Gestamp Reduces Production Printouts by 50% and Improves Document and Information Quality
Customer Company Size
Large Corporate
Region
- America
- Europe
- Asia
Country
- Argentina
Product
- SE EAM Suite
- SE ECM Suite
Tech Stack
- Web-based Modules
- ERP Integration
Implementation Scale
- Enterprise-wide Deployment
Impact Metrics
- Cost Savings
- Productivity Improvements
- Customer Satisfaction
Technology Category
- Functional Applications - Enterprise Asset Management Systems (EAM)
Applicable Industries
- Automotive
Applicable Functions
- Quality Assurance
- Business Operation
Services
- Software Design & Engineering Services
- System Integration
About The Customer
Gestamp Automação is an international group focused on the creation, development, and manufacturing of components and metal sets for automobiles. It is currently present in 18 countries and has 57 production centers and 13 I+D+i centers (meaning “Research + Development + Technological Innovation” in Spanish) with over 13,500 employees. The company's 2008 earnings totaled €2.4 million. Through the use of global solutions, Gestamp has become a reference provider for clients such as Volkswagen, Ford, PSA, Honda, Porsche, BMW, Fiat, and Iveco, among others. The company is committed to maintaining high standards of quality and compliance, as evidenced by its certifications in ISO/TS 16949 and ISO 14000. Gestamp's extensive presence and significant workforce highlight its influence and capability in the automotive sector.
The Challenge
The non-conformities generated during each external audit due to deficient document management affecting each area, as well as the need to integrate documents throughout the entire organization were the main needs that prompted Corporação Gestamp to invest in SoftExpert solutions. The company faced challenges in managing non-conformities generated with every audit due to deficient document management affecting each area. Additionally, there was a need to improve document management automation to simplify and streamline the document flow of each area and that linked to the different departments. The company also needed to significantly reduce the time loss cost due to increased bureaucracy because it lacked a system that automates most management processes. Furthermore, there was a need to motivate the areas to assume their responsibility for document management, granted that a high percentage of this task falls under the responsibility of the quality area. Lastly, the company aimed to improve calibration management by transferring the use of a bureaucratic, simplistic, and limited model found on the Intranet to a professional software package widely recognized in the market.
The Solution
Gestamp decided to implement SoftExpert's SE Suite, which is designed for document and quality management with a focus on maintaining the ISO TS 16949 and ISO 14000 certifications. The SE Suite minimizes management time by cutting down on bureaucracy and automating most of the actions that were previously developed using countless model and structure spreadsheets that, over time, became obsolete, requiring constant revision and reevaluation. The SE Suite offers a set of multilingual modules that are natively integrated and fully Web-based to automate the processes required to improve and optimize the different business areas at organizations. This boosts the quality of management, cuts operating costs, and facilitates compliance with the main market standards and regulations. The suite is integrated with the main ERP systems on the market through already available connectors or through customized connectors developed based on the client's specific needs. This integration ensures that the work completed over a period of several years is not wasted and allows employees with a longer history at the company to easily adapt to the new system due to its similarity to Windows.
Operational Impact
Quantitative Benefit
Case Study missing?
Start adding your own!
Register with your work email and create a new case study profile for your business.
Related Case Studies.
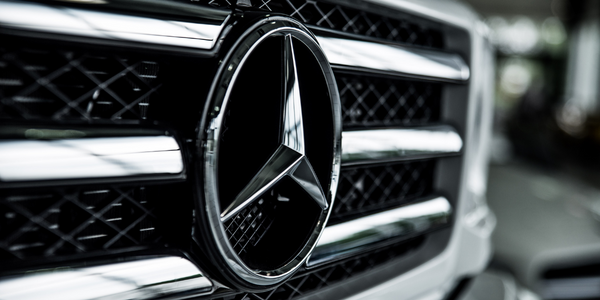
Case Study
Integral Plant Maintenance
Mercedes-Benz and his partner GAZ chose Siemens to be its maintenance partner at a new engine plant in Yaroslavl, Russia. The new plant offers a capacity to manufacture diesel engines for the Russian market, for locally produced Sprinter Classic. In addition to engines for the local market, the Yaroslavl plant will also produce spare parts. Mercedes-Benz Russia and his partner needed a service partner in order to ensure the operation of these lines in a maintenance partnership arrangement. The challenges included coordinating the entire maintenance management operation, in particular inspections, corrective and predictive maintenance activities, and the optimizing spare parts management. Siemens developed a customized maintenance solution that includes all electronic and mechanical maintenance activities (Integral Plant Maintenance).
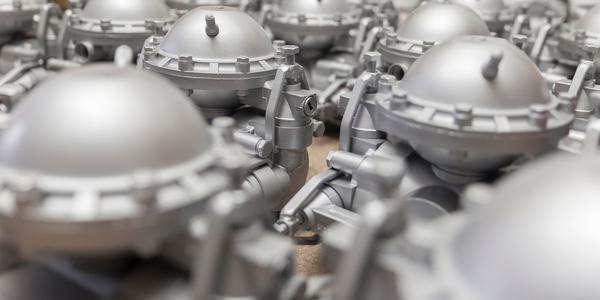
Case Study
Monitoring of Pressure Pumps in Automotive Industry
A large German/American producer of auto parts uses high-pressure pumps to deburr machined parts as a part of its production and quality check process. They decided to monitor these pumps to make sure they work properly and that they can see any indications leading to a potential failure before it affects their process.