Henny Penny Cooks Up Big Benefits with Warehouse Automation
Customer Company Size
Large Corporate
Country
- United States
Product
- RF-SMART
- JD Edwards EnterpriseOne
- Warehouse Automation Module
Tech Stack
- RF-SMART Workflows
- JD Edwards Integration
Implementation Scale
- Enterprise-wide Deployment
Impact Metrics
- Productivity Improvements
- Customer Satisfaction
- Cost Savings
Technology Category
- Functional Applications - Warehouse Management Systems (WMS)
- Application Infrastructure & Middleware - Data Exchange & Integration
- Functional Applications - Remote Monitoring & Control Systems
Applicable Industries
- Food & Beverage
- Retail
Applicable Functions
- Warehouse & Inventory Management
- Logistics & Transportation
Use Cases
- Warehouse Automation
- Inventory Management
- Process Control & Optimization
Services
- System Integration
- Software Design & Engineering Services
About The Customer
Henny Penny designs and manufactures foodservice equipment solutions, including fryers and rotisseries, serving well-known names like Chick-fil-A and McDonald’s. Besides their manufacturing operations, they also run a small parts distribution operation for their global network of service providers. The company is known for its innovative solutions and commitment to customer service, making it a key player in the foodservice industry. With a growing business, Henny Penny continuously seeks ways to improve efficiency and maintain high standards of customer satisfaction.
The Challenge
Henny Penny faced challenges with manual data entry and inaccuracy in their parts distribution operation. Despite using RF-SMART in their finished goods area, there was room for improvement in their parts distribution process. The company needed to optimize picking for their parts distribution and decided to bring in vertical lift towers. This required integrating the software for their picking towers with their existing systems, a task that was handed over to Bob Blackburn's team.
The Solution
Henny Penny selected RF-SMART due to its highly configurable software, proven integration with JD Edwards EnterpriseOne, and top-tier customer service. They began using RF-SMART to pick orders and validate the correct items were sent to the appropriate customer. The company utilized various RF-SMART workflows, including Work Order Completion, Picking, and Ship Confirm. The configurable nature of RF-SMART allowed Henny Penny to tailor it to their unique business processes, saving time and boosting efficiency in their warehouse. To further optimize their parts distribution, Henny Penny integrated vertical lift towers with RF-SMART. The integration of picking towers to JD Edwards was seamless, with RF-SMART handling all data exchange and keeping JD Edwards up to date in real-time. This integration allowed for accurate inventory management and real-time visibility, significantly improving their operations.
Operational Impact
Quantitative Benefit
Case Study missing?
Start adding your own!
Register with your work email and create a new case study profile for your business.
Related Case Studies.

Case Study
The Kellogg Company
Kellogg keeps a close eye on its trade spend, analyzing large volumes of data and running complex simulations to predict which promotional activities will be the most effective. Kellogg needed to decrease the trade spend but its traditional relational database on premises could not keep up with the pace of demand.

Case Study
HEINEKEN Uses the Cloud to Reach 10.5 Million Consumers
For 2012 campaign, the Bond promotion, it planned to launch the campaign at the same time everywhere on the planet. That created unprecedented challenges for HEINEKEN—nowhere more so than in its technology operation. The primary digital content for the campaign was a 100-megabyte movie that had to play flawlessly for millions of viewers worldwide. After all, Bond never fails. No one was going to tolerate a technology failure that might bruise his brand.Previously, HEINEKEN had supported digital media at its outsourced datacenter. But that datacenter lacked the computing resources HEINEKEN needed, and building them—especially to support peak traffic that would total millions of simultaneous hits—would have been both time-consuming and expensive. Nor would it have provided the geographic reach that HEINEKEN needed to minimize latency worldwide.
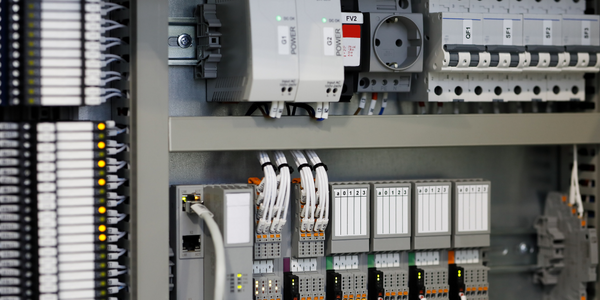
Case Study
Improving Production Line Efficiency with Ethernet Micro RTU Controller
Moxa was asked to provide a connectivity solution for one of the world's leading cosmetics companies. This multinational corporation, with retail presence in 130 countries, 23 global braches, and over 66,000 employees, sought to improve the efficiency of their production process by migrating from manual monitoring to an automatic productivity monitoring system. The production line was being monitored by ABB Real-TPI, a factory information system that offers data collection and analysis to improve plant efficiency. Due to software limitations, the customer needed an OPC server and a corresponding I/O solution to collect data from additional sensor devices for the Real-TPI system. The goal is to enable the factory information system to more thoroughly collect data from every corner of the production line. This will improve its ability to measure Overall Equipment Effectiveness (OEE) and translate into increased production efficiencies. System Requirements • Instant status updates while still consuming minimal bandwidth to relieve strain on limited factory networks • Interoperable with ABB Real-TPI • Small form factor appropriate for deployment where space is scarce • Remote software management and configuration to simplify operations

Case Study
Energy Management System at Sugar Industry
The company wanted to use the information from the system to claim under the renewable energy certificate scheme. The benefit to the company under the renewable energy certificates is Rs 75 million a year. To enable the above, an end-to-end solution for load monitoring, consumption monitoring, online data monitoring, automatic meter data acquisition which can be exported to SAP and other applications is required.
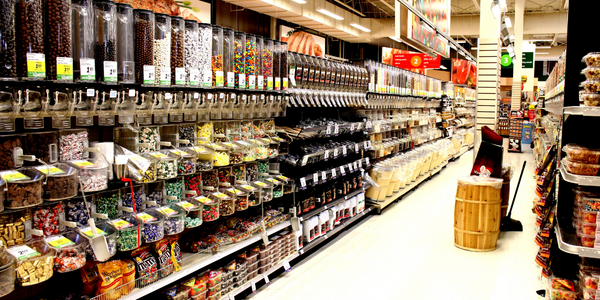
Case Study
How Sirqul’s IoT Platform is Crafting Carrefour’s New In-Store Experiences
Carrefour Taiwan’s goal is to be completely digital by end of 2018. Out-dated manual methods for analysis and assumptions limited Carrefour’s ability to change the customer experience and were void of real-time decision-making capabilities. Rather than relying solely on sales data, assumptions, and disparate systems, Carrefour Taiwan’s CEO led an initiative to find a connected IoT solution that could give the team the ability to make real-time changes and more informed decisions. Prior to implementing, Carrefour struggled to address their conversion rates and did not have the proper insights into the customer decision-making process nor how to make an immediate impact without losing customer confidence.