure they work properly and that they can see any indications leading to a potential failure before it affects their process.