Global Biopharmaceutical Company Recognizes Annual Operational Savings of $60,000 per Facility with Avetta
Company Size
1,000+
Region
- America
Country
- United States
Product
- Avetta
Tech Stack
- Lotus Notes
Implementation Scale
- Enterprise-wide Deployment
Impact Metrics
- Cost Savings
- Customer Satisfaction
- Productivity Improvements
Technology Category
- Application Infrastructure & Middleware - Data Exchange & Integration
- Platform as a Service (PaaS) - Connectivity Platforms
Applicable Industries
- Healthcare & Hospitals
- Pharmaceuticals
Applicable Functions
- Procurement
- Quality Assurance
Use Cases
- Regulatory Compliance Monitoring
- Remote Asset Management
- Supply Chain Visibility
Services
- System Integration
- Training
About The Customer
The customer is a global, research-based biopharmaceutical company with a workforce of 28,000 employees. The company is committed to maintaining strict internal safety standards, referred to as “Global Technical Standards,” to ensure that all contractors are properly trained, certified, and reviewed according to OSHA standards. The company undertakes a wide range of jobs, including asbestos abatement, lead abatement, confined space work, excavations, fall protection, crane lifts, and helicopter lifts. The Senior Safety Construction Specialist at the company is responsible for ensuring that all contractors meet these stringent safety requirements. However, managing several hundred contractors at a single site had become an overwhelming task, leading to the need for a more efficient and cost-effective approach to supply chain risk management.
The Challenge
Faced with a ballooning administrative workload, combined with the refusal to compromise his company’s strict safety standards, a Senior Safety Construction Specialist in North Chicago had a decision to make: hire more staff and absorb the cost of salary, health care insurance, and training—or look for a more efficient and cost-effective approach to de-risking his supply chain. His company, a global, research-based biopharmaceutical company with a workforce of 28,000, has set a strict internal safety initiative referred to as “Global Technical Standards.” It’s the job of this Senior Safety Construction Specialist to make sure contractors at his facility are properly trained, certified, and reviewed, according to OSHA standards. But with several hundred contractors working at his site alone, managing them all and meeting company goals had become too much work for one person. The problem wasn’t just the amount of time required to execute the reviews. Internal staff had no automated way of knowing who was due for review, whose review was late, or who hadn’t been reviewed yet. There was no trigger in place that would tell them when contractors were up for review. The company did have an electronic database of information for contractors, but it did not provide detailed information, such as certifications or training—not even an indication of whether the contractor was qualified to perform work onsite. With overflowing file cabinets, an increasingly complex supply chain, and the ever-present concern over contractor risk, something needed to change.
The Solution
Recognizing that without an automated system he could not comply with the company’s Global Technical Standards, the Senior Safety Construction Specialist approached his managers and suggested they look into a third-party vendor to assist with supply chain risk management. They contacted three different companies, including Avetta, and had each present before the evaluation team, which included individuals from contract administration and directors from other departments outside of Health & Safety. After the vetting process, the team was unanimous in its selection. Avetta offered a bit more than the others, with an easy-to-navigate application and a straightforward flag system. Today, staff members in the purchasing department log in to Avetta, check whether a contractor is in the system, and then verify the contractor’s flag color. If a prospective contractor is not in the Avetta system, the buyer will let them know they have to enroll, comply with the program, and send in their EHS information. Contractors have been complying, and the process of issuing POs is easier than ever. Contractors, in some cases, are leveraging the system to make changes or improvements in their business practices. The critical task of checking on contractors is now easier and faster. The Avetta dashboard is especially convenient and instantly conveys high-level information. Staff can see everything that’s going on, check the pie chart at the top of the home screen, and see which contractors are green, yellow, and red. They can also look at documents such as confined space programs or OSHA 300 logs easily.
Operational Impact
Quantitative Benefit
Case Study missing?
Start adding your own!
Register with your work email and create a new case study profile for your business.
Related Case Studies.
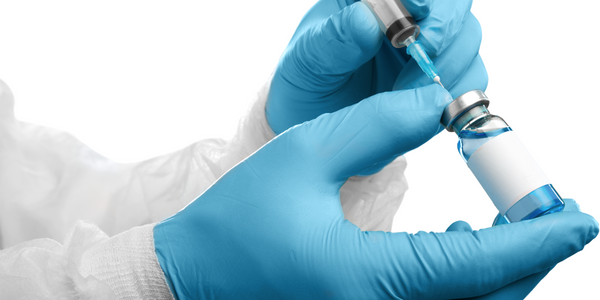
Case Study
Case Study: Pfizer
Pfizer’s high-performance computing software and systems for worldwide research and development support large-scale data analysis, research projects, clinical analytics, and modeling. Pfizer’s computing services are used across the spectrum of research and development efforts, from the deep biological understanding of disease to the design of safe, efficacious therapeutic agents.
