Hammond Group Reduces IT Costs and Increases Productivity with Aptean Process Manufacturing ERP Ross Edition
Customer Company Size
Large Corporate
Region
- America
Country
- United States
Product
- Aptean Process Manufacturing ERP Ross Edition
Tech Stack
- ERP
Implementation Scale
- Enterprise-wide Deployment
Impact Metrics
- Cost Savings
- Customer Satisfaction
- Productivity Improvements
Technology Category
- Functional Applications - Enterprise Resource Planning Systems (ERP)
Applicable Industries
- Chemicals
Applicable Functions
- Discrete Manufacturing
- Quality Assurance
Use Cases
- Predictive Maintenance
Services
- System Integration
About The Customer
Hammond Group is a chemical company with plants in the US and abroad. The company has a reputation for customer care and was looking to grow and maintain this reputation. They were facing challenges with their existing ERP supplier, including lengthy implementation times and growing overhead costs. They had also experienced two unsuccessful CRM system migrations. The company realized that to grow and maintain its reputation for customer care, it needed to invest in systems that would cut operational costs while still focusing on its customers.
The Challenge
Hammond Group, a chemical company with plants in the US and abroad, was facing growing overhead costs and lengthy implementation time with a tier one ERP supplier. They had also experienced two unsuccessful CRM system migrations. The company realized that to grow and maintain its reputation for customer care, it needed to invest in systems that would cut operational costs while still focusing on its customers. They turned to Aptean Process Manufacturing ERP Ross Edition to handle their financial and production operations.
The Solution
Hammond Group implemented Aptean Process Manufacturing ERP to handle both front and back office needs. The solution provides a portal that allows customers to manage elements of their own accounts, including pulling certificates of analysis, something extremely important to its many customers in the chemical industry. The company has made many additional process improvements that make the 39% savings even more valuable. These improvements include enhanced customer service, global management, product costing, product development, quality assurance, regulatory compliance, sample requests, technical service, and tracking and tracing.
Operational Impact
Quantitative Benefit
Case Study missing?
Start adding your own!
Register with your work email and create a new case study profile for your business.
Related Case Studies.
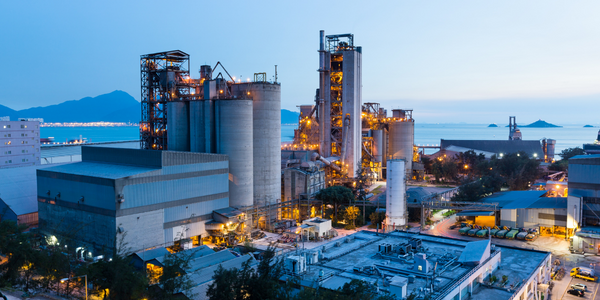
Case Study
Honeywell - Tata Chemicals Improves Data Accessibility with OneWireless
Tata was facing data accessibility challenges in the cement plant control room tapping signals from remote process control areas and other distant locations, including the gas scrubber. Tata needed a wireless solution to extend its control network securely to remote locations that would also provide seamless communication with existing control applications.

Case Study
Advanced Elastomer Systems Upgrades Production
In order to maintain its share of the international market for thermoplastic elastomers AES recently expanded its Florida plant by adding a new production line. While the existing lines were operating satisfactorily using a PROVOX distributed control system with traditional analog I/O, AES wanted advanced technology on the new line for greater economy, efficiency, and reliability. AES officials were anxious to get this line into production to meet incoming orders, but two hurricanes slowed construction.
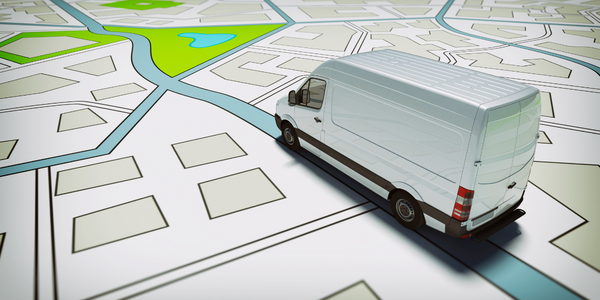
Case Study
Wireless GPS Tracking & Security Monitoring
Enhancing the security of hazardous freight and ensuring compliance with Homeland Security’s Transportation Security Administration mandate that all trains carrying chemicals capable of creating a toxic inhalation condition are equipped with on-board safety monitoring systems.
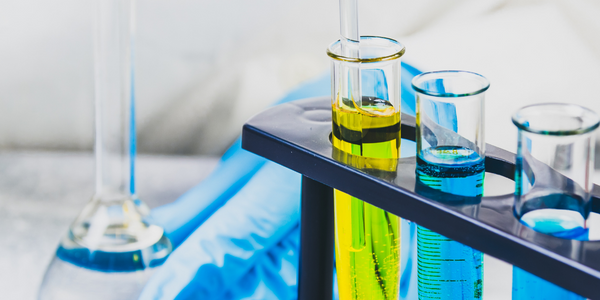
Case Study
Field Device Asset Management For Chemical Company in China
Chinese chemical subsidiary of multinational corporation serves customers throughout the world. Sales offices and research and technology centers are strategically located to provide rapid response to customer requests. Just two workers were assigned to maintain thousands of intelligent instruments in three production units, so they could do little more than react to device issues as they appeared. This costly maintenance method inevitably led to unexpected downtime when a critical instrument failed. Plant management recognized the need to change from reactive to predictive maintenance for all assets, including instruments and control valves, but help was needed in implementing such a technology-based initiative.
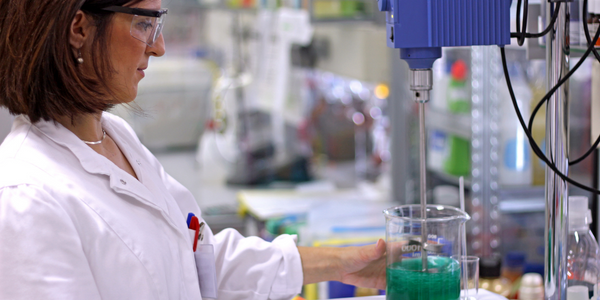
Case Study
Industrial Workforce Mobility for Improved Safety & Operations
Huntsman Corporation, a global manufacturer and marketer of differentiated chemicals, undertook an aggressive program to eliminate injuries, product defects, and environmental releases at their Port Neches facility. Termed “Project Zero”, this program required a completely mobile solution to empower operations and maintenance personnel to capture defects, track work progress and make process and safety related decisions in real-time.