Customer Company Size
Large Corporate
Region
- Asia
Country
- India
Product
- SAP ERP 6.0
- IBM DB2 database
- IBM Power 520 servers
- IBM System Storage DS5020 disk system
Tech Stack
- IBM AIX
- IBM DB2
Implementation Scale
- Enterprise-wide Deployment
Impact Metrics
- Productivity Improvements
- Cost Savings
Technology Category
- Application Infrastructure & Middleware - Database Management & Storage
- Functional Applications - Enterprise Resource Planning Systems (ERP)
Applicable Industries
- Automotive
Applicable Functions
- Discrete Manufacturing
- Procurement
Use Cases
- Manufacturing System Automation
- Inventory Management
Services
- System Integration
- Cloud Planning, Design & Implementation Services
About The Customer
Gabriel India Ltd is the flagship company of the Anand Group, which is among India’s leading automotive component companies. The group consists of 19 companies that manufacture original equipment and components for the automotive industry both within India and internationally. Gabriel India specializes in ride control products (shock-absorbers, front forks and struts), which it supplies directly to major car, motorcycle and heavy goods vehicle manufacturers, and also sells through agents and distributors as aftermarket products. Founded in 1961, the company has its headquarters and main plant in Pune and operates at five other manufacturing sites in Nashik, Dewas, Hosur, Khandsa and Parwanoo. It employs around 2,900 people, produces 20 million units per year, and generates annual revenues of approximately 7 billion Indian Rupees.
The Challenge
Gabriel India Ltd operates six main manufacturing sites across the country, and plans to open additional plants in northern India. To streamline operations and support growth, the company wanted to move to a single central enterprise resource planning (ERP) solution that would support manufacturing processes as well as finance and distribution. Its existing architecture – Intel processor-based HP Proliant machines running Microsoft Windows Server and Microsoft SQL Server 2005 databases – was struggling to deliver adequate performance even for SAP Business One, and the predicted resource requirements for SAP ERP were far higher.
The Solution
The company upgraded from its existing SAP Business One solution to SAP ERP 6.0, and migrated from HP hardware and Microsoft SQL Server to a fully IBM solution: an IBM DB2 database running on two IBM Power 520 servers and supported by an IBM System Storage DS5020 disk system. The company also upgraded its network infrastructure, providing faster access to SAP applications for users across the country. Running IBM DB2 on IBM AIX enables features such as Deep Compression, which allows companies to reduce data storage requirements by up to 70 percent while also boosting database performance. This is particularly valuable in database-intensive environments such as SAP ERP, where improved database throughput can have a significant effect on overall response times.
Operational Impact
Quantitative Benefit
Case Study missing?
Start adding your own!
Register with your work email and create a new case study profile for your business.
Related Case Studies.
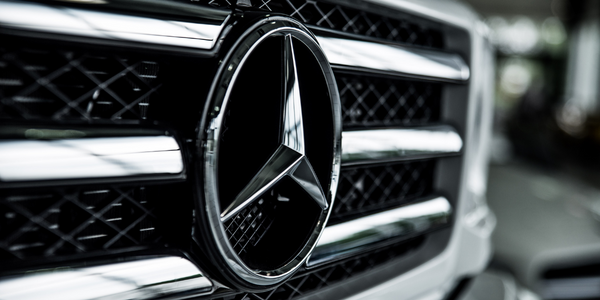
Case Study
Integral Plant Maintenance
Mercedes-Benz and his partner GAZ chose Siemens to be its maintenance partner at a new engine plant in Yaroslavl, Russia. The new plant offers a capacity to manufacture diesel engines for the Russian market, for locally produced Sprinter Classic. In addition to engines for the local market, the Yaroslavl plant will also produce spare parts. Mercedes-Benz Russia and his partner needed a service partner in order to ensure the operation of these lines in a maintenance partnership arrangement. The challenges included coordinating the entire maintenance management operation, in particular inspections, corrective and predictive maintenance activities, and the optimizing spare parts management. Siemens developed a customized maintenance solution that includes all electronic and mechanical maintenance activities (Integral Plant Maintenance).
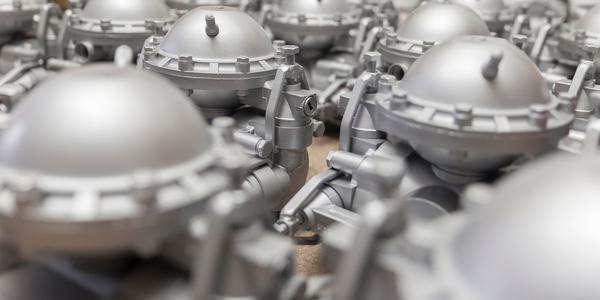
Case Study
Monitoring of Pressure Pumps in Automotive Industry
A large German/American producer of auto parts uses high-pressure pumps to deburr machined parts as a part of its production and quality check process. They decided to monitor these pumps to make sure they work properly and that they can see any indications leading to a potential failure before it affects their process.