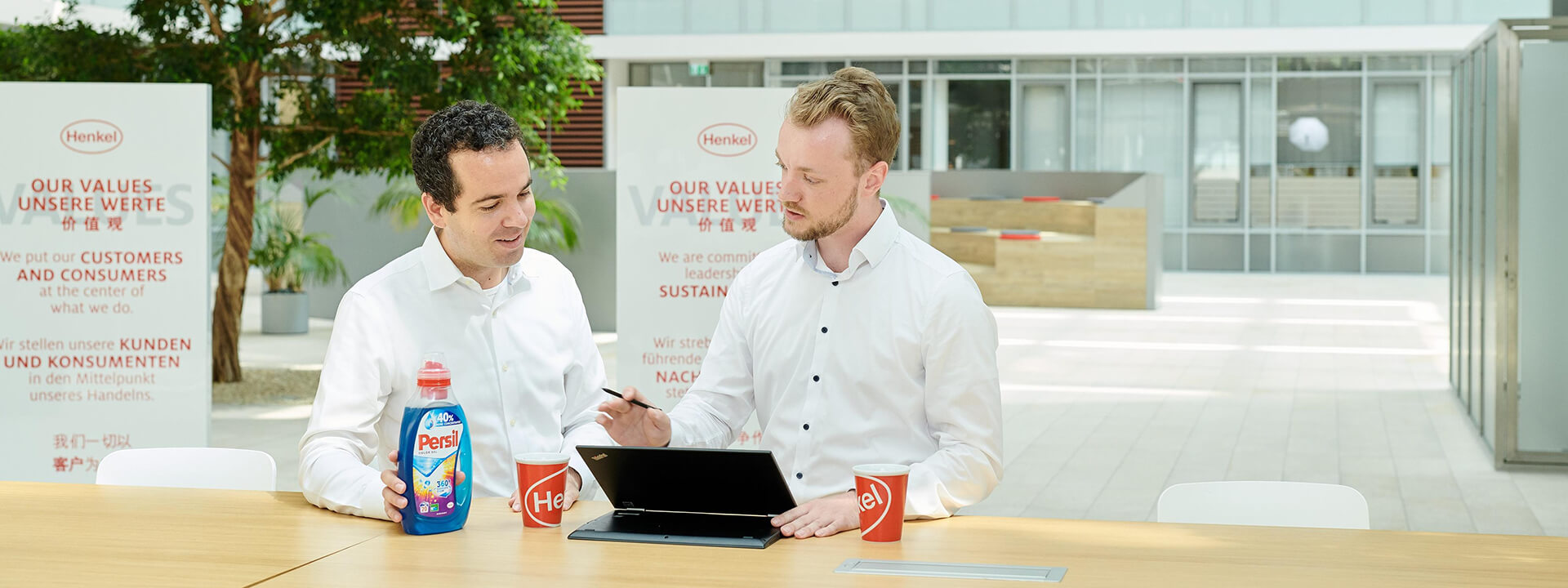
Technology Category
- Cybersecurity & Privacy - Endpoint Security
- Infrastructure as a Service (IaaS) - Hybrid Cloud
Applicable Industries
- Cement
- Consumer Goods
Applicable Functions
- Logistics & Transportation
- Product Research & Development
Use Cases
- Construction Management
- Personnel Tracking & Monitoring
Services
- Cloud Planning, Design & Implementation Services
- Training
The Customer
Henkel
About The Customer
Henkel is a global leader in the chemical and consumer goods industries, operating on almost every continent. Over the past 145 years, the company has demonstrated resilience, innovation, and growth, adapting to changing environments and overcoming unexpected obstacles. Henkel's success can be attributed to its ability to leverage digital transformation to strengthen connections with its 53,000 employees and consumers. In 2018, the company quickly relocated over 46,000 non-essential staff to work from home, demonstrating its agility in adapting to shifting landscapes.