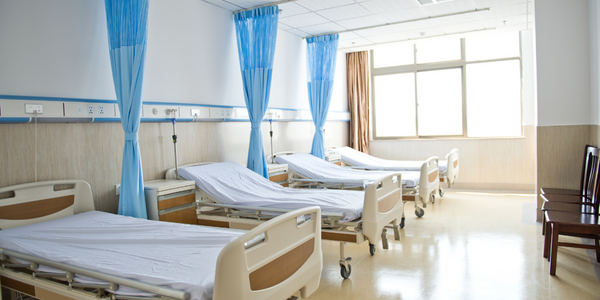
Case Study
Hospital Inventory Management
The hospital supply chain team is responsible for ensuring that the right medical supplies are readily available to clinicians when and where needed, and to do so in the most efficient manner possible. However, many of the systems and processes in use at the cancer center for supply chain management were not best suited to support these goals. Barcoding technology, a commonly used method for inventory management of medical supplies, is labor intensive, time consuming, does not provide real-time visibility into inventory levels and can be prone to error. Consequently, the lack of accurate and real-time visibility into inventory levels across multiple supply rooms in multiple hospital facilities creates additional inefficiency in the system causing over-ordering, hoarding, and wasted supplies. Other sources of waste and cost were also identified as candidates for improvement. Existing systems and processes did not provide adequate security for high-cost inventory within the hospital, which was another driver of cost. A lack of visibility into expiration dates for supplies resulted in supplies being wasted due to past expiry dates. Storage of supplies was also a key consideration given the location of the cancer center’s facilities in a dense urban setting, where space is always at a premium. In order to address the challenges outlined above, the hospital sought a solution that would provide real-time inventory information with high levels of accuracy, reduce the level of manual effort required and enable data driven decision making to ensure that the right supplies were readily available to clinicians in the right location at the right time.
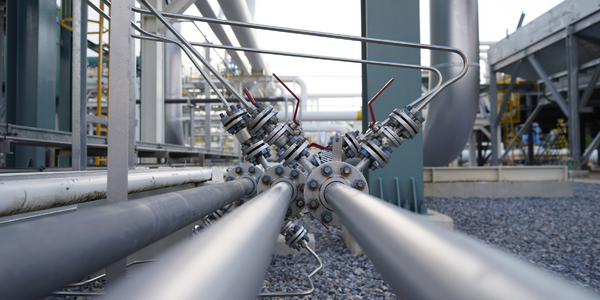
Case Study
Gas Pipeline Monitoring System for Hospitals
This system integrator focuses on providing centralized gas pipeline monitoring systems for hospitals. The service they provide makes it possible for hospitals to reduce both maintenance and labor costs. Since hospitals may not have an existing network suitable for this type of system, GPRS communication provides an easy and ready-to-use solution for remote, distributed monitoring systems System Requirements - GPRS communication - Seamless connection with SCADA software - Simple, front-end control capability - Expandable I/O channels - Combine AI, DI, and DO channels
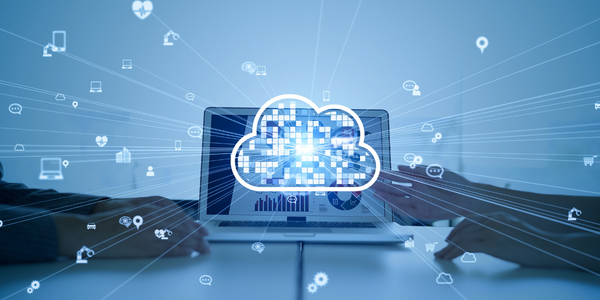
Case Study
Fusion Middleware Integration on Cloud for Pharma Major
Customer wanted a real-time, seamless, cloud based integration between the existing on premise and cloud based application using SOA technology on Oracle Fusion Middleware Platform, a Contingent Worker Solution to collect, track, manage and report information for on-boarding, maintenance and off-boarding of contingent workers using a streamlined and Integrated business process, and streamlining of integration to the back-end systems and multiple SaaS applications.
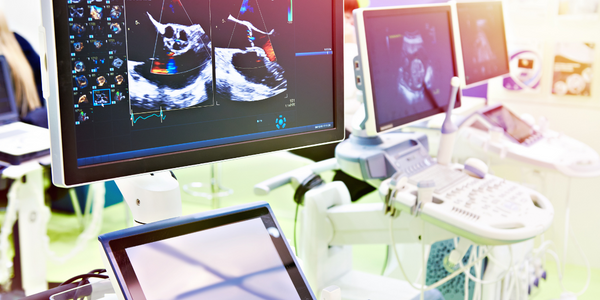
Case Study
Driving Digital Transformations for Vitro Diagnostic Medical Devices
Diagnostic devices play a vital role in helping to improve healthcare delivery. In fact, an estimated 60 percent of the world’s medical decisions are made with support from in vitrodiagnostics (IVD) solutions, such as those provided by Roche Diagnostics, an industry leader. As the demand for medical diagnostic services grows rapidly in hospitals and clinics across China, so does the market for IVD solutions. In addition, the typically high cost of these diagnostic devices means that comprehensive post-sales services are needed. Wanteed to improve three portions of thr IVD:1. Remotely monitor and manage IVD devices as fixed assets.2. Optimizing device availability with predictive maintenance.3. Recommending the best IVD solution for a customer’s needs.