Global Tire Manufacturer Fully Automates Integration Testing with Genrocket Test Data Automation
Customer Company Size
Large Corporate
Region
- America
Country
- United States
- Canada
Product
- GenRocket Test Data Automation (TDA)
- GenRocket Data Generators
- GenRocket Data Receivers
Tech Stack
- Microservices Architecture
- NoSQL Databases
- Jenkins CI/CD Pipeline
- Containerization
Implementation Scale
- Enterprise-wide Deployment
Impact Metrics
- Productivity Improvements
- Cost Savings
- Customer Satisfaction
Technology Category
- Application Infrastructure & Middleware - Data Exchange & Integration
- Analytics & Modeling - Real Time Analytics
- Functional Applications - Remote Monitoring & Control Systems
Applicable Industries
- Automotive
Applicable Functions
- Quality Assurance
- Business Operation
Services
- Software Design & Engineering Services
- System Integration
- Training
About The Customer
A multinational tire company designs and manufactures tires for various vehicles, including airplanes, automobiles, bicycles, earthmovers, farm equipment, heavy-duty trucks, and motorcycles. The company operates globally, selling its diverse product line through retail channels and maintaining manufacturing facilities in distributed locations to streamline its supply chain. The company values innovation, environmental sustainability, and safety, with major manufacturing plants in the U.S. and Canada staffed by thousands of employees. As a digital enterprise, the company follows DevOps practices, transitioning monolithic applications to modular information systems using a microservices architecture.
The Challenge
The company needed to modernize its critical software testing platform, E2E, to support full-scale end-to-end testing for all integration applications. The platform required a transformation to become a fully automated framework capable of testing all messaging components exchanged by integration middleware. The QA team faced a significant challenge in generating high-volume test data with a wide variety of data patterns. The complexity of creating this test data was overwhelming, leading the team to spend as much time generating data as on actual testing. They needed a solution that could provide synthetic test data in volume and on-demand to support their continuous integration and testing processes.
The Solution
The company adopted GenRocket Test Data Automation (TDA) to address their test data challenges. After a successful Proof of Concept (POC), the QA team underwent training at GenRocket University to familiarize themselves with the platform. They learned to use GenRocket’s API to trigger Real-Time Synthetic Test Data Generation directly from the E2E testing framework. The team scheduled GenRocket TDA to generate on-demand test data continuously throughout a 24-hour testing cycle, specifying the volume and variability needed for their test cases. GenRocket’s component architecture, with over 250 Data Generators and 60 Data Receivers, allowed the QA team to generate synthetic data with control over format, variability, and volume. This data was then augmented with actual production data to create realistic messages for testing E2E. The integration of GenRocket into the company’s automated test environment resulted in more comprehensive testing, faster pace, and improved code quality.
Operational Impact
Quantitative Benefit
Case Study missing?
Start adding your own!
Register with your work email and create a new case study profile for your business.
Related Case Studies.
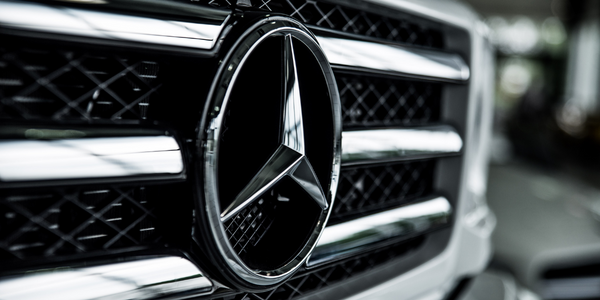
Case Study
Integral Plant Maintenance
Mercedes-Benz and his partner GAZ chose Siemens to be its maintenance partner at a new engine plant in Yaroslavl, Russia. The new plant offers a capacity to manufacture diesel engines for the Russian market, for locally produced Sprinter Classic. In addition to engines for the local market, the Yaroslavl plant will also produce spare parts. Mercedes-Benz Russia and his partner needed a service partner in order to ensure the operation of these lines in a maintenance partnership arrangement. The challenges included coordinating the entire maintenance management operation, in particular inspections, corrective and predictive maintenance activities, and the optimizing spare parts management. Siemens developed a customized maintenance solution that includes all electronic and mechanical maintenance activities (Integral Plant Maintenance).
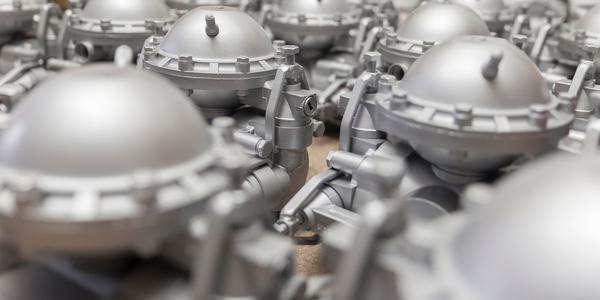
Case Study
Monitoring of Pressure Pumps in Automotive Industry
A large German/American producer of auto parts uses high-pressure pumps to deburr machined parts as a part of its production and quality check process. They decided to monitor these pumps to make sure they work properly and that they can see any indications leading to a potential failure before it affects their process.