Customer Company Size
Mid-size Company
Region
- Asia
Country
- China
Product
- DesignConcept 2D
- Diamino
- VectorAuto iX6
Tech Stack
- CAD/CAM
- Prototyping Software
- Marker-Making Solution
Implementation Scale
- Enterprise-wide Deployment
Impact Metrics
- Productivity Improvements
- Cost Savings
- Waste Reduction
Technology Category
- Functional Applications - Manufacturing Execution Systems (MES)
- Functional Applications - Product Lifecycle Management Systems (PLM)
- Functional Applications - Remote Monitoring & Control Systems
Applicable Industries
- Automotive
Applicable Functions
- Quality Assurance
Use Cases
- Manufacturing System Automation
- Predictive Maintenance
- Process Control & Optimization
Services
- System Integration
- Software Design & Engineering Services
- Training
About The Customer
Based in Shanghai, China, Guangzan is a supplier of automotive headrests and interior trim. Initially an automotive injection molding manufacturer, the company expanded into automotive seating trim covers, from the cutting of fabric parts to sewing and assembly. Founded in 1994, Guangzan has a production plant in Shanghai and employs a workforce of over 200. The company upgraded its product line to attract more customers and grow its business. However, new revenue opportunities also brought challenges to productivity and cost control, affecting the company's overall growth.
The Challenge
New revenue opportunities brought challenges to productivity and cost control, hindering Guangzan's overall growth. The company found it difficult to meet demand with inflexible production capabilities based mainly on manual die press operations. Increasingly sophisticated seating designs involving smaller, more intricate parts added further manufacturing complexity. Guangzan's business underwent a major transformation after signing a contract with an OEM, leading to a company-wide initiative to streamline production. Guangzan sought a digital cutting solution to provide higher production capacity while ensuring premium quality.
The Solution
At the end of 2015, Guangzan acquired two automotive fabric cutters from a rival CAD/CAM system manufacturer. However, the equipment was not suited to cutting the multi-fabric material used in headrests, leading to technical limitations and material waste. Determined to build a foundation for long-term growth, Guangzan began researching alternative fabric-cutting solutions. With the support of Lectra’s Professional Services, Guangzan re-outfitted its cutting line with DesignConcept 2D prototyping software, Diamino marker-making solution, and VectorAuto iX6 precision fabric cutting equipment. Lectra’s Vector iX6 features a 2x7 mm blade that exerts less pressure on synthetic materials, minimizing friction and the risk of fusion. Combined with Vector iX6’s more sensitive stress sensor, the precision blade enables a reduction of buffer between pieces, significantly lowering the waste ratio. Together with Lectra’s automatic nesting solution, Vector iX6 enables the best possible placement of pieces, saving time and maximizing fabric efficiency.
Operational Impact
Quantitative Benefit
Case Study missing?
Start adding your own!
Register with your work email and create a new case study profile for your business.
Related Case Studies.
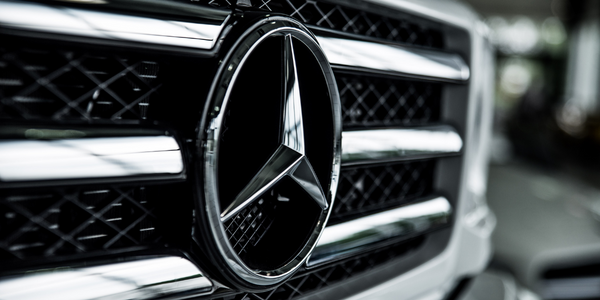
Case Study
Integral Plant Maintenance
Mercedes-Benz and his partner GAZ chose Siemens to be its maintenance partner at a new engine plant in Yaroslavl, Russia. The new plant offers a capacity to manufacture diesel engines for the Russian market, for locally produced Sprinter Classic. In addition to engines for the local market, the Yaroslavl plant will also produce spare parts. Mercedes-Benz Russia and his partner needed a service partner in order to ensure the operation of these lines in a maintenance partnership arrangement. The challenges included coordinating the entire maintenance management operation, in particular inspections, corrective and predictive maintenance activities, and the optimizing spare parts management. Siemens developed a customized maintenance solution that includes all electronic and mechanical maintenance activities (Integral Plant Maintenance).
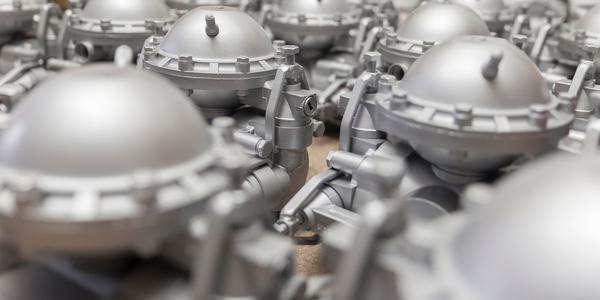
Case Study
Monitoring of Pressure Pumps in Automotive Industry
A large German/American producer of auto parts uses high-pressure pumps to deburr machined parts as a part of its production and quality check process. They decided to monitor these pumps to make sure they work properly and that they can see any indications leading to a potential failure before it affects their process.