The Challenge
Henkel, a global powerhouse in the chemical and consumer goods industries, faced the challenge of accelerating its digital transformation to strengthen relationships with employees, customers, and consumers, while reducing the cost of provisioning and supporting workplace technology. The company aimed to provide smooth and accessible workplace technology to support productivity among its thousands of employees. The situation became more critical when the COVID-19 pandemic forced the company to move its more than 46,000 non-critical employees to work from home while maintaining the high-performing services staff enjoyed in the office. Achieving successful digital transformation required changes that enabled employees to adapt to new processes and resources in any situation.
The Solution
Henkel partnered with Unisys to deploy Digital Workplace Solutions, including a service desk with desktop management and support, on-site Tec-Stop (support and IT learning center) at three of the company’s locations, and a virtual Tec-Stop service to deliver critical aid and device distribution for employees working from home. Unisys also provided Cloud, Applications & Infrastructure Solutions, including data center transformation advice and engineering, endpoint security, and managed network services. The entire project was completed within Henkel’s service level agreement, with no network or application services degradation. Unisys also launched a virtual Tec-Stop service that provided device support and distribution for remote workers and on-site staff, ensuring that critical operations remained uninterrupted.
Operational Impact
Quantitative Benefit
Case Study missing?
Start adding your own!
Register with your work email and create a new case study profile for your business.
Related Case Studies.
.png)
Case Study
Improving Vending Machine Profitability with the Internet of Things (IoT)
The vending industry is undergoing a sea change, taking advantage of new technologies to go beyond just delivering snacks to creating a new retail location. Intelligent vending machines can be found in many public locations as well as company facilities, selling different types of goods and services, including even computer accessories, gold bars, tickets, and office supplies. With increasing sophistication, they may also provide time- and location-based data pertaining to sales, inventory, and customer preferences. But at the end of the day, vending machine operators know greater profitability is driven by higher sales and lower operating costs.

Case Study
System 800xA at Indian Cement Plants
Chettinad Cement recognized that further efficiencies could be achieved in its cement manufacturing process. It looked to investing in comprehensive operational and control technologies to manage and derive productivity and energy efficiency gains from the assets on Line 2, their second plant in India.
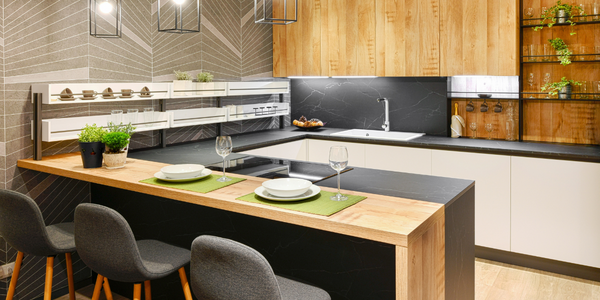
Case Study
Series Production with Lot-size-1 Flexibility
Nobilia manufactures customized fitted kitchens with a lot size of 1. They require maximum transparency of tracking design data and individual processing steps so that they can locate a particular piece of kitchen furniture in the sequence of processes.
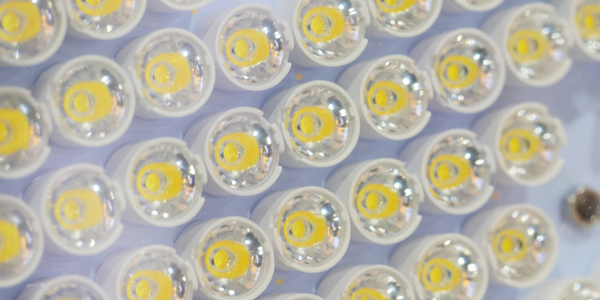
Case Study
American Eagle Achieves LEED with GE LED Lighting Fixtures
American Eagle Outfitters (AEO) was in the process of building a new distribution center. The AEO facility management team decided to look at alternate options for lighting layout that could provide energy and maintenance savings. AEO would need a full-time maintenance employee just to replace burned-out fluorescent tubes.