Customer Company Size
Mid-size Company
Region
- Europe
Product
- QlikView
Tech Stack
- Microsoft Dynamics
- MS Excel
- SQL Server
- Windows Server 2008 RC2 64-bit
Implementation Scale
- Enterprise-wide Deployment
Impact Metrics
- Productivity Improvements
- Cost Savings
Technology Category
- Application Infrastructure & Middleware - Data Visualization
Applicable Industries
- Construction & Infrastructure
Applicable Functions
- Discrete Manufacturing
- Business Operation
Use Cases
- Visual Quality Detection
- Predictive Quality Analytics
Services
- Data Science Services
About The Customer
Heembouw is a one-stop provider of building services, catering for architecture, new building and renovation of non-residential buildings, offices and residential property. The company has 280 staff and revenue of over 110 million Euros. Heembouw’s mission is to create added value for its customers. For this purpose, it draws inspiration from the Lean philosophy, which has led to the development of a unique view on the building process: Lean Building according to Heembouw. The company views collaboration as a precondition for success. Performance is not about the individual performance, but the ability to perform as a team and as a collective. In its capacity of chain producer, Heembouw does everything it can to mobilise knowledge, to bring the right parties together and to forge a uniform whole. Chain collaboration, chain integration or supply chain management in other words — using one another’s knowledge to jointly achieve an optimum product on behalf of the client. Heembouw has based its new building and renovation projects on the Lean philosophy since 2005. This has resulted in proven successes, such as a 10-40% shorter building time, 40% less post-delivery issues, 45% less complaints and 13% less accidents.
The Challenge
Heembouw, a one-stop provider of building services, was facing challenges in enhancing visual management in support of the Lean management philosophy. The company was struggling with minimizing error margins during the data entry process for management dashboards and automating the input process for existing dashboards. The publication of the dashboards was too time-consuming for the employees as they had to retrieve data from source systems and enter them manually into Excel sheets. With 30 to 40 project dashboards a month, automating this process seemed a viable option. Moreover, visual management was starting to play an increasingly important role in the organization, so many dashboards had already been developed in Excel.
The Solution
Heembouw uses QlikView to enhance its visual management. Relevant data are made insightful and made available at the right time (Just-in-Time). QlikView offers stakeholders access to the right management information anytime, anywhere. This makes it possible for adjustments to be made more quickly during building projects, something that can result in major cost savings. Examples are, quicker insight into opportunities and risks and more efficient sourcing. Moreover, thanks to the QlikView dashboards, Heembouw can now quickly visualize the importance and benefits of registering data, which further encourages people to record information. The data source systems used include QlikView version 11, Microsoft Dynamics (previously Navision) and MS Excel. The database used is C-SIDE (until 2012), and henceforth SQL Server. The server is a virtualised server running on Windows Server 2008 RC2 64-bit with 24GB of RAM.
Operational Impact
Quantitative Benefit
Case Study missing?
Start adding your own!
Register with your work email and create a new case study profile for your business.
Related Case Studies.

Case Study
IoT System for Tunnel Construction
The Zenitaka Corporation ('Zenitaka') has two major business areas: its architectural business focuses on structures such as government buildings, office buildings, and commercial facilities, while its civil engineering business is targeted at structures such as tunnels, bridges and dams. Within these areas, there presented two issues that have always persisted in regard to the construction of mountain tunnels. These issues are 'improving safety" and "reducing energy consumption". Mountain tunnels construction requires a massive amount of electricity. This is because there are many kinds of electrical equipment being used day and night, including construction machinery, construction lighting, and ventilating fan. Despite this, the amount of power consumption is generally not tightly managed. In many cases, the exact amount of power consumption is only ascertained when the bill from the power company becomes available. Sometimes, corporations install demand-monitoring equipment to help curb the maximum power demanded. However, even in these cases, the devices only allow the total volume of power consumption to be ascertained, or they may issue warnings to prevent the contracted volume of power from being exceeded. In order to tackle the issue of reducing power consumption, it was first necessary to obtain an accurate breakdown of how much power was being used in each particular area. In other words, we needed to be able to visualize the amount of power being consumed. Safety, was also not being managed very rigorously. Even now, tunnel construction sites often use a 'name label' system for managing entry into the work site. Specifically, red labels with white reverse sides that bear the workers' names on both sides are displayed at the tunnel work site entrance. The workers themselves then flip the name label to the appropriate side when entering or exiting from the work site to indicate whether or not they are working inside the tunnel at any given time. If a worker forgets to flip his or her name label when entering or exiting from the tunnel, management cannot be performed effectively. In order to tackle the challenges mentioned above, Zenitaka decided to build a system that could improve the safety of tunnel construction as well as reduce the amount of power consumed. In other words, this new system would facilitate a clear picture of which workers were working in each location at the mountain tunnel construction site, as well as which processes were being carried out at those respective locations at any given time. The system would maintain the safety of all workers while also carefully controlling the electrical equipment to reduce unnecessary power consumption. Having decided on the concept, our next concern was whether there existed any kind of robust hardware that would not break down at the construction work site, that could move freely in response to changes in the working environment, and that could accurately detect workers and vehicles using radio frequency identification (RFID). Given that this system would involve many components that were new to Zenitaka, we decided to enlist the cooperation of E.I.Sol Co., Ltd. ('E.I.Sol') as our joint development partner, as they had provided us with a highly practical proposal.
