Company Size
1,000+
Region
- America
Country
- United States
Product
- JDA® Warehouse Labor Management
Tech Stack
- SAP enterprise resource planning
- warehouse management systems
Implementation Scale
- Enterprise-wide Deployment
Impact Metrics
- Cost Savings
- Productivity Improvements
Technology Category
- Functional Applications - Warehouse Management Systems (WMS)
Applicable Industries
- Equipment & Machinery
Applicable Functions
- Warehouse & Inventory Management
Use Cases
- Inventory Management
- Warehouse Automation
Services
- System Integration
About The Customer
Briggs & Stratton is the world’s largest producer of air-cooled gasoline engines for outdoor power equipment. The company designs, manufactures, markets and services these engines for original equipment manufacturers (OEMs) worldwide. Briggs & Stratton engines are incorporated into products as diverse as lawnmowers, race cars, farm equipment, generators, pressure washers, pumps and welders, as well as many other industrial and commercial applications. Briggs & Stratton’s replacement parts division ships aftermarket and service parts worldwide from two facilities: a 300,000 square foot distribution center (DC), and a 225,000 square foot outside facility. It handles between 70,000 to 75,000 SKUs representing $40 million to $45 million in inventory, including parts for acquired brands such as Generac (now Briggs & Stratton Home Power) and Simplicity (now Briggs & Stratton Yard Power). The two facilities have both distribution and packaging operations, and ship approximately 26 million pieces annually.
The Challenge
Briggs & Stratton, the world’s largest producer of air-cooled gasoline engines for outdoor power equipment, was facing a challenge in its warehouse labor management. The company's replacement parts division ships aftermarket and service parts worldwide from two facilities. It handles between 70,000 to 75,000 SKUs representing $40 million to $45 million in inventory. Prior to 2003, the Menomonee Falls Distribution Center (MFDC) had no standardized way for associates to do their jobs or to measure productivity. The MFDC management team felt they could get greater productivity if they standardized work methods, set goals and measured results. To help research this hypothesis the University of Wisconsin Supply Chain Consortium conducted a study that suggested there was significant opportunity for return on investment if the MFDC deployed labor management technology.
The Solution
Briggs & Stratton implemented JDA Warehouse Labor Management first in its traditional distribution operations. The company turned the system on in “monitoring mode” one month before the actual go-live date to get a baseline on existing performance. As is common with most companies JDA has worked with, Briggs & Stratton found it was working at only 67 percent of standard for its operations. However, within a month of going live the company was able to reduce its pick, pack and ship headcount by about 18 percent while maintaining throughput. Soon after, performance improved to 100 percent to 110 percent of standard. Following completion of the DC implementation, Briggs & Stratton turned its focus on its packaging operations. These occupy half of the facility, with about 95 percent of all parts being kitted, representing approximately 26 million pieces annually. The light manufacturing environment required a different approach to labor management. The entire workflow from receiving and putaway through the kitting operations to transfer to the DC had to be included. Measuring performance of the kitting process entailed incorporation of machine-based timings not present in traditional distribution operations. The flexibility of JDA’s solution made implementation straightforward.
Operational Impact
Quantitative Benefit
Case Study missing?
Start adding your own!
Register with your work email and create a new case study profile for your business.
Related Case Studies.

Case Study
Smart Water Filtration Systems
Before working with Ayla Networks, Ozner was already using cloud connectivity to identify and solve water-filtration system malfunctions as well as to monitor filter cartridges for replacements.But, in June 2015, Ozner executives talked with Ayla about how the company might further improve its water systems with IoT technology. They liked what they heard from Ayla, but the executives needed to be sure that Ayla’s Agile IoT Platform provided the security and reliability Ozner required.

Case Study
IoT enabled Fleet Management with MindSphere
In view of growing competition, Gämmerler had a strong need to remain competitive via process optimization, reliability and gentle handling of printed products, even at highest press speeds. In addition, a digitalization initiative also included developing a key differentiation via data-driven services offers.
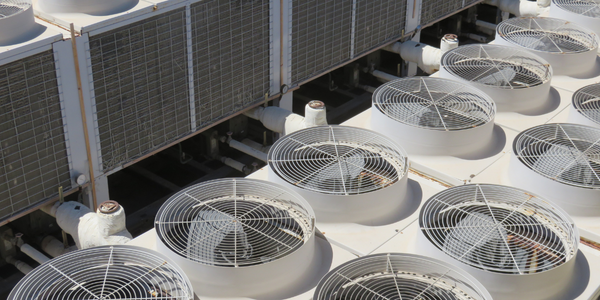
Case Study
Predictive Maintenance for Industrial Chillers
For global leaders in the industrial chiller manufacturing, reliability of the entire production process is of the utmost importance. Chillers are refrigeration systems that produce ice water to provide cooling for a process or industrial application. One of those leaders sought a way to respond to asset performance issues, even before they occur. The intelligence to guarantee maximum reliability of cooling devices is embedded (pre-alarming). A pre-alarming phase means that the cooling device still works, but symptoms may appear, telling manufacturers that a failure is likely to occur in the near future. Chillers who are not internet connected at that moment, provide little insight in this pre-alarming phase.

Case Study
Premium Appliance Producer Innovates with Internet of Everything
Sub-Zero faced the largest product launch in the company’s history:It wanted to launch 60 new products as scheduled while simultaneously opening a new “greenfield” production facility, yet still adhering to stringent quality requirements and manage issues from new supply-chain partners. A the same time, it wanted to increase staff productivity time and collaboration while reducing travel and costs.

Case Study
Integration of PLC with IoT for Bosch Rexroth
The application arises from the need to monitor and anticipate the problems of one or more machines managed by a PLC. These problems, often resulting from the accumulation over time of small discrepancies, require, when they occur, ex post technical operations maintenance.
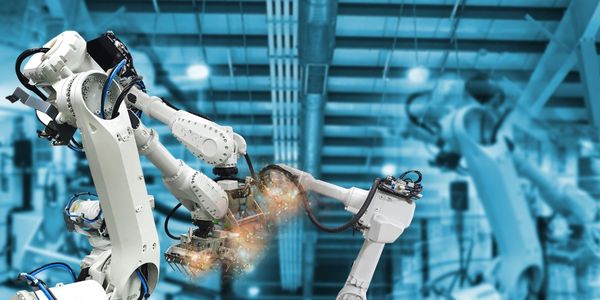
Case Study
Robot Saves Money and Time for US Custom Molding Company
Injection Technology (Itech) is a custom molder for a variety of clients that require precision plastic parts for such products as electric meter covers, dental appliance cases and spools. With 95 employees operating 23 molding machines in a 30,000 square foot plant, Itech wanted to reduce man hours and increase efficiency.