GLOVIA G2 Delivers Streamlined Operations and Foundation for Efficient Global Business
Company Size
1,000+
Region
- America
- Asia
Country
- Japan
- United States
Product
- GLOVIA G2
Tech Stack
- Oracle database
Implementation Scale
- Enterprise-wide Deployment
Impact Metrics
- Cost Savings
- Productivity Improvements
Technology Category
- Functional Applications - Enterprise Resource Planning Systems (ERP)
Applicable Industries
- Automotive
Applicable Functions
- Discrete Manufacturing
- Procurement
Use Cases
- Inventory Management
- Manufacturing System Automation
Services
- System Integration
About The Customer
Keihin Corporation is a $1.8 billion principal manufacturer for Honda that produces fuel systems, electronic controls, and heating, ventilating and air conditioning products. The company is headquartered in Tokyo, Japan and has manufacturing facilities in Japan, North America, Canada and other countries. Keihin is a long established Japanese company, with roots going back to 1950, but the corporation in its present form derives from a series of mergers in 1997. In the United States alone, Keihin has annual revenue of around $600 million and its global turnover runs into billions. This is big business and information technology is one of the mainstays of that business.
The Challenge
Keihin Corporation, a principal manufacturer for Honda, was facing a business problem where their three North American facilities needed a single solution to replace their existing, individually procured applications. This was necessary to support the increasing fluidity of customer schedules. The company was operating in an intensely competitive industry and needed to have quick and accurate information. Their customer schedules were very fluid and they were becoming more so by the week, month, and year as the car makers continued to respond to increasing consumer demands. In 1995, one of Keihin’s pre-merger companies, Indiana Precision Technology (KIPT), realized they were wasting time and duplicating effort by using standalone PCs running a variety of individually procured applications. The rapid growth and associated disjointed applications, combined with more stringent and fluid customer schedules, made an imperative case to change business processes and implement an ERP system with the goal to streamline operations, increase operational responsiveness, and meet customers’ growing demands as effectively as possible.
The Solution
Keihin chose Glovia’s extended ERP solution, GLOVIA G2, to replace their standalone applications with one proven, robust solution and to streamline operations, synchronize cycle times, tighten inventory control, and increase operational responsiveness. Glovia is now installed at Keihin’s three North American facilities. The transition was very smooth and clean. They imported some data from KIPT, then added their own financials and bills of materials. Glovia professional services helped them to get the different modules up and running. The Keihin Corporation has now implemented GLOVIA G2 in its three North American companies and the common software platform simplifies the incorporation of new factories into the manufacturing chain. The product is so rich in features that the company only utilizes those for which there is an immediate business need.
Operational Impact
Quantitative Benefit
Case Study missing?
Start adding your own!
Register with your work email and create a new case study profile for your business.
Related Case Studies.
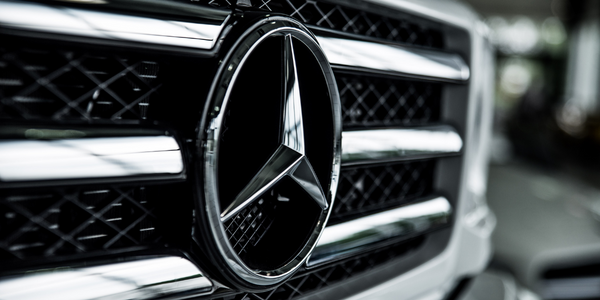
Case Study
Integral Plant Maintenance
Mercedes-Benz and his partner GAZ chose Siemens to be its maintenance partner at a new engine plant in Yaroslavl, Russia. The new plant offers a capacity to manufacture diesel engines for the Russian market, for locally produced Sprinter Classic. In addition to engines for the local market, the Yaroslavl plant will also produce spare parts. Mercedes-Benz Russia and his partner needed a service partner in order to ensure the operation of these lines in a maintenance partnership arrangement. The challenges included coordinating the entire maintenance management operation, in particular inspections, corrective and predictive maintenance activities, and the optimizing spare parts management. Siemens developed a customized maintenance solution that includes all electronic and mechanical maintenance activities (Integral Plant Maintenance).
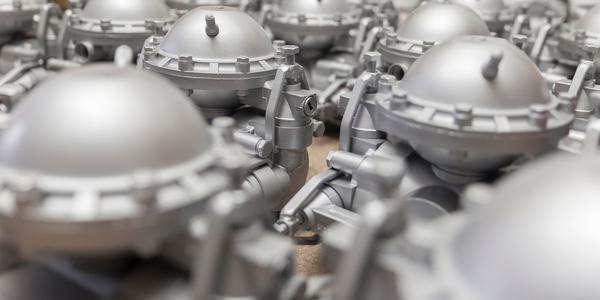
Case Study
Monitoring of Pressure Pumps in Automotive Industry
A large German/American producer of auto parts uses high-pressure pumps to deburr machined parts as a part of its production and quality check process. They decided to monitor these pumps to make sure they work properly and that they can see any indications leading to a potential failure before it affects their process.