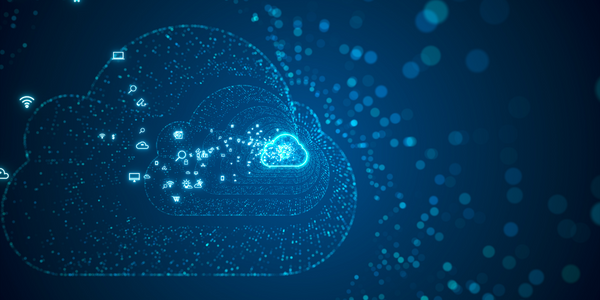
Case Study
Splunk Partnership Ties Together Big Data & IoT Services
Splunk was faced with the need to meet emerging customer demands for interfacing IoT projects to its suite of services. The company required an IoT partner that would be able to easily and quickly integrate with its Splunk Enterprise platform, rather than allocating development resources and time to building out an IoT interface and application platform.
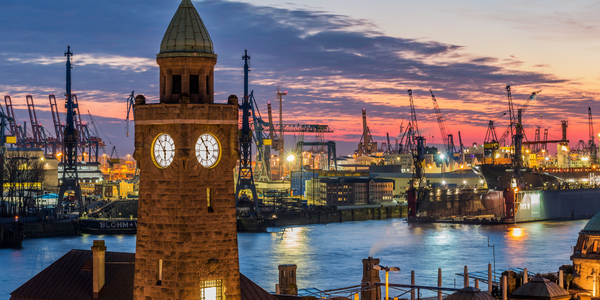
Case Study
Bridge monitoring in Hamburg Port
Kattwyk Bridge is used for both rail and road transport, and it has played an important role in the Port of Hamburg since 1973. However, the increasing pressure from traffic requires a monitoring solution. The goal of the project is to assess in real-time the bridge's status and dynamic responses to traffic and lift processes.
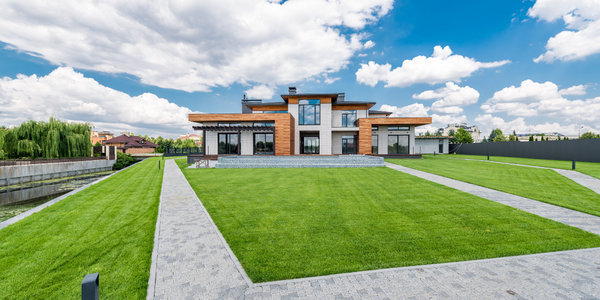
Case Study
Bellas Landscaping
Leading landscaping firm serving central Illinois streamlines operations with Samsara’s real-time fleet tracking solution: • 30+ vehicle fleet includes International Terrastar dump trucks and flatbeds, medium- and light-duty pickups from Ford and Chevrolet. Winter fleet includes of snow plows and salters.
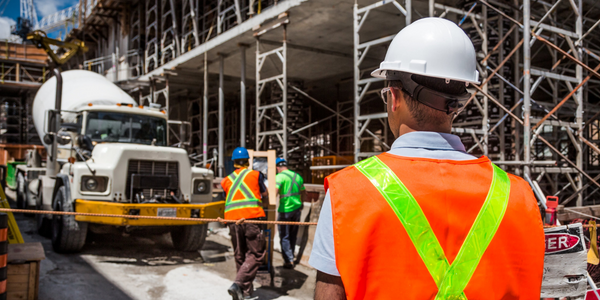
Case Study
Condition Based Monitoring for Industrial Systems
A large construction aggregate plant operates 10 high horsepower Secondary Crusher Drive Motors and associated conveyor belts, producing 600 tons of product per hour. All heavy equipment requires maintenance, but the aggregate producer’s costs were greatly magnified any time that the necessary maintenance was unplanned and unscheduled. The product must be supplied to the customers on a tight time schedule to fulfill contracts, avoid penalties, and prevent the loss of future business. Furthermore, a sudden failure in one of the drive motors would cause rock to pile up in unwanted locations, extending the downtime and increasing the costs.Clearly, preventative maintenance was preferable to unexpected failures. So, twice each year, the company brought in an outside vendor to attach sensors to the motors, do vibration studies, measure bearing temperatures and attempt to assess the health of the motors. But that wasn’t enough. Unexpected breakdowns continued to occur. The aggregate producer decided to upgrade to a Condition Based Monitoring (CBM) sensor system that could continually monitor the motors in real time, apply data analytics to detect changes in motor behavior before they developed into major problems, and alert maintenance staff via email or text, anywhere they happened to be.A wired sensor network would have been cost prohibitive. An aggregate plant has numerous heavy vehicles moving around, so any cabling would have to be protected. But the plant covers 400 acres, and the cable would have to be trenched to numerous locations. Cable wasn’t going to work. The aggregate producer needed a wireless solution.