Technology Category
- Robots - Autonomous Guided Vehicles (AGV)
- Robots - Wheeled Robots
Applicable Industries
- Automotive
- Telecommunications
Applicable Functions
- Maintenance
- Procurement
Use Cases
- Onsite Human Safety Management
- Smart Contracts
About The Customer
PD Ports is a leading provider of port-centric logistics and warehousing solutions based in the United Kingdom. The company is committed to improving its market position and customer satisfaction by enhancing the efficiency and cost-effectiveness of its internal processes. PD Ports often handles fixed-term contracts and manages a mobile workforce that is frequently away from the office. The company is dedicated to ensuring vehicle safety and improving customer service, and it often deals with customer service queries that require thorough investigation to identify and resolve issues.
The Challenge
PD Ports, a leading provider of port-centric logistics and warehousing solutions, was facing challenges in improving the efficiency and cost-effectiveness of its internal processes. The company was seeking ways to enhance its market position and customer satisfaction. One of the challenges was managing a mobile workforce that often worked away from the office, making vehicle safety checks difficult to handle. Another challenge was handling short-term contracts that required efficient contract and order management over short periods of time, typically handled by employing additional staff. Lastly, the company was dealing with inefficient customer service investigations that required warehouse staff to spend several hours a week investigating to identify and solve issues.
The Solution
PD Ports invested in Nintex K2 Five, a workflow solution that connected with existing processes and technology to enhance efficiency. The company automated over 20 processes, resulting in significant cost and time savings. To address the challenge of mobile workforce, PD Ports used mobile workflow technology to enable employees to carry out vehicle safety checks using a SmartForm on mobile devices. Any issues requiring maintenance were automatically sent directly to the maintenance team by email. To handle short-term contracts efficiently, PD Ports created workflows quickly and easily, improving efficiency in fixed-term contracts. One such workflow helped the company process up to 300 orders a day over a nine-month period. To improve customer service, PD Ports developed a workflow process that captured information from customer queries and automatically collated all the relevant information that managers might need to investigate and resolve the query.
Operational Impact
Quantitative Benefit
Case Study missing?
Start adding your own!
Register with your work email and create a new case study profile for your business.
Related Case Studies.
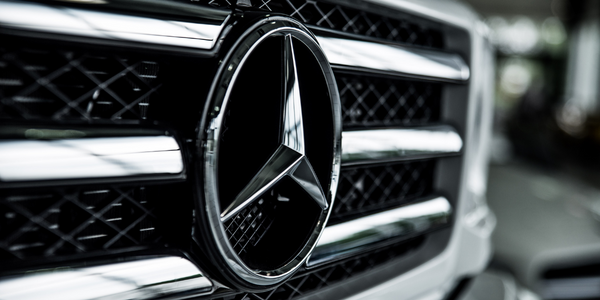
Case Study
Integral Plant Maintenance
Mercedes-Benz and his partner GAZ chose Siemens to be its maintenance partner at a new engine plant in Yaroslavl, Russia. The new plant offers a capacity to manufacture diesel engines for the Russian market, for locally produced Sprinter Classic. In addition to engines for the local market, the Yaroslavl plant will also produce spare parts. Mercedes-Benz Russia and his partner needed a service partner in order to ensure the operation of these lines in a maintenance partnership arrangement. The challenges included coordinating the entire maintenance management operation, in particular inspections, corrective and predictive maintenance activities, and the optimizing spare parts management. Siemens developed a customized maintenance solution that includes all electronic and mechanical maintenance activities (Integral Plant Maintenance).
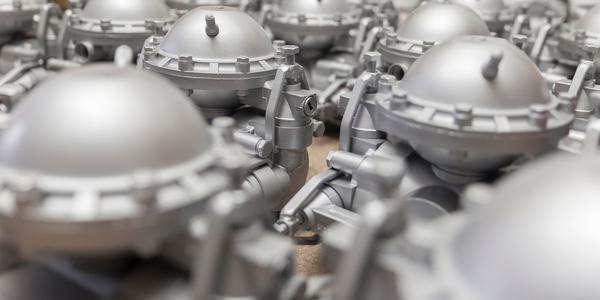
Case Study
Monitoring of Pressure Pumps in Automotive Industry
A large German/American producer of auto parts uses high-pressure pumps to deburr machined parts as a part of its production and quality check process. They decided to monitor these pumps to make sure they work properly and that they can see any indications leading to a potential failure before it affects their